Du béton compacté routier (BCR) pour une plate-forme de stockage de véhicules en transit : le site CGMV du port de Brégaillon
Performances techniques, durabilité, optimisation structurelle, préservation des ressources, réduction des coûts, protection de l’environnement, remise en circulation rapide… Autant d’avantages qui expliquent l’engouement pour la technique du béton compacté routier (BCR) ! En voici un nouvel exemple avec la plate-forme de stockage de véhicules en transit, réalisée sur le site du Comptoir général maritime varois (CGMV) du port de Brégaillon, à La Seyne-sur-Mer.
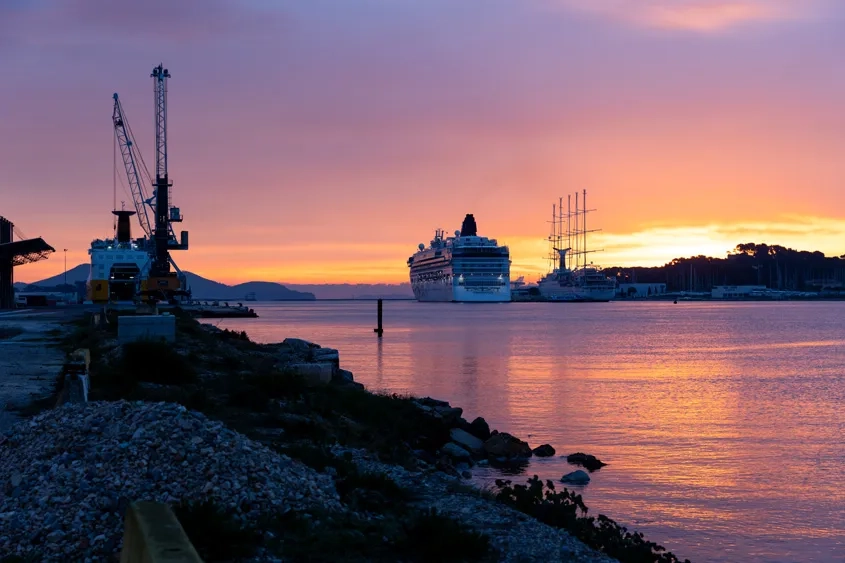
État des lieux
Sur la façade maritime française, le port de Brégaillon de La Seyne-sur-Mer est niché au sein de la rade de Toulon, qui compte parmi les sites les mieux abrités de la Méditerranée occidentale et les plus sûrs en raison de la présence de la marine nationale.
Spécialisé dans le fret intraméditerranéen, il se situe à la croisée des axes de communication de l’Europe : il permet de connecter la vallée du Rhône au nord , l’arc méditerranéen Espagne-Italie et l’Afrique du Nord. C’est l’un des sites logistiques majeurs de l’Europe du Sud avec le port de Toulon, le port Saint-Louis du Mourillon, Fos Distriport, plate-forme logistique maritime, la plate-forme rail-route Clésud de Miramas et l’aéroport international de Marseille-Provence, première plate-forme de fret aérien après Paris.
Offrant déjà un accès rapide et direct au réseau autoroutier (l’A50 est située à dix minutes environ), le port a récemment fait l’objet d’importants travaux pour le connecter au réseau ferré national. Menés par la chambre de commerce et d’industrie (CCI) du Var, ceux-ci ont renforcé l’intermodalité du site et la compétitivité du port. Apprécié pour sa flexibilité opérationnelle (le port est ouvert 24/24 h et 365 jours par an), il cherche à répondre aux divers besoins des industriels européens et mondiaux ainsi qu’à ceux des prestataires de transport et des distributeurs. Il consolide ainsi la position stratégique du Var sur le marché de la logistique du sud de l’Europe.
Aujourd’hui, le port de Brégaillon s’enrichit d’une nouvelle plate-forme de stockage de véhicules en transit, construite sur un ancien site industriel de concassage de granulats. La CCI du Var a assuré à la fois la maîtrise d’ouvrage et la maîtrise d’œuvre du projet. Pour le réaliser, c’est à l’entreprise Colas (agence de La Seyne-sur-Mer) qu’elle a fait appel. Le béton compacté routier (BCR), technique choisie pour réaliser cette nouvelle plate-forme, a, quant à lui, été fabriqué et livré par la société Vicat.
Projet
Ce projet de transformation et de remise en état du site du CGMV s’inscrit dans la politique de diversification et d’intensification de l’activité et des échanges maritimes sur le port de Brégaillon.
« Au départ, nous avions conçu la plate-forme de stockage comme une structure de chaussée conventionnelle, c’est-à-dire en matériaux bitumineux. Mais, après réflexion au sein de nos services techniques, la décision a été prise de penser l’aménagement différemment, afin de mieux prendre en compte les particularités du projet (stockage de véhicules, charges statiques, risque de fuites de carburant et d’huile de moteur), les objectifs fixés par la CCI en matière de politique d’investissement (durabilité, optimisation des coûts des projets), d’exploitation et d’entretien des infrastructures (mise en service rapide sous soixante-douze heures au maximum, peu de travaux d’entretien) et l’engagement de la CCI en faveur de l’environnement (préservation des ressources naturelles, limitation des impacts) », explique Jean-Christophe Barbagelata, directeur des Opérations et Travaux de la CCI.
Recherche d'une solution technique adaptée
« Le site nécessitait tout d’abord d’importants travaux de terrassement, sur lesquels nous voulions réaliser une structure de chaussée solide, homogène, capable de résister à la fois aux charges des véhicules et aux embruns marins », poursuit Jean-Christophe Barbagelata. Or, le BCR est réputé pour ses performances mécaniques et sa durabilité face aux sollicitations provoquées par les charges et les conditions climatiques. Il résiste également aux fuites de carburant et d’huile de moteur. En outre, grâce à ces qualités, le BCR ne nécessite que très peu d’interventions, d’où un coût d’entretien faible. Cela représente, aux yeux d’un gestionnaire, un avantage économique non négligeable.
« Nous savions que le BCR avait été utilisé pour refaire les quais de maintenance du port de La Ciotat en 2007 et, plus récemment, pour rénover les quais du port de La Rochelle. Nous avons donc rencontré Olivier Piselli, manager de la société Béton Vicat, ainsi que Christophe Fontaine, directeur de la société Colas (Var), qui nous ont proposé une étude personnalisée pour la réalisation du projet. Après réflexion, nous avons décidé que la technique du BCR était la plus adaptée à notre ouvrage comme à notre budget », conclut Jean-Christophe Barbagelata de la CCI.
Études
La formulation du BCR
La formulation du BCR a été menée conformément à la norme NF P 98 128 « Béton Compacté Routier », afin de satisfaire aux deux objectifs suivants :
- Un mélange le plus dense possible pour une maniabilité optimale ;
- Un mélange ayant les performances mécaniques adéquates et d’un coût minimal.
La formule du BCR retenue se compose de :
- Granulats : 0/2 C, 6/16 C, 11/22 C – Granulats concassés Someca Le Revest.
- Ciment : CEM II/A-LL 42.5 R CE NF Vicat Peille.
- Eau.
- Adjuvants : plastifiant et retardateur de prise.
Les propriétés du mélange ont été mesurées en laboratoire, avant le début des travaux :
- À l’état frais, la mesure de la masse volumique a donné la valeur de 2,33 t/m3 ;
- À l’état durci, les mesures de résistance à la traction et du module ont permis de déterminer la classe mécanique du BCR, conformément à la norme NF P 98 128 « Béton Compacté Routier ». Il s’agit de la classe T4.
Formules et données
Formulation du BCR
La production du BCR a été assurée à la centrale de BPE de Béton Vicat. Une centrale discontinue ELBA, avec malaxeur horizontal de 2,00 m3, assurait le malaxage à froid des constituants.
DEFIPERF BCR 10 % D3 S1 CEMII/A-LL 42,5 R CE NF VICAT
- Granulats : 0/2, 6/16 et 11/22 – Granulats concassés Someca Le Revest.
- Ciment CEMII/A-LL 42,5 R CE NF VICAT.
- Eau.
- Adjuvants : plastifiant et retardateur de prise.
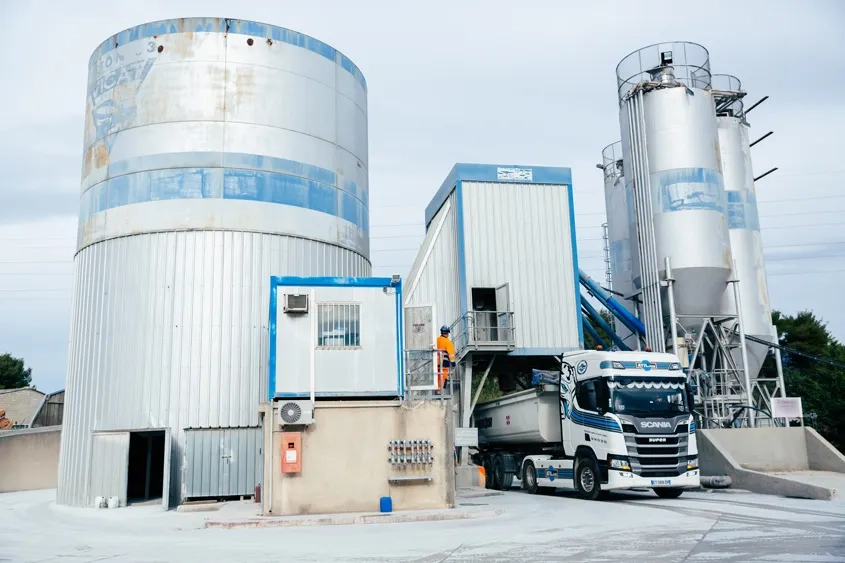
Le dimensionnement de la structure
Le dimensionnement de la structure a été effectué avec les hypothèses suivantes :
- Trafic estimé à la mise en service : T5 = 25 PL/j
- Portance de la plate-forme : PF2 = 50 MPa
Classe mécanique du BCR : T4
- Durée de vie : vingt ans
Le calcul mené avec le logiciel Alizé donne la structure de chaussée suivante :
- Couche de forme constituée de deux couches :
- Une couche inférieure en GNT 0/60, d’épaisseur 25 cm ;
- Une couche supérieure en GNT 0/20, d’épaisseur 15 cm.
- Revêtement en BCR : 25 cm.
« Le choix du BCR et le dimensionnement de la structure de la plate-forme de stockage ont été faits afin de créer une assise solide, durable et homogène », explique Jean-Christophe Barbagelata.
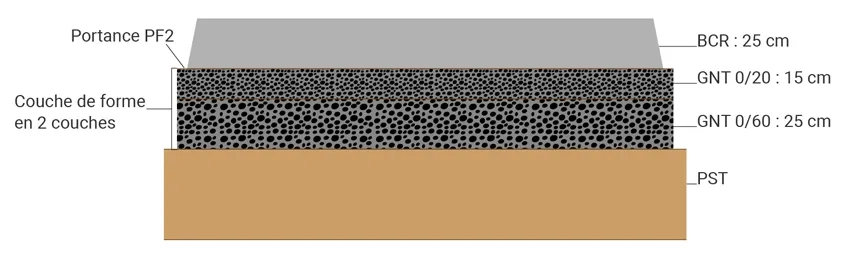
Le BCR : un choix judicieux
« La solution du BCR a permis de résoudre simultanément toutes les problématiques posées par la construction de la plate-forme de stockage des véhicules en transit », résume Olivier Piselli, manager de Béton Vicat. Cette solution offre trois avantages déterminants :
Sur le plan technique
Il s’agit d’une structure de chaussée confectionnée avec un béton compacté routier (BCR). Le BCR est constitué des mêmes ingrédients (granulats, ciment, eau, adjuvants) qu’un béton traditionnel, dit « plastique », mais il diffère par sa composition (proportions des différents constituants). En effet, il contient plus de gravillons, moins de sable et, surtout, beaucoup moins d’eau qu’un béton plastique. De ce fait, c’est un matériau « sec », à forte densité granulaire et avec une faible teneur en fines. Il requiert, pour sa mise en place, une énergie de compactage élevée.
Bien formulé, le BCR permet de rapidement développer des résistances mécaniques élevées, souvent plus fortes qu’un béton traditionnel et, de surcroît, avec un dosage en ciment plus faible.
Sur le plan structurel
Un revêtement en BCR est un ouvrage possédant les mêmes qualités structurelles (module d’élasticité, performances mécaniques, tenue à la fatigue) qu’un revêtement en béton dit « plastique ». Il est donc conçu et dimensionné selon les mêmes critères.
Sur le plan financier
À performances mécaniques égales, les revêtements en BCR sont moins chers que les revêtements en béton dit « plastique ». En effet, en comparaison, un revêtement en BCR bénéficie des avantages suivants :
- Un dosage en ciment plus faible, de l’ordre de 20 % ;
- Une plus grande rapidité de mise en œuvre ;
- Une remise en service plus rapide.
En outre, les revêtements en BCR ne requièrent pas l’emploi de goujons, ni d’armatures, ni l’utilisation de coffrages, contrairement aux revêtements en béton plastique.
Mise en œuvre de la structure en BCR
La mise en œuvre de la structure en BCR s’effectue à l’aide d’un matériel habituellement utilisé pour la construction de chaussées souples ou semi-rigides (niveleuses, finisseurs, compacteurs, etc.).
« Avant le démarrage des travaux, nous avons remis au maître d’œuvre, pour validation, un plan précisant l’organisation de la mise en œuvre du BCR. Ce plan définit le séquençage de la mise en place du matériau (sens de bétonnage, longueur et largeur des bandes, réalisation des bandes en peigne c’est-à-dire une bande sur deux) et l’emplacement des joints de construction. », précise Sébastien MARTIN, chef de service technique PACA de Colas Sud-Est.
La mise en œuvre de la structure en BCR s’effectue à l’aide d’un matériel habituellement utilisé pour la construction de chaussées souples ou semi-rigides.
« L’objectif, pour nous, est d’assurer une mise en œuvre continue, de maîtriser les délais d’exécution et de minimiser les joints de construction », ajoute Christophe Fontaine, directeur de l’agence Colas de La Seyne-sur-Mer.
Pour la plate-forme de stockage de véhicules en transit du port de Brégaillon, la mise en œuvre s’est déroulée en trois étapes :
- Les travaux préparatoires ;
- L’exécution de la couche de forme ;
- L’exécution du revêtement en BCR, qui comprend plusieurs opérations : production et transport du BCR ; régalage du matériau ; nivellement ; compactage ; protection et exécution des joints de retrait.
De la production du BCR jusqu’à sa mise en place, l’entreprise a pris des précautions afin d’éviter la ségrégation et la variation de la teneur en eau du matériau.
Les travaux préparatoires
Les travaux préparatoires ont consisté à réaliser les opérations suivantes :
- Un nettoyage soigné du site ;
- L’exécution du support de la plate-forme par déblais /remblais, à l’aide d’un chargeur à chenilles,
- Un relevé topographique détaillé ;
- Des travaux d’assainissement ;
- Un compactage soigné à l’aide d’un compacteur de type V4, suivi éventuellement de purges et d’un comblement ;
- Des contrôles (uni, dévers, etc.).
Exécution de la couche de forme
Après avoir effectué les travaux préparatoires, l’entreprise a réalisé une couche de forme en grave non traitée (GNT), d’une épaisseur totale de 40 cm, en vue de conférer à la plate-forme support de chaussée une portance minimale PF2 (50 ≤ EV2 < 80 MPa). Cette couche de forme a été réalisée en deux temps :
- Une couche inférieure en grave non traitée GNT 0/60 mm, d’épaisseur 25 cm ;
- Une couche supérieure en grave non traitée GNT 0/20 mm, d’épaisseur 15 cm.
Chacune des deux couches a été mise en œuvre en réalisant successivement les opérations suivantes :
- Régalage de la GNT à la niveleuse ;
- Humidification ;
- Compactage soigné.
« Cette dernière opération est très importante, car elle vise à conférer à la plate-forme support un niveau de portance permettant ultérieurement le compactage efficace de la couche du BCR (effet d’enclume). À la suite du compactage, la plate-forme support a fait l’objet d’un contrôle de la portance, effectué par l’essai à la plaque. Les mesures ont été réalisées en plusieurs points de la plate-forme afin de vérifier que l’objectif visé pour la portance a bien été atteint (homogénéité et niveau). Toutes les valeurs obtenues se situaient dans la plage de portance visée (de 50 à 80 MPa) et étaient donc conformes aux spécifications du cahier des charges », poursuit Christophe Fontaine.
“Cette dernière opération, le compactage, est très importante, car elle vise à conférer à la plate-forme support un niveau de portance permettant ultérieurement le compactage efficace de la couche du BCR.”
Exécution du revêtement en BCR
La mise en œuvre du revêtement en BCR comprend deux étapes :
- Fabrication et transport du BCR ;
- Mise en œuvre du BCR.
Fabrication et Transport du BCR
Le BCR a été fabriqué à la centrale de BPE de Béton Vicat. Pour assurer l’homogénéité du mélange, le temps de malaxage a été augmenté par rapport à celui d’un béton dit « plastique » : il est de l’ordre de trois minutes par gâchée.
« Comme le BCR est pauvre en pâte, la hauteur de chute du matériau, lors du chargement des camions à benne ainsi que lors du déchargement dans le finisseur, a été réduite au minimum pour éviter la ségrégation du matériau », précise Olivier Piselli.
Le BCR est ensuite acheminé depuis la centrale jusqu’au chantier, par camions à semi-benne. « Comme le BCR est très sensible aux variations de la teneur en eau, les camions sont équipés de bâches pour réduire l’évaporation de l’eau du matériau sous l’effet des conditions climatiques », ajoute Olivier Piselli.
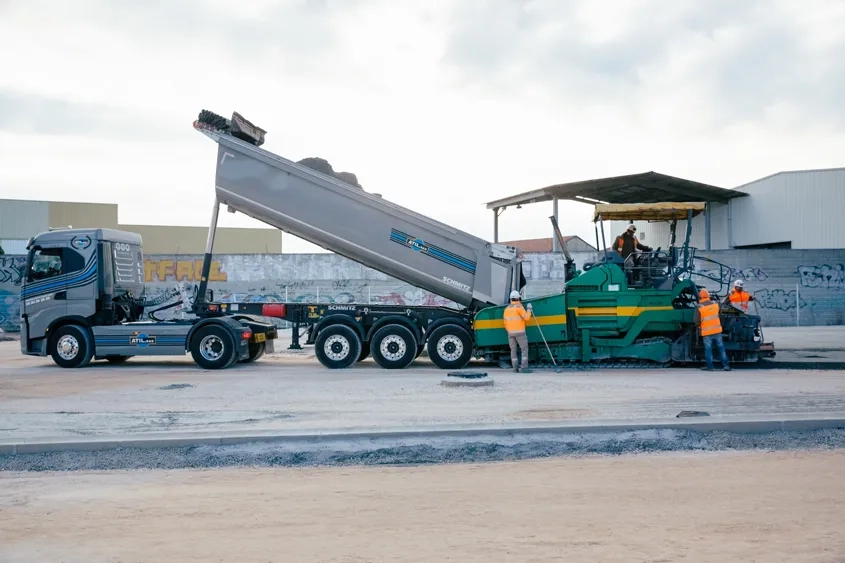
Mise en œuvre du BCR
Avant la mise en œuvre du BCR, l’entreprise a procédé systématiquement à l’arrosage de la couche de forme afin d’éviter que le BCR ne perde son eau par percolation. Cette opération a été suivie par la mise en œuvre du BCR, en deux couches successives séparées d’un délai de 24 heures minimum (pour garantir l’obtention d’une portance suffisante de la première couche, permettant la réalisation de la deuxième couche), et respectant le processus suivant :
- Répandage d’une première couche de BCR, à l’aide d’un finisseur, d’épaisseur 15 cm en sortie de table.
- Compactage de cette première couche à l’aide d’un atelier de deux compacteurs vibrants (un compacteur vibrant tandem VT2 et un petit compacteur vibrant PV2) afin d’obtenir la compacité visée. « Nous avons réalisé une planche d’essai en début de chantier, explique Sébastien Martin. Elle nous a permis de définir l’atelier de mise en œuvre. »
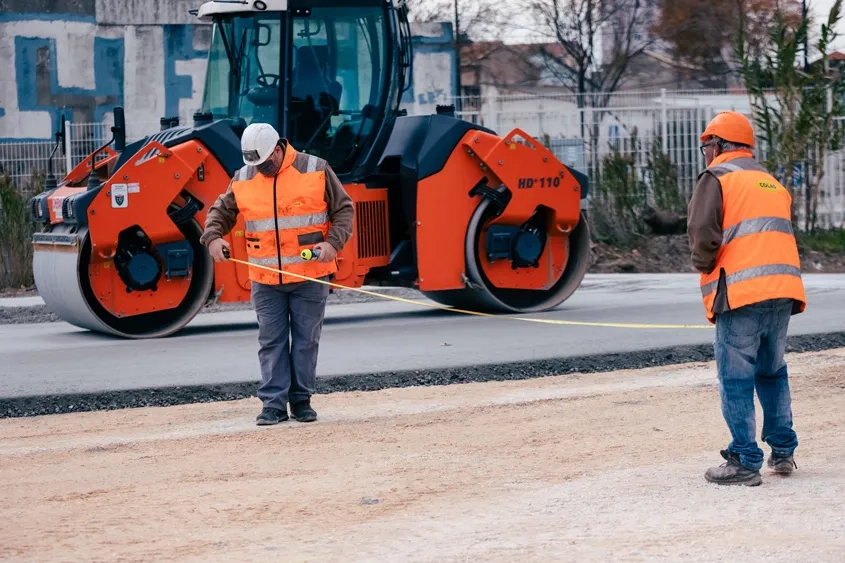
- La protection de cette première couche de BCR contre la dessiccation a été obtenue par humidification de la surface à l’eau et non par la pulvérisation d’un produit de cure qui aurait engendré un décollement à l’interface entre les deux couches de BCR et par conséquent une fragilité structurelle.
- Avant la mise en place de la deuxième couche de BCR, la surface de la première couche a été légèrement scarifiée et grattée à l’aide d’un peigne puis arrosée à l’eau sans laisser de flaques.
- Répandage de la deuxième couche de BCR, à l’aide d’un finisseur, d’épaisseur 17 cm en sortie de table.
- Compactage soigné du BCR à l’aide des deux compacteurs vibrants VT2 et PV2.
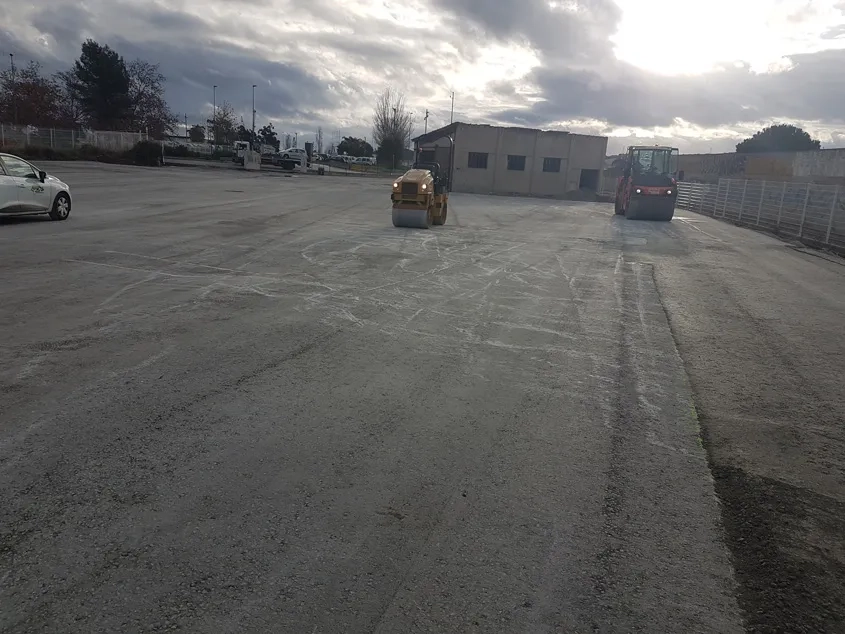
- La protection du revêtement en BCR contre la dessiccation par la pulvérisation d’un produit de cure filmogène pour prise hydraulique, à raison de 250 g/m2.
- Les joints d’arrêt de fin de journée sont réalisés par une coupure verticale sur toute l’épaisseur du béton. Le lendemain, un simple recalage et l’humidification du joint suffisent lors de la reprise du chantier.
- Afin d’éviter la fissuration anarchique liée au retrait du béton, l’entreprise a réalisé, le lendemain du bétonnage, des joints de retrait transversaux par sciage du revêtement en BCR sur le quart de son épaisseur, espacés de 4 m (maillage 4 m x 4 m ou largeur d’application de la bande).
- Sciage des joints de construction longitudinaux et de reprise pour un rendu plus esthétique.
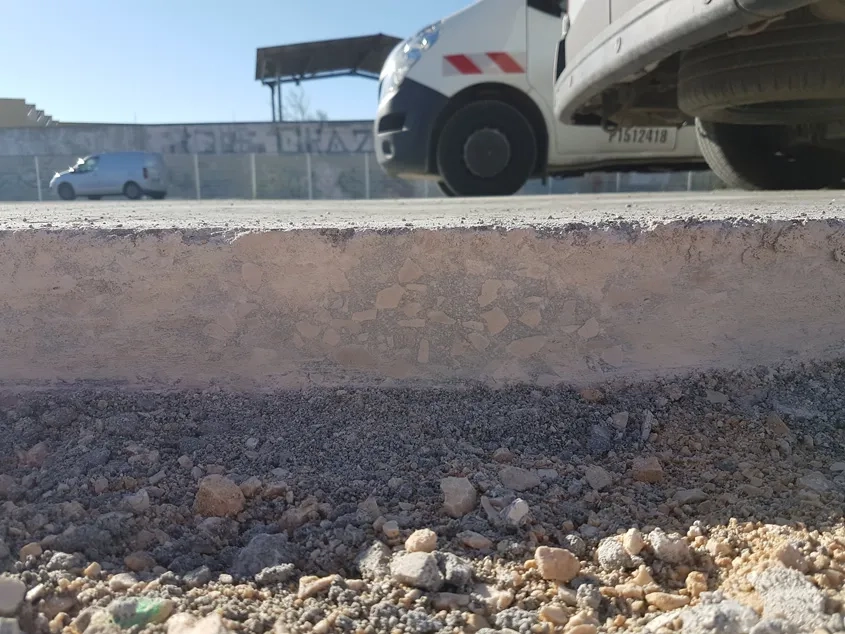
Bon à savoir
Le Béton Compacté Routier (BCR)
Le BCR est obtenu avec les mêmes constituants de base que le béton classique, à savoir un mélange de :
- Ciment : conforme à la norme NF EN 197-1, de type CEM I, CEM II, CEM III, CEM IV ou CEM V.
- Granulats : conformes aux normes NF EN 13242 et NF P 18 545. Ils constituent de 75 à 85 % du volume total et peuvent être roulés (sable siliceux) ou concassés (sable calcaire, gravier, grave, etc.). Pour limiter les problèmes de ségrégation et en vue d’une meilleure qualité de surface, la dimension maximale du granulat doit être inférieure à 20 mm et le fuseau granulométrique divisé en plusieurs fractions ou coupures granulométriques (par exemple : 0/3-3/8-8/16). Toutes les fractions doivent avoir un indice de concassage supérieur à 30 % dans le cas d’un trafic faible et d’environ 100 % dans le cas d’un trafic élevé. Ces granulats ont un indice de plasticité non mesurable et une teneur en matière organique inférieure à 0,2 %.
- Eau : conforme à la norme NF P 98 100. Le BCR est un béton sec à affaissement nul. Sa teneur en eau doit donc être faible.
- Adjuvants, éventuellement : dans des proportions spécifiques et avec précaution. De fait, la courte durée du malaxage et la faible quantité d’eau limitent l’effet de ces adjuvants, d’où une augmentation du dosage pour en accroître l’efficacité.
Les plus courants sont des retardateurs de prise, permettant d’augmenter la durée de transport et de mise en place du béton, de maintenir longtemps la consistance recherchée du BCR ou de ménager la contrainte des reprises de bétonnage. D’autres sont des réducteurs d’eau, permettant une amélioration de l’homogénéité de la pâte. Les accélérateurs de prise sont peu utilisés et les fluidifiants sont exclus, car ils peuvent provoquer un ressuage ou une déformation excessive à la suite du compactage.
Contrôles
Qualité oblige, l’entreprise a mis en place une série de contrôles pour vérifier :
- Régulièrement la teneur en eau du BCR, afin de garantir l’obtention d’un mélange homogène et compact.
- L’épaisseur du revêtement en sortie de table et par calcul de Q/S (Tonnage mis en œuvre/Surface exécutée).
- La compacité en place au gamma densimètre. La compacité mesurée a été supérieure à la compacité visée : C% > 98%.
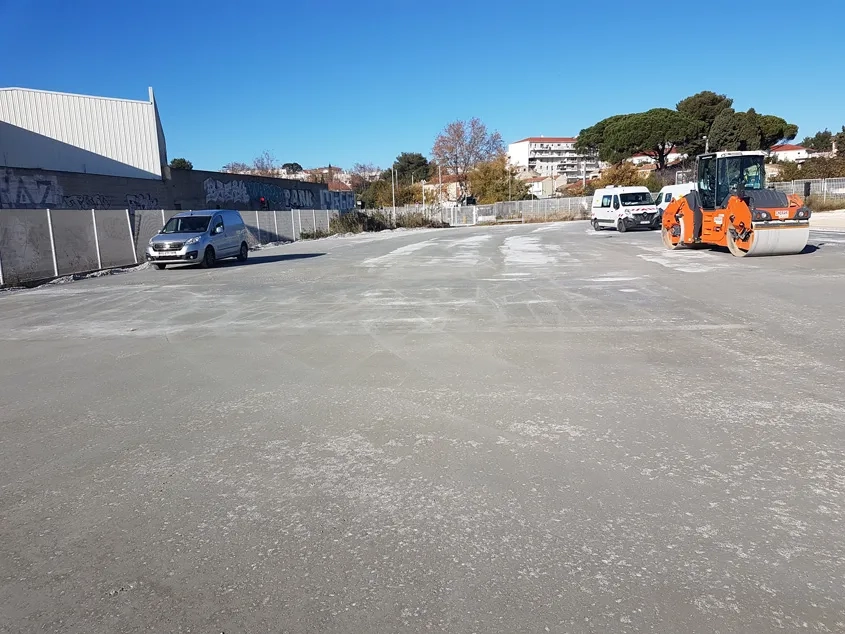
Bilan
L’entreprise Colas a réalisé un revêtement en BCR, d’épaisseur 25 cm, sur une surface de 4 000 m2. « Au total, ce chantier aura nécessité 1 050 m3 de BCR, soit environ 250 tonnes de ciment », résume Olivier Piselli.
Le chantier s’est déroulé durant le mois de décembre 2020. Les travaux ont été réalisés dans les délais et le résultat est très satisfaisant. La mise en œuvre s’est achevée en décembre 2020. Après trois jours sans circulation, le trafic de poids lourds a été de nouveau autorisé.
La réussite de cette opération est due à l’implication totale de l’ensemble des acteurs de l’opération (la CCI, Béton Vicat, Colas).
Le cas de la plate-forme de stockage de véhicules sur le port de Brégaillon n’étant pas isolé, l’utilisation de la technique du BCR pourrait être envisagée, à l’avenir, sur de nombreux sites partageant les mêmes problématiques.
Vidéos, Guides techniques, organisation de Journées techniques, découvrez les outils mis à votre disposition sur : www.infociments.fr/routes/
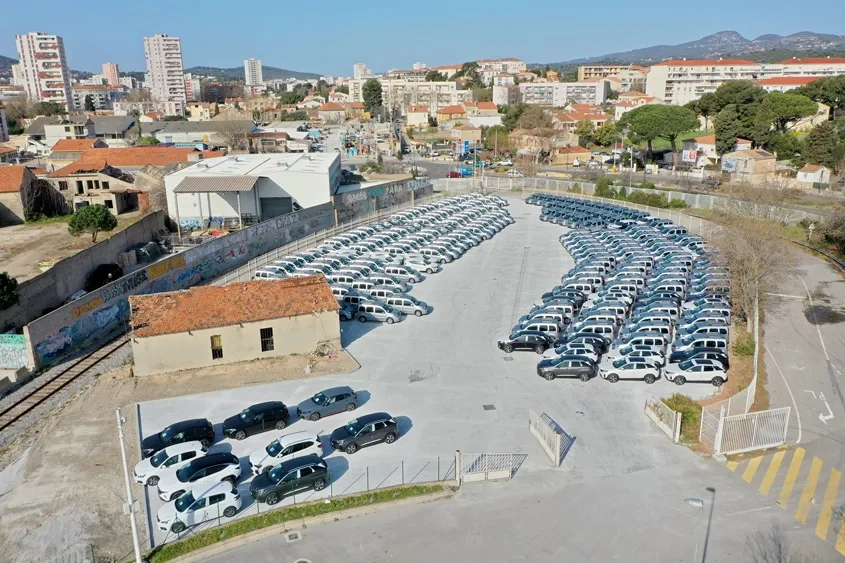
Localiser la réalisation
Principaux intervenants
- Maîtrise d’ouvrage : Chambre de commerce et d’industrie (CCI)
- Maître d’œuvre : Chambre de commerce et d’industrie (CCI)
- Entreprise : Colas
- Fournisseur du béton compacté routier : Béton Vicat
COMMENTAIRES
LAISSER UN COMMENTAIRE