Traitement des sols pour les travaux de terrassement de l’A79, entre Toulon-sur-Allier et Digoin
Important tronçon du vaste chantier d’aménagement de la route Centre-Europe-Atlantique (RCEA) et l’un des plus grands chantiers de terrassement réalisés en France en 2021, la liaison entre Montmarault (Allier) et Digoin (Saône-et-Loire) fait massivement appel à la technique de traitement des sols en place au liant hydraulique routier (LHR) pour le renforcement de l’arase et pour la confection de la couche de forme. Confié à l’entreprise Eiffage, ce projet a requis des solutions hors normes pour s’adapter à la nature des sols et aux cadences du chantier. Pour la partie est, de Toulon-sur-Allier à Digoin, les travaux ont nécessité 35 000 tonnes de Ligex M4, un LHR confectionné sur mesure par Ciments-Calcia.
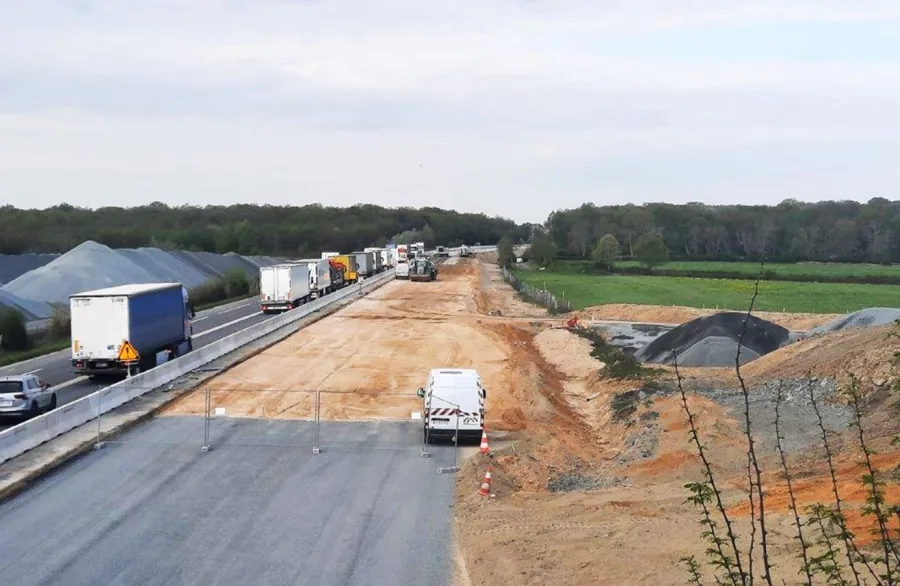
Situation
Le tronçon de la future A79 entre Toulon-sur-Allier (03) et Digoin (71) s’inscrit dans le plus large cadre de l’aménagement de la route Centre-Europe-Atlantique (RCEA). Une fois achevée, la RCEA reliera Bordeaux et la façade atlantique à l’Europe centrale et septentrionale, en s’intégrant dans un vaste réseau continental de voies express et d’autoroutes. Il s’agit de construire 1 850 km de voies en France, dont 400 km d’autoroutes et 800 km de routes express qui seront transformées postérieurement en autoroutes.
Le tracé de la RCEA est situé majoritairement en France. Il comporte plusieurs branches : deux à l’est et deux à l’ouest ainsi que d’autres, d’importance moindre. Elles se rejoignent toutes en une section centrale, de Guéret à Paray-le-Monial.
La RCEA présente l’avantage de rester au-dessous des 500 mètres d’altitude, de réduire le trajet Mulhouse-Bordeaux (de 970 à 830 km) et d’être gratuite. L’immense succès de l’itinéraire a induit un trafic beaucoup plus dense que les estimations de départ et un flux très important de poids lourds sur des routes construites, à l’origine, principalement à 1×2 voies. La mise à 2×2 voies, rendue indispensable par un taux d’accidents graves ou mortels beaucoup plus élevé que sur le reste du réseau français, est commencée dès les années 1990, mais elle bute en Saône-et-Loire et dans l’Allier sur un manque de financements publics.
État des lieux
Le tronçon de la future autoroute A79, objet de ce reportage, reliera Toulon-sur-Allier (03) à Digoin (71), en lieu et place de l’actuelle route nationale RN79. Il s’inscrit dans le cadre de l’aménagement de l’A79, qui reliera Montmarault (03) à Digoin (71) et qui se situe sur le tronçon central de la RCEA concédé par l’état à Aliae (filiale d’Eiffage).
La RN79 est une route particulièrement accidentogène à l’origine de fortes perturbations de trafic. C’est pourquoi le projet de mise à 2×2 voies aux normes autoroutières a été déclaré d’utilité publique par décret ministériel en date du 22 avril 2017.
Cette mise à 2×2 voies aux normes autoroutières a fait l’objet d’un contrat de concession avec la société Aliae, filiale à 100 % du groupe Eiffage, pour une durée de 48 ans à partir de la date de signature du contrat. À la suite de quoi, l’ouvrage sera transféré à l’État.
« En tant que maître d’ouvrage en charge de financer, concevoir, construire puis exploiter, entretenir et assurer la maintenance jusqu’au terme de la concession, Aliae a confié au groupement CLEA la conception et la construction de l’A79. Ce groupement, dont la mission s’achèvera à la mise en service de l’A79, rassemble toutes les compétences indispensables au bon déroulement des opérations techniques », explique Christophe Sandre, directeur du projet du groupement concepteur-constructeur CLEA.
Depuis la commune de Sazeret, à l’ouest, jusqu’à celle de Digoin, à l’est, 88 km de la RN79 passeront progressivement de 2×1 à 2×2 voies. Tous les ouvrages feront l’objet de mise aux normes de sécurité. « Ce chantier de grande envergure mobilise au plus fort de son activité un effectif qui atteint en pointe plus de 1 500 personnes et qui met en avant l’expertise multimétier du groupe Eiffage. Ce chantier a été découpé en quatre sections désignées par TOARC A, TOARC B, TOARC C et TOARC D », ajoute Christophe Sandre.
Néanmoins, l’impact environnemental d’un tel ouvrage n’est pas neutre, en particulier parce que le projet traverse une réserve naturelle (celle du val d’Allier) et parce qu’il est susceptible de créer un nouvel obstacle pour les déplacements de la faune locale.
« Pour réduire cet impact, nous avons dû intégrer à ce projet de nombreuses compensations environnementales et, notamment, la réalisation d’un passage pour la grande faune et de plusieurs ouvrages réservés au passage de la faune ainsi qu’une centaine d’ouvrages plus petits destinés à la petite faune afin de maintenir les continuités écologiques », ajoute Thibaut Meskel, responsable de l’Environnement chez Aliae.
L’autoroute A79 sera porteuse d’une grande innovation : le péage en flux libre, dispositif qui permet la suppression des barrières physiques de pleine voie au profit de portiques équipés de caméras capables de lire les plaques d’immatriculation et les badges de télépéage. « Ces portiques font partie d’un système intelligent qui permet de relier un véhicule ou un badge à un compte bancaire, de sorte à automatiser les transactions et à éviter l’arrêt aux gares de péage. Ils présentent aussi l’avantage de réduire considérablement l’artificialisation des sols », ajoute Thibaut Meskel.
Déjà en place dans certains pays européens, l’A79 sera la première autoroute de France à bénéficier de cette technologie de péage en flux libre, contribuant à la fluidification de la circulation avec un petit tronçon de l’autoroute A4.
Bon à savoir
Caractéristiques générales de l'A79 entre Sazeret et Digoin
- 88 km de longueur totale
- 48 ans de concession
- 65 km d’élargissement
- 23 km de route à 2x2 voies à requalifier
- Trafic estimé à la mise en service : 5 000 à 8 500 véhicules par jour et par sens, selon les tronçons
- 3,5 millions de mètres cubes de déblais
- 1 million de tonnes d’enrobés (GB classique, GB5® et BB5®)
- 12 échangeurs
- 4 aires de repos et 2 haltes simples
- 1 aire de service à Toulon-sur-Allier
- 148 ouvrages d’art, dont 45 ouvrages d’art courants neufs, 12 ouvrages non courants et 91 ouvrages existants à requalifier
- 79 bassins multifonctions
- 40 ouvrages pour la transparence écologique à élargir
- 52 cours d’eau franchis avec suivi écologique
- 21 communes traversées
Mise au standard autoroutier de la RN79 entre Toulon-sur-Allier et Digoin
Le projet
La RN79 est un axe majeur, tant localement qu’à l’échelle européenne. Elle draine ainsi un trafic compris entre 10 000 et 15 000 véhicules par jour dont 30 à 40 % de poids lourds selon les sections dans les départements de l’Allier et de Saône-et-Loire. La mise au standard autoroutier entre Toulon-sur-Allier et Digoin correspond aux TOARCS C et D (52 km sur les 88 km au total).
Les objectifs
Les objectifs sont de sécuriser et de fluidifier la circulation, la RN79 étant une voie dangereuse et encombrée.
Les contraintes
Elles sont de deux types :
- Les contraintes environnementales afin de respecter la nature et les paysages, de maintenir les corridors écologiques, de réduire l’impact sur l’environnement pendant les travaux et durant l’exploitation de l’autoroute.
- Les contraintes d’exécution dues au phasage des travaux, à la gestion du flux du trafic et des déviations, à la gestion de l’eau, du matériel et des déblais.
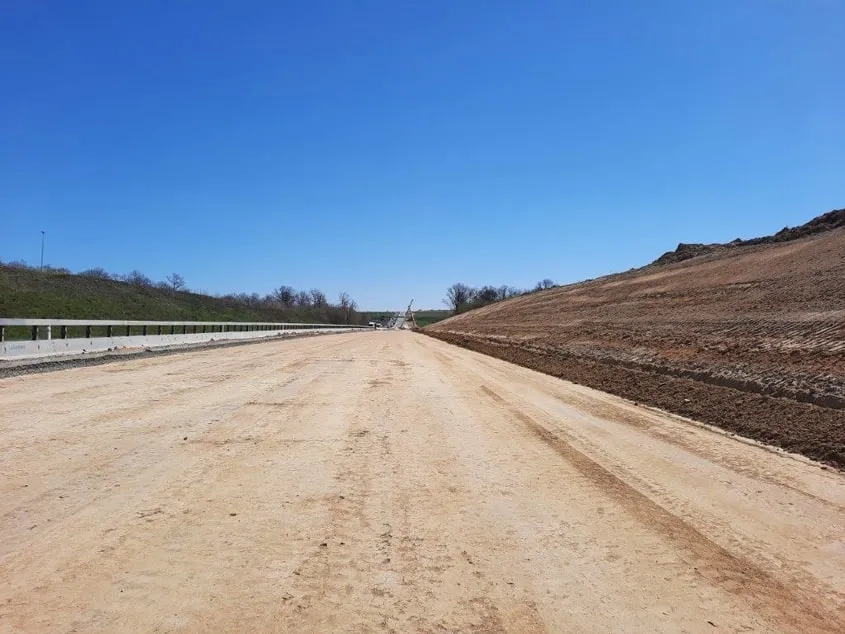
Études
Le contexte géotechnique
Le tracé du tronçon de l’A79 entre Toulon-sur-Allier et Digoin traverse principalement la formation géologique connue sous l’appellation « sables et argiles du Bourbonnais », qui est une formation hétérogène de sables plus ou moins argileux, avec présence de lentilles argileuses.
Les reconnaissances géotechniques
Pour les besoins des études de terrassement (mouvement des terres et études de traitement des sols), une campagne de reconnaissance géotechnique globale des ouvrages d’art et d’assainissement a été menée en deux phases : une G2 pro poussée, puis un contrôle en G3. La première, pour la phase de projet, a été réalisée au quatrième trimestre de l’année 2019 ; puis la seconde de contrôle, pour la phase d’exécution, au printemps 2020.
Lors de ces reconnaissances, 1 950 sondages géotechniques de tous types ont été réalisés : 850 sondages à la pelle ; 150 sondages avec essais pressiométriques tous les mètres ; 320 sondages carottés ou à la tarière ; 590 essais au pénétromètre type CPT, 40 piézomètres, etc.
Ces sondages ont des profondeurs comprises entre 1,5 et 17 m. Les différents matériaux ont été identifiés et classés conformément au Guide technique des terrassements routiers (GTR) et à la norme NF P 11 300 « Classification des sols ».
Les études de traitement
La présence des sables et argiles du Bourbonnais sur l’ensemble du tracé Toulon-Digoin a permis d’identifier rapidement les gisements potentiels en matériaux pour la partie supérieure des terrassements (PST) et la couche de forme (CDF). Grâce à leur facilité d’utilisation (taux de réemploi proche de 100 % lors des mouvements de terres), une stratégie avait été imaginée dès les études préalables, qui consistait à optimiser les mouvements des terres en maximisant le réemploi des matériaux du site et en les traitant soit à la chaux, soit au LHR pour les couches nobles de la future plate-forme autoroutière.
Compte tenu de l’hétérogénéité de certains gisements de matériaux, des mélanges associés pouvant varier en matériaux de B4 à A1, il a été décidé de mener un grand nombre d’études de traitement sur les différentes grandes familles de ces gisements pour :
- Vérifier l’aptitude du sol au traitement (norme NF P 94 100) ;
- Déterminer les performances mécaniques obtenues par un traitement à la chaux ;
- Déterminer les performances mécaniques obtenues par un traitement au LHR ;
- Vérifier la tenue au gel des sols traités.
L’objectif était de trouver un liant adapté à chaque type de sol afin de garantir les performances mécaniques visées (résistance mécanique et tenue au gel), tout en prenant en compte les contraintes spécifiques de mise en œuvre du chantier.
Le choix s’est finalement porté sur un LHR dont le délai de maniabilité était cohérent avec les exigences du traitement en place.
En outre, pour la couche de forme, une étude géotechnique de niveau 2 a été menée pour obtenir :
- Une plate-forme support de classe PF3 ;
- Un matériau traité de classe mécanique 5.
En termes de performances mécaniques et de comportement au gel, les objectifs recherchés étaient les suivants :
- Pour la PST inférieure : matériau traité à la chaux vive présentant une pente de gonflement au gel p < 0,25 mm / (°C.h) 1/2, peu gélif, classé SGp selon la norme NF P98-086.
- Pour la PST supérieure : matériau traité systématiquement au LHR et présentant une résistance Rtb > 0,25 MPa, non gélif, classé SGn selon la norme NF P98-086.
- Pour la CDF : matériau traité au LHR, présentant une résistance Rtb > 0,25 MPa, non gélif, classé SGn selon la norme NF P98-086 et de classe mécanique 5 au sens du GTS.
L’objectif était de trouver un liant adapté à chaque type de sol afin de garantir les performances mécaniques visées, tout en prenant en compte les contraintes spécifiques de mise en œuvre du chantier. Le choix s’est finalement porté sur un LHR dont le délai de maniabilité était cohérent avec les exigences du traitement en place.
La solution retenue pour la plate-forme support de chaussée
Les études ont permis de caractériser le matériau traité, de définir les dosages permettant d’atteindre les performances visées et d’établir un dimensionnement de la plate-forme support de chaussée.
Le dimensionnement optimisé des structures de chaussée a été réalisé en prenant comme objectif une classe de plate-forme autoroutière de portance PF3.
Compte tenu des conditions climatiques particulières qui règnent dans les départements de l’Allier et de Saône-et-Loire (indice de gel élevé 200 °C/J) et des épaisseurs optimisées des structures bitumineuses, le dimensionnement de la plate-forme support de chaussée repose sur deux variantes :
- soit une couche de forme granulaire, non gélive, de 50 cm ;
- soit une couche de forme traitée au liant hydraulique routier, non gélive, de 35 cm, avec une PST peu gélive, traitée au liant routier.
Pour optimiser la réutilisation des matériaux du site, le choix a été fait de réaliser les couches supports en matériaux traités au LHR, à savoir :
- PST inférieure : matériau traité à la chaux (dosage : 1,5 %) et sur une épaisseur de 35 cm. À réaliser uniquement dans les configurations d’arase nécessitant une amélioration de celle-ci, principalement dans les zones de déblais ou de remblais rasants.
- Objectifs :
- Matériau peu gélif avec pente de gonflement au gel ≤ 0,25 (soit Qg = 4) ;
- Densification : q3.
- Critères de réception :
- Compacité conforme à la densification q3 ;
- Portance EV2 ≥ 30 MPa.
- Objectifs :
- PST supérieure : matériau traité au LHR (dosage : 3 %) et sur une épaisseur de 35 cm.
- Objectifs :
- Matériau peu gélif (Rtb ≥ 0,25 MPa) ;
- Densification : q3.
- Objectifs :
- Couche de forme traitée au LHR : matériau traité au LHR (dosage : 5 %) et sur une épaisseur de 35 cm.
- Objectifs :
- Matériau non gélif (Rtb ≥ 0,25 MPa) ;
- Densification : q3 ;
- Matériau de classe mécanique 5.
- Objectifs :
Le choix du liant
Le liant fourni a été formulé spécifiquement pour le projet de l’A79, en lien avec les équipes techniques de CLEA. Ce liant devait pouvoir répondre en termes de composition, de performances mécaniques et de délai de maniabilité. « Après différentes propositions et divers échanges entre nos laboratoires, le Ligex M4 a été validé », explique Bruno Classen, directeur de l’agence Routes chez Ciments-Calcia.
Le liant fourni a été formulé spécifiquement pour le projet de l’A79, en lien avec les équipes techniques de CLEA. Ce liant devait pouvoir répondre en termes de composition, de performances mécaniques et de délai de maniabilité.
Choix de la structure de la chaussée
Compte tenu des performances escomptées de la plate-forme support de chaussée, la structure de la chaussée est la suivante :
- Enduit bicouche clouté, qui assure à la fois la protection de la couche de forme traitée et le collage à l’interface entre la couche de forme et la structure de chaussée.
- Couche de fondation en grave-bitume GB4 MAX, de granulométrie 0/14, d’épaisseur 9 cm, comportant 50 % de fraisats d’enrobés (recyclage de matériaux de la RCEA ou de chantiers situés à proximité).
- Couche de base en grave-bitume GB4 MAX, de granulométrie 0/14, d’épaisseur 9 cm et comportant 50 % de fraisats d’enrobés (récupérés sur la RCEA ou sur les chantiers des alentours).
- Couche de surface en béton bitumineux semi-grenu BBSG modifié de type BB5®, de granulométrie 0/10, d’épaisseur 5 cm et comportant 30 % de fraisats d’enrobés (récupérés sur la RCEA ou sur les chantiers des alentours).
- À noter : sur une zone de 4 km, au niveau de Toulon-sur-Allier, la couche de fondation et la couche de base ont été réalisées en grave-bitume de type GB5®.
Réalisation des travaux de terrassement
Phasage du chantier
Les travaux ont commencé, en août 2020, par les opérations de décapage de la terre végétale et de mouvement des sols pour modeler le terrain. « Les travaux des TOARCS C et D ont été lancés simultanément avec les quatre métiers (chaussées ; ouvrages d’art ; génie civil ; équipements). La durée des travaux a été fixée à deux ans. Pour tenir ces délais, l’entreprise a dû s’organiser efficacement et mettre en place une organisation spécifique, tant humaine que matérielle », précise Olivier Prinet, directeur des travaux chez Eiffage.
Plusieurs spécificités marquent ce tronçon :
- il fait 51,5 km et impose de longues distances à parcourir, en particulier par la route.
- il compte la réalisation de 8 viaducs.
- la traversée de la route nationale (RN7).
- la réalisation de 7 échangeurs sur le linéaire divise le chantier en plusieurs zones indépendantes qui contraignent le transport des matériaux traités.
- peu d’emprises foncières : complication de la gestion et du stockage des matériaux sur l’itinéraire.
Les travaux de terrassement se sont divisés en trois étapes : travaux de la PST inférieure (35cm) ; travaux de la PST supérieure (35cm) et travaux de la CDF (35cm).
Travaux de la PST inférieure traitée à la chaux
Dans un premier temps, l’arase a été décapée sur une épaisseur de 70 cm, puis mise en dépôt provisoire. Après la scarification, la chaux a été épandue à l’aide d’un épandeur asservi, à raison de 10 kg/m2. Le malaxage du sol et de la chaux a été réalisé sur une épaisseur finale de 35 cm, à l’aide d’un malaxeur tracté. Un réglage avec une niveleuse a ensuite été effectué, puis un compactage à l’aide d’un compacteur VM5 garantissant l’obtention de la compacité visée.
Travaux de la PST supérieure traitée au LHR
Cette opération consiste à acheminer les matériaux depuis le dépôt provisoire et à les répandre sur le site à l’aide d’une niveleuse, de façon à obtenir une épaisseur homogène avant traitement et suffisante pour garantir une épaisseur finale de 35 cm (après traitement, compactage et recoupe). L’utilisation de ces matériaux, issus des déblais, a permis de ne pas puiser dans les ressources naturelles locales. Le LHR Ligex M4 a été ensuite répandu à l’aide d’un épandeur asservi, à raison de 19 kg/m2. Le matériau et le liant ont été malaxés à l’aide d’un malaxeur tracté. Enfin, un préréglage avec une niveleuse asservie a été réalisé de façon à obtenir une épaisseur homogène. Cette phase est importante, car un bon réglage ne peut être garanti que s’il y a recoupe de la couche après traitement. Pour finir, le compactage a été réalisé par des compacteurs VM5.
L’utilisation de ces matériaux, issus des déblais, a permis de ne pas puiser dans les ressources naturelles locales.
Travaux de mise en œuvre de la CDF
Sur le chantier, une fois l’arase traitée, l’objectif de portance de la partie supérieure des terrassements (PST) est largement atteint (> 80 MPa). Ensuite, pour réaliser la couche de forme, les matériaux du dépôt provisoire ont été acheminés sur site (approvisionnement avec reprise sur stock à l’aide d’une pelle sur chenilles et de tombereaux articulés). Cette opération est suivie du régalage du matériau sur 40 cm, pour une épaisseur finale de 35 cm, afin de tenir compte du compactage et de la recoupe finale. Un préréglage avec une niveleuse asservie a ensuite été réalisé, de façon à obtenir une épaisseur homogène avant traitement. Cette phase est également très importante, car un bon réglage ne peut être garanti que s’il y a recoupe de la couche après traitement. Aucun apport n’est possible dans la phase de réglage final. « Une étape-clé a été la parfaite humidification du matériau. Pour obtenir une teneur en eau optimale, nous avons utilisé un malaxeur équipé d’un système d’injection d’eau dans la cloche, et ce préalablement aux opérations de traitement de la couche », explique Olivier PRINET d’Eiffage.
Cette opération a été suivie par le traitement proprement dit. Celui-ci a été réalisée en deux temps :
- Un épandage du LHR Ligex M4, à raison de 5 % (soit 30 kg/m2), à la surface du matériau a été réalisé en deux passes, à l’aide d’un épandeur autotracté.
- Un malaxage à l’aide de la machine type Wirtgen 240 ou similaire. Le matériau a été ensuite remis en forme.
Trois types de compacteurs ont été utilisés afin d’atteindre l’objectif q3 fixé : à bille lisse, à pieds dameurs (pour limiter le feuilletage), puis à pneus (pour donner un bel uni). « Une niveleuse assistée par GPS effectue le réglage par recoupe de la couche traitée, pour obtenir un résultat au centimètre près. On acquiert ainsi un très bon uni et un profil en long très régulier », ajoute Olivier Prinet.
Un enduit de cure bicouche clouté a été ensuite appliqué pour, d’une part, protéger la couche de forme et assurer la bonne prise hydraulique du mélange et pour, d’autre part, garantir l’obtention d’un bon collage à l’interface entre la couche de forme et la couche de fondation.
Contrôles
De nombreux contrôles ont été réalisés au cours du chantier afin de s’assurer des caractéristiques mécaniques visées.
Des contrôles de portance ont ainsi été réalisés pour la PST inférieure, traitée à la chaux vive, permettant de valider la classe d’arase obtenue.
Lors des travaux de la PST supérieure, traitée au LHR, la validation de la classe d’arase a été permise par des contrôles de portance couplés à des vérifications de densification au gammadensimètre.
Contraintes techniques du chantier
Approvisionnement en eau
Point crucial dans la mise en œuvre des matériaux traités : « L’humidification et l’arrosage doivent être constamment contrôlés afin de maintenir le bon état hydrique des matériaux. Plusieurs points d’approvisionnement ont donc été aménagés tout au long du tracé », explique Olivier Prinet.
Délai de maniabilité et logistique de livraison du Ligex M4
« Le Ligex M4 est un liant à base de clinker. Sa composition permet d’obtenir une cinétique rapide de montée en performance, tout en bénéficiant d’un délai de maniabilité adapté à une mise en œuvre des travaux de traitement des sols en place », précise Bruno Classen, chef de l’agence Routes de Ciments-Calcia.
Au total, ce sont 35 000 t qui ont été livrées sur la période concernée, relativement longue, compte tenu de l’importance du chantier, mais également des conditions restrictives dues à la pandémie de coronavirus. « Les livraisons ont débuté en Mai 2021 et se sont achevées à la mi-octobre 2021. Cependant, l’activité a connu son pic entre les mois de juillet et de septembre. Les cadences de livraison ont été très variables selon l’avancée des travaux. Certaines cadences journalières ont pu atteindre 300 tonnes », souligne Wilfrid Beck, technico-commercial chez Ciments-Calcia.
La logistique a été un élément-clé de la réussite de ce chantier pour Ciments-Calcia : la bonne communication entre les équipes de traitement d’Eiffage et de Ciments-Calcia a permis une fluidité des livraisons.
Bilan
« Ce chantier a été un défi du point de vue de l’organisation – en particulier, au regard de la longueur du tracé et des nombreux ouvrages qui le jalonnent – et du respect des enjeux environnementaux », précise Christophe Sandre.
En outre, il a été impacté par la crise du Covid-19 et par une météo pas toujours clémente… « Mais les équipes soudées et un bon enchaînement dans les diverses étapes du processus ont permis de relever ce défi ! » se félicite Christophe Sandre.
La couche de forme a été terminée à la mi-octobre 2021, pour une mise en service prévue à l’automne 2022.
Vidéos, Guides techniques, organisation de Journées techniques, découvrez les outils mis à votre disposition sur : www.infociments.fr/routes/
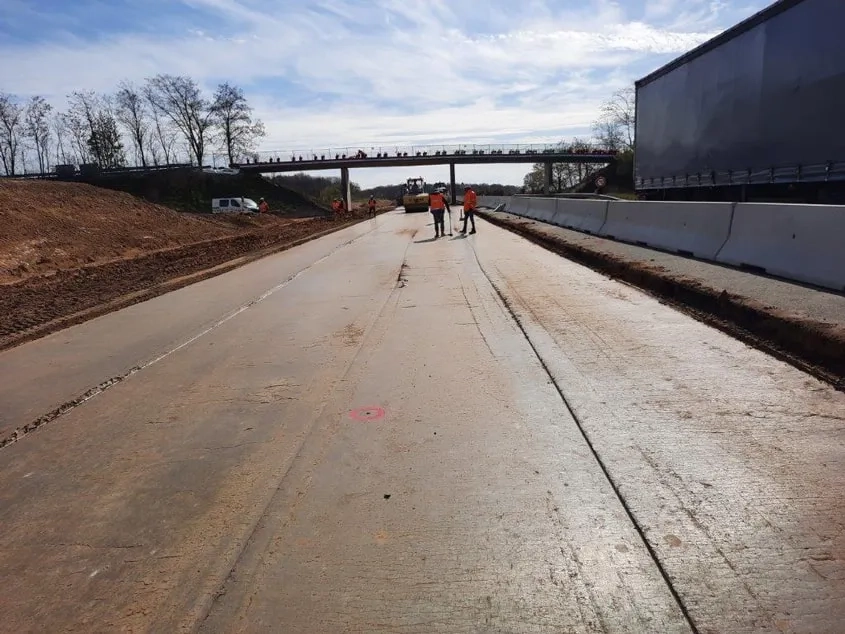
Localiser la réalisation
Principaux intervenants
- Concédant : État (DIT)
- Maîtrise d’ouvrage : Aliae
- Maîtrise d’œuvre : EGIS Villes et Transports
- GIE concepteur-constructeur : CLEA, Eiffage Génie civil
- Exploitant : APRR
- Fournisseur du LHR (Ligex M4) : Ciments-Calcia
En quelques chiffres
- Longueur : 52 km dont 6,9 km en requalification et 45,1 km en élargissement
- Déblais : 1 800 000 m3
- Remblais routiers et paysagers : 1 200 000 m3
- LHR Ligex M4 : 35 000 t
- PST traitée au LHR : 185 000 m3
- CDF traitée au LHR : 200 000 m3
COMMENTAIRES
LAISSER UN COMMENTAIRE