Pont de l’Atlantique sur le canal de Panama
Avec une portée centrale de 530 m, le pont de l’Atlantique est le plus grand pont haubané du monde intégralement en béton. Un ouvrage exceptionnel, fruit de nombreux exploits techniques.
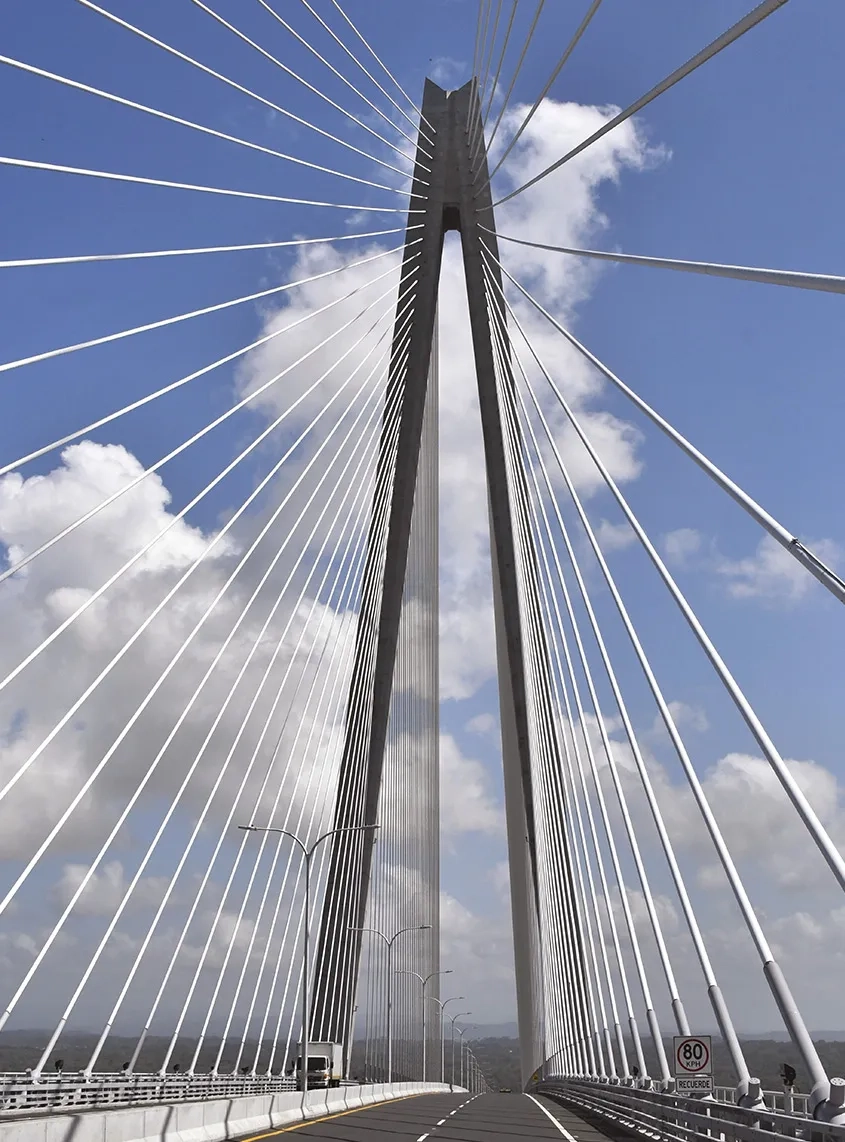
Depuis son ouverture en 1914, le canal de Panama constitue un point de passage stratégique pour le commerce maritime mondial. Traversant un isthme étroit selon un axe nord-sud, il permet de relier les océans Atlantique et Pacifique sur une distance de 77 km. Son élargissement, décidé par le gouvernement panaméen pour augmenter le trafic et permettre le passage des navires Post-Panamax, parmi les plus gros de la planète, a donné lieu à des travaux titanesques qui se sont achevés par l’inauguration du nouveau canal en juin 2016, après neuf années de chantier.
Record du monde de portée
Alors que le canal coupe le Panama en deux, les liaisons d’une rive à l’autre sont rares. Il a fallu attendre 1962 pour voir la mise en service d’un premier lien fixe, le pont des Amériques, un ouvrage routier en arc à treillis situé dans la capitale, Panama City, au-dessus de l’entrée côté Pacifique du canal. Un deuxième ouvrage, le pont à haubans du Centenaire, a été ouvert en 2004 à une quinzaine de kilomètres au nord du pont des Amériques, principalement pour désengorger ce dernier. Ce n’est qu’à l’occasion de l’élargissement du canal que le gouvernement décida de créer un 3e pont, enjambant cette fois le canal du côté Atlantique, au niveau de Colón, la deuxième ville du pays. Cet ouvrage permettrait de passer des continents sud à nord-américains indépendamment du fonctionnement des écluses du canal à Gatún, empruntées jusqu’alors par les automobilistes. Il a confié la responsabilité de sa maîtrise d’ouvrage à l’Autorité du canal de Panama (ACP).
En octobre 2012, l’ACP a attribué le marché de la construction du pont de l’Atlantique à Vinci Construction Grands Projets, en concurrence avec deux consortiums internationaux.
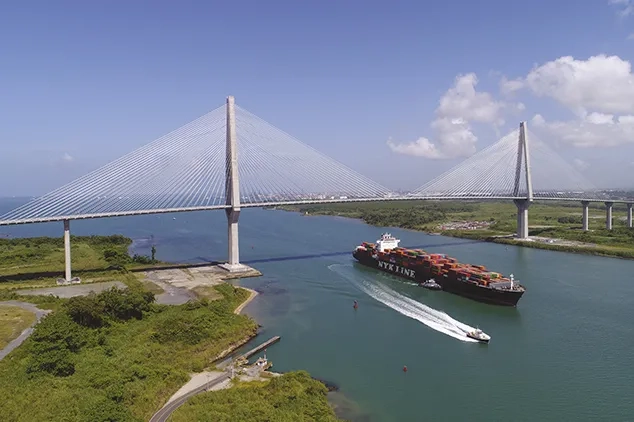
Le marché porte sur la réalisation de l’ensemble des ouvrages à 2 x 2 voies traversant le canal sur une longueur de 4,6 km, dont 3,1 km d’ouvrages d’art exceptionnels : les viaducs d’approche sur 2 km et le pont de l’Atlantique proprement dit, long de 1 050 m.
Avec une portée centrale de 530 m ménageant un tirant d’air de 75 m de haut pour laisser passer les porte-conteneurs de type « Post-Panamax », ce dernier établit un record : il s’agit du plus long pont haubané en béton au monde. « La zone de construction, sur la façade atlantique, est soumise à une ambiance marine parmi les plus corrosives du monde », explique Gilles Dumoulin, directeur du projet pour Vinci Construction Grands Projets. « C’est en raison de cette adversité climatique qu’une solution technique entièrement en béton armé a été préférée par l’ACP à l’emploi d’une structure métallique. » Le pont haubané est ainsi composé d’un tablier en béton armé précontraint très fin (23,5 m de large pour 2,8 m d’épaisseur) constitué de deux poutres caissons. Chacun des 128 voussoirs de l’ouvrage est suspendu à ses extrémités par une paire de haubans. Les 256 haubans, répartis en deux nappes latérales inclinées, sont ancrés sur la moitié supérieure des pylônes de 212,5 m de hauteur dont les jambes forment un « delta » de pente 10/1.
Une véritable école des ponts
Démarré en janvier 2013, le chantier avançait sur les deux rives en même temps. « Notre projet constituait une superbe école des ponts puisque nous avons mis en œuvre trois grandes familles de techniques de construction », évoque Gilles Dumoulin. Tandis que les extrémités de chaque viaduc d’accès étaient réalisées par poussage des tabliers en béton (900 m au total), les parties côté canal étaient constituées de voussoirs en béton coulés en place par encorbellements successifs (1 km au total).
Le tablier du pont à haubans a quant à lui été construit en place, voussoir après vous-soir, grâce à quatre équipages (coffrages) mobiles, pesant chacun 240 t, et ce, de manière parfaitement symétrique. « La construction était symétrique par rapport à chacun des pylônes, pour éviter les déséquilibres de charges », précise Laurent Agostini, directeur technique du projet pour Vinci Construction Grands Projets.
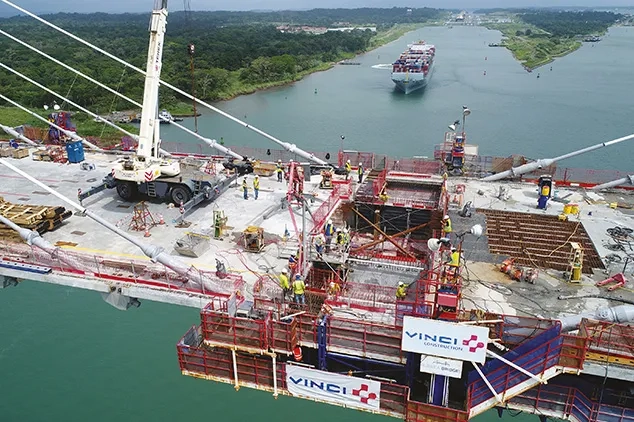
Le défi du positionnement des haubans
De la mise en œuvre des 432 pieux de grandes dimensions des fondations (jusqu’à 2,5 m de diamètre et 50 m de profondeur) à l’édification des pylônes géants en passant par la mise en tension progressive des haubans tenant les voussoirs, les défis techniques relevés par les équipes du chantier furent innombrables. L’un des plus complexes était celui du positionnement des ancrages des haubans dans les pylônes. « Malgré leur taille imposante, les pylônes possèdent en réalité une faible inertie dans le sens longitudinal du pont : très flexibles, ils se déforment à la manière d’un “bambou” à la moindre variation de température ou à chaque nouvel ajout de charge, un nouveau voussoir par exemple dont la charge est transmise sur le pylône par les haubans déjà installés. Or, avant le bétonnage de la levée du pylône, nous devions positionner les ancrages des haubans, dont chacun forme un angle différent avec le pylône, avec une tolérance angulaire très faible (0,3° vis-à-vis de la position absolue prévue dans le design). » Si le tube d’ancrage d’un hauban n’était pas correctement orienté, le risque existait en effet que le hauban frotte contre l’extrémité du tube et s’use prématurément. « Cette orientation doit être la bonne, sachant que le tube est placé pendant une phase de construction où ni le tablier, ni le pylône n’est dans sa position définitive », précise Laurent Agostini. Les équipes ont ainsi dû mettre en œuvre un contrôle géométrique précis doublé d’une méthode de construction très élaborée conçue pour permettre aux tubes d’ancrage des haubans de se trouver dans un alignement parfait en position finale.
Le moment de vérité eut lieu en août 2018 lors du clavage du tablier. « C’est lors de cette opération, où les deux moitiés de tablier se rejoignent, chacune formant un porte-à-faux de 265 m de long, que nous avons réellement su que le chantier serait une réussite », se rappelle Gilles Dumoulin. Après avoir ajusté la tension et la longueur des haubans, les deux fléaux se sont ainsi parfaitement positionnés l’un en face de l’autre, et le tablier, à l’issue d’un ultime bétonnage de la zone de clavage, formait une structure continue de 530 m de long.
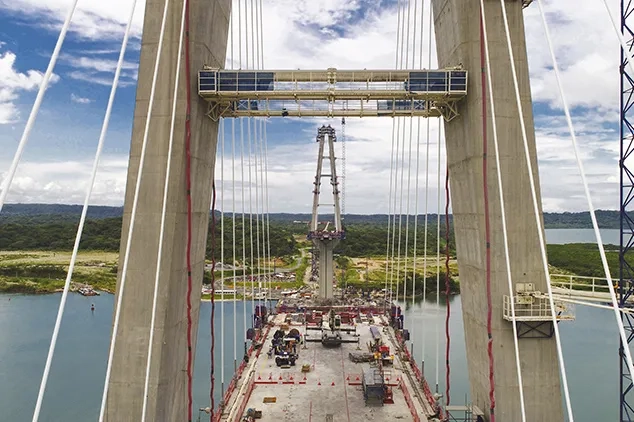
Une reconception au fil du chantier
En termes de planning, l’une des difficultés supplémentaires du chantier tenait dans le fait que les équipes de Vinci Construction Grands Projets ont dû reconcevoir le projet alors même que le chantier avait démarré. « Initialement, nous devions en assurer uniquement la construction, la conception ayant été menée en amont de l’appel d’offres », se souvient Gilles Dumoulin. Mais à travers plusieurs avenants successifs, il nous a été confié la responsabilité du design. « Nous avons dû recalculer l’intégralité de l’ouvrage en respectant néanmoins son architecture initiale. Sachant qu’un pont constitue un type d’ouvrage pour lequel les méthodes d’exécution sont intégrées à la conception, la coordination entre les équipes des bureaux d’ingénierie et celles du chantier n’a pas été une mince affaire », se rappelle Laurent Agostini.
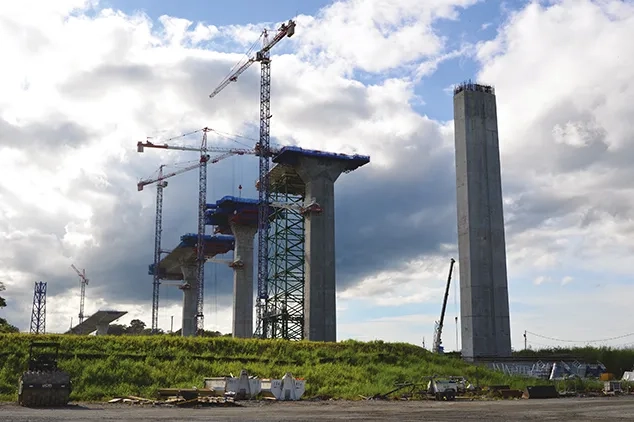
De la préfabrication au coulage en place
Ce changement de conception a notamment porté sur le mode de production des voussoirs. À l’origine, ceux-ci devaient tous être préfabriqués. Mais cela aurait néces-sité de multiplier les transports de voussoirs par barge d’une rive à l’autre du canal. Or, avec un trafic compris entre 40 et 50 bateaux de grande taille chaque jour, ce flux traversant aurait créé un vrai casse-tête logistique. « C’est pourquoi nous avons déci-dé de couler en place la quasi-totalité des éléments structurels des ouvrages », justifie Gilles Dumoulin. Deux centrales à béton ont ainsi été installées : une sur chaque rive. « Le béton était ensuite livré sur site par l’intermédiaire de camions toupie, puis mis en œuvre à la benne par grue pour les pylônes, ou par pompage pour les voussoirs du tablier. Nous avons effectué des pompages sur plus de 330 m de longueur », se rappelle Lionel Linger. « Dans ces cas, les bonnes fluidité et ouvrabilité du béton constituaient des paramètres déterminants. »
Au-delà des problématiques techniques, l’un des défis majeurs du chantier se trouvait du côté de la sécurité. « Nous avons dû former nos compagnons, tous recrutés loca-lement, afin qu’ils apprennent à travailler selon des standards beaucoup plus exi-geants que ceux qu’ils connaissaient », confie Gilles Dumoulin. Avec un résultat très satisfaisant à la clé : « Nous n’avons pas eu un seul accident grave sur toute la durée du chantier », se félicite le directeur de projet.
À l’issue d’un chantier de six ans qui aura compté jusqu’à 1 200 personnes se re-layant 24 h/24 et pratiquement 7 j/7, le pont de l’Atlantique a été mis en service le 2 août 2019.
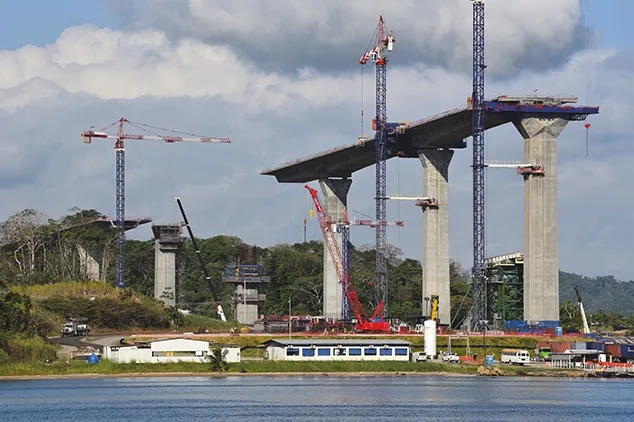
Avis d’expert
Lionel Linger, directeur du pôle matériau béton de Vinci Construction Grands Projets
« Nous devions bâtir un ouvrage d’art exceptionnel dans une ambiance agressive pour les bétons. »
Soumis à un climat tropical marin humide très agressif, les bétons du pont de l’Atlantique devaient répondre à des performances mécaniques très élevées ainsi qu’à une grande durabilité, l’ouvrage étant dimensionné pour une durée d’utilisation de cent ans. Lionel Linger, directeur du pôle matériau béton de Vinci Construction Grands Projets, explique comment les équipes d’experts sont parvenues à relever ce défi.
Les bétons constituant la structure des ouvrages d’art que vous avez construits devaient répondre à des performances très élevées. Avez-vous rencontré des difficultés dans leur formulation ?
Oui, de nombreuses ! L’une des grandes problématiques pour les ingénieurs du chantier a notamment résidé dans la capacité à formuler des bétons offrant des performances stables au cours du chantier. Au Panama, il est en effet très difficile de trouver des granulats et des ciments de qualités constantes. D’une fabrication à l’autre, les caractéristiques pouvaient différer grandement. Cette grande variabilité a obligé l’équipe projet à stocker de grandes quantités de matériaux sur site et à mettre en place des contrôles qualité drastiques en amont de la production du béton. Par ailleurs, nous
ne pouvions pas, par manque de disponibilité localement, utiliser des cendres volantes ou des laitiers moulus, des additions que nous utilisons d’habitude couramment dans la plupart de nos formulations pour renforcer leur durabilité et réduire leur empreinte carbone. Et ce, d’autant que le maître d’ouvrage imposait des spécifications hybrides drastiques, mêlant exigences performantielles et exigences prescriptives, ce qui limitait le choix du type de matériaux qui pouvaient être utilisés ainsi que les latitudes de formulation des bétons.
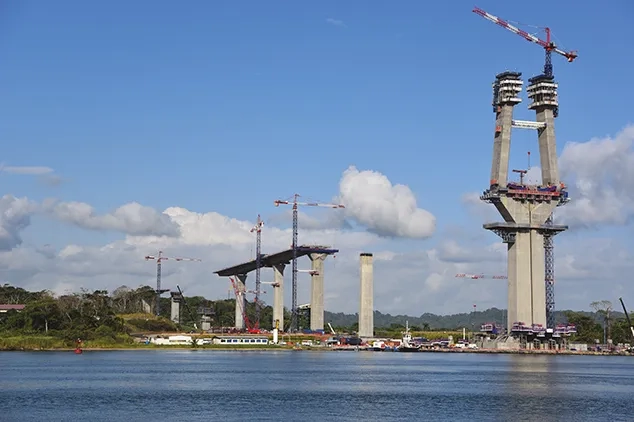
Comment se manifestait cette limitation ?
Lors de la préparation du coulage des pièces massives par exemple, sous des températures extérieures qui atteignaient souvent les 35 °C. En fonction des matériaux que nous avions à disposition, nous étions obligés de réaliser des modélisations thermo-numériques complexes pour être capables d’anticiper les conditions de mise en œuvre, sachant que la température maximale à cœur du béton était limitée à 75 °C et le différentiel de température entre le cœur et la peau à 25 °C. Lorsque ces critères seuils ne pouvaient pas être respectés avec les moyens classiques (refroidissement des granulats, eau froide, glace pilée) de production du béton, nous étions contraints de devoir refroidir le béton.
Quels moyens de refroidissement avez-vous utilisés ?
Le refroidissement était réalisé soit directement dans la toupie, en injectant de l’azote liquide qui permettait de réduire encore plus la température du béton frais au pied du coffrage, soit à l’intérieur même des éléments structurels, en faisant circuler de l’eau dans des tubes noyés dans la masse lors du coulage pendant plusieurs jours après le coulage (technique dite du post-cooling).
À combien de types de bétons avez-vous eu recours pour la construction de l’ensemble des ouvrages ?
En tout, trois familles de formulations ont été utilisées sur le chantier : pour les pieux de fondation des piles et des pylônes, la formule était très fluide avec un liant intégrant des pouzzolanes naturelles et de la fumée de silice. Pour les éléments de structures massives, le béton était formulé avec ces mêmes constituants proportionnés pour limiter la chaleur d’exothermie, mais pas suffisamment pour éviter de devoir les refroidir. Enfin, pour les voussoirs courants, qui nécessitaient une forte résistance au jeune âge pour pouvoir augmenter la cadence des cycles de production, était ajoutée une plus forte proportion de ciment à base de clinker Type II selon la classification des normes américaines (équivalent à CEM I PM selon la terminologie française).
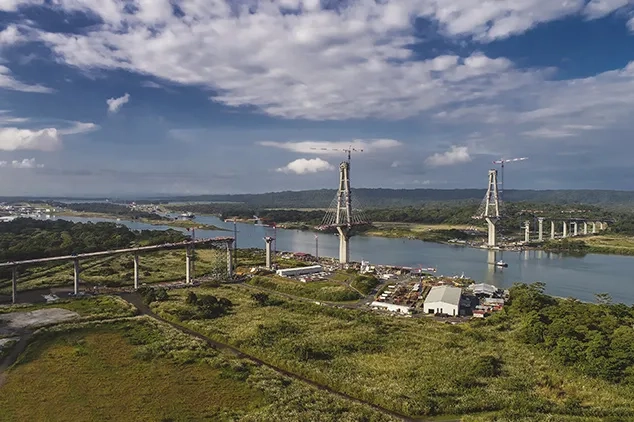
Reportage photos : photothèque VINCI et filiales ; F. Vigouroux
Principaux intervenants
- Maîtrise d’ouvrage : Autorité du canal de Panama
- Conception : China Communication Construction Company (CCCC) et Louis Berger Group
- Entreprise de construction : Vinci Construction Grands Projets
COMMENTAIRES
LAISSER UN COMMENTAIRE