FastCarb : une solution pour développer la production bas carbone et l’économie circulaire
Avec le projet FastCarb et le travail de recherche et d’expérimentation entrepris sur la recarbonation des Granulats de Bétons Recyclés (GBR), l'industrie cimentière s'inscrit dans un cercle vertueux de recyclage et de production bas carbone. Entretien avec Laurent Izoret, directeur délégué Produits et Applications de l'ATILH.
Comment est née l’idée de travailler sur la recarbonatation du béton ?
Laurent Izoret – L’idée remonte à 2015 avec une réflexion commune avec l’IFSTTAR et le dépôt de deux projets ANR rejetés à l’époque. Puis il y eu le projet national Recybéton qui a pour objectif de développer le recyclage des granulats de bétons issus de la déconstruction. Grâce à Recybéton, nous savions qu’en France, nous pouvions compter sur environ 17 millions de tonnes de Granulats de Bétons Recyclés (GBR) par an. A ce jour, ces GBR sont réemployés en remblais routiers, en terrassement, dans la composition de bétons faibles performances adjuvantés ou encore traités par enfouissement.
Or, l’on sait que le béton a pour propriété de fixer lentement du CO2 grâce à la matrice cimentaire hydratée qui entoure les granulats naturels. C’est un processus chimique naturel et spontané connu depuis les travaux de Louis Vicat, nommé carbonatation.
Peut-on utiliser ce processus naturel pour «recarbonater » les GBR à partir du CO2 émis par les cheminées des cimenteries et, si oui, avec quelles applications ?
L.I : C’est tout l’objet du projet FastCarb. Par la recherche en laboratoire et l’expérimentation industrielle, il s’agit de valider ces concepts et proposer aux cimentiers une mise en œuvre certifiée avec des guides d’exploitation pour des modèles industriels.
Le processus industriel revient à fabriquer du calcaire par la rencontre entre les GBR et le CO2 industriel. Comme le produit « final;» sera du calcaire, nous allons évaluer les faisabilités de différentes voies possibles de valorisation de ces GBR «;recarbonatés » :
- les gravillons recyclables comme gravilons «calcaire» dans le béton
- les sables en tant qu’apport de calcaire au niveau du cru de cimenterie,
- ou comme constituant «calcair» principal des ciments autre que le clinker dans les ciments de type CEM II.
Avec Recybéton, nous avions démontré que le sable de GBR était déjà recyclable tel quel dans le cru de cimenterie, mais l’étape de recarbonatation nous donne des dimensions supplémentaires : celle du puits de carbone qui nous ouvre une voie additionnelle, celle du ciment au calcaire.
L’idée principale est donc de pouvoir traiter la majorité des émissions de CO2 des cimenteries ?
L.I : Exactement. Il s’agit de capter le CO2 émis par les cimenteries lors de la fabrication du clinker, en créant une dérivation à partir des cheminées. Sur le plan du « process », le CO2 émis lors de la décarbonatation est utilisé pour reformer du calcaire réutilisable.
Actuellement, on estime que 250 kg de CO2 sont émis pour 1 m3 de béton fabriqué. L’objectif ambitieux est de capter et de traiter par ce procédé la totalité du CO2 émis.
Et si nous arrivons, dans un premier temps, à garantir une captation et un traitement de 20% du CO2 émis, ce sera déjà une grande avancée.
Concrètement, quels procédés de carbonatation des granulats de béton recyclés sont expérimentés ?
L.I : Quatre solutions, dont 3 dynamiques et une statique sont à l’essai pour la mise en contact des granulats de bétons avec le CO2.
- La première consiste à utiliser des séchoirs à lit fluidisé. Les granulats de béton sous forme de sable sont déposés sur des plans en acier inclinés et perforés. Le CO2, pulsé à travers les perforations, imprègne les granulats pour les recarbonater.
- La seconde solution consiste à détourner l’utilisation d’un sécheur à tambour rotatif dans lequel les granulats de béton sont introduits à l’amont. Le CO2 des fumées y est injecté à l’aval et la rotation de l’ensemble, via des releveurs internes de matière assurera le mélange des gaz et des granulats et la captation du CO2 par ces derniers.
- Une troisième solution utilise le principe du filtre à gravier, bien connu en cimenterie dans les années 1970, dans lequel les granulats de béton sont déposés et recarbonatés par l’imprégnation du CO2 qui est diffusé de bas en haut.
- Enfin, un quatrième processus vise à stocker des GBR dans un conteneur équipé d’un système de diffusion de gaz. Ce procédé statique présente l’avantage de la simplicité de mise en œuvre.
Ce qui nous intéresse dans cette phase d’essai à l’échelle « pilote industriel » c’est la comparaison des performances des différents procédés et l’identification des leviers d’action pour améliorer les rendements et la qualité de carbonatation.
Quelles réutilisations sont envisagées pour ces granulats de béton recyclés et recarbonatés ?
L.I : Enrichit en CO2, ces granulats de béton reviennent à un état proche du calcaire.
- L’idée première est de pouvoir les utiliser dans la fabrication de béton en complément du ciment et de l’eau.
- La deuxième option est de les employer comme calcaire pour, ajoutés à l’argile, former le clinker.
- Troisième option : ils peuvent être injectés crus (sans cuisson) dans du ciment Portland, au même titre que du laitier ou des cendres, pour augmenter les performances du béton de construction.
Avec le projet FastCarb et la recarbonatation des GRB, on crée une boucle vertueuse de recyclage, avec à la clé, la production de produits à valeur ajoutée.
[INFOGRAPHIE] Le projet FastCarb
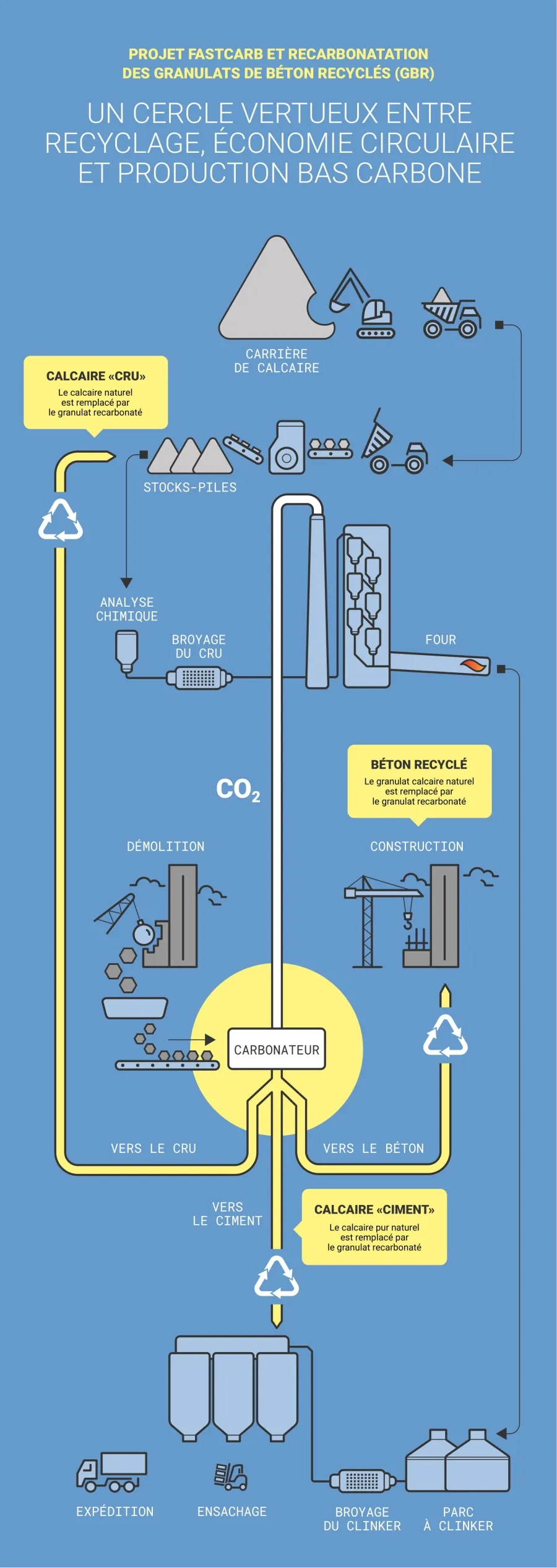
À quel stade en est le projet ?
L.I : Pour 2019, trois pilotes vont être lancés avec le concours d’industriels et le suivi d’universités et de laboratoires de recherche. Ils permettront de modéliser le processus, de le paramètrer et d’effectuer des tests en utilisation et en réutilisation, et de programmer des recherches pour vérifier les effets à long terme sur le produit et sur les installations.
Il s’agira également de fixer les coefficients de rendement et déterminer les bons dimensionnements des installations industrielles.
L’objectif reste, d’ici la fin du projet FastCarb en 2021, de mettre à disposition des industriels une mise en œuvre certifiée et des modèles d’exploitation.
Cela permettra une réduction de 20% des émissions de CO2 des cimenteries, et contribuera à atteindre l'objectif de réduction de 80% que s'est fixé l'Industrie Cimentière pour 2050.
Quelles sont les recherches qu’il reste à mener ?
L.I : Elles sont encore nombreuses.
- L’une porte sur une vitesse effective de carbonatation,
- l’autre sur la qualité des GBR recarbonatés, notamment la détermination de leurs caractéristiques : provenances, qualités (déblais contenant du gypse, de l’anhydrite, des roches fragiles, etc.).
- Enfin, il faudra vérifier la qualité finale des GBR recarbonatés : le calcaire « néoformé » sera-t-il mécaniquement très résistant ou très fragile ? Quel sera sont taux d’humidité final ? Cela change beaucoup de choses.
A titre d’exemple, avec des GBR recarbonatés plutôt fragiles et humides, il faudra favoriser une utilisation en « cru » pour entrer dans la fabrication du ciment, avec l’éventualité d’une décarbonatation à plus basse température et donc une économie sur la quantité d’énergie finale nécessaire à la clinkérisation.
A l’inverse, des GBR recarbonatés durs et secs seront à utiliser soit dans le ciment comme constituant principal autre que le clinker (ce qui évitera de puiser dans les ressources naturelles) soit dans dans la fabrication de béton, en complément du ciment et de l’eau.
Ce procédé est donc source de nombreuses économies : il préserve la ressource et permet le traitement du CO2 en évitant de l’émettre dans l’atmosphère.
L.I : Oui, tout à fait. C’est un cycle vertueux qui va permettre aux cimentiers d’économiser sur la ressource première et, ainsi, réduire drastiquement l’émission de CO2 grâce à un processus de traitement, directement à la sortie des cheminées.
L’objectif premier est de pouvoir récupérer 100 % des granulats de béton recyclés et de traiter 100% du CO2 sorti des cheminées.
Avec l’utilisation des GBR recabornatés, on préserve la ressource primaire et on économise également sur les coûts d’extraction. Le gisement de GBR existe, comme celui de CO2. A nous de les exploiter pleinement.
Surtout, nous avons voulu un projet frugal en matière d’innovation. Il n’y a pas d’innovation de rupture. Nous utilisons des procédés industriels déjà existants, fiabilisés, que l’on adapte pour un autre usage.
Il s’agit de permettre une mise en œuvre simple et rapide à partir de processus industriels maitrisés.
Le transport et la logistique semblent être également un des éléments importants ?
L.I : Oui, il ne faut pas les négliger car le transport a un coût économique mais aussi environnemental avec l’émission de CO2. Actuellement, nous avons un bon maillage de cimenteries sur le territoire français.
L’intérêt du projet FastCarb est que le procédé de traitement du CO2 pourra également être utilisé sur d’autres installations industrielles, par exemple pour des chaufferies ou des incinérateurs.
Les procédés de dérivation des fumées chargées en CO2, de recarbonatation ou de stockage de GBR recarbonatés, sont simples à mettre en œuvre, y compris sur de petites unités en milieu urbain.
Ainsi, on pourra constituer un réseau décentralisé et dense d’enrichissement et de valorisation sur l’ensemble du territoire.
En savoir plus
- sur le site du projet FastCarb
COMMENTAIRES
LAISSER UN COMMENTAIRE