Tours d’éoliennes de grande hauteur
L’entreprise Freyssinet a créé une gamme de tours d’éoliennes de grande hauteur en béton précontraint, constituées d’une superposition d’anneaux préfabriqués.
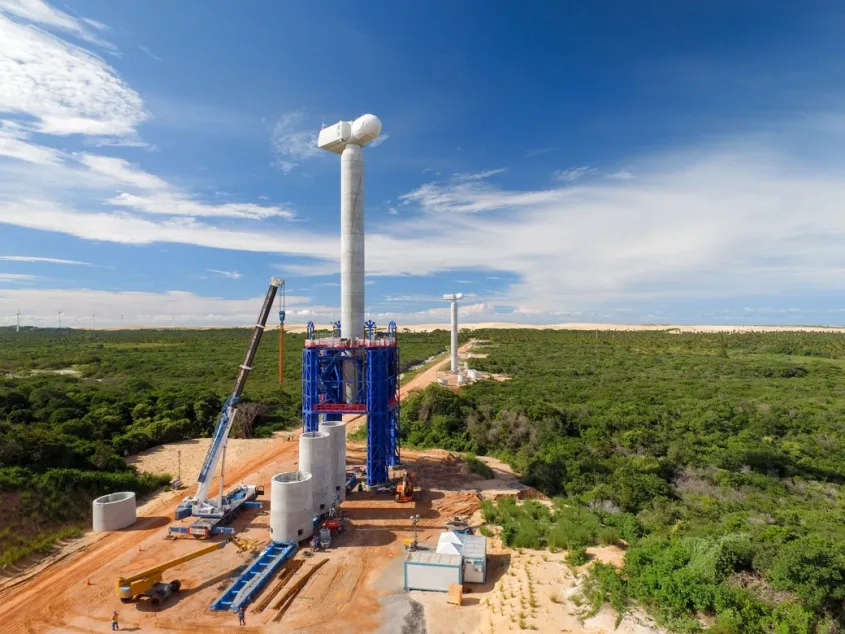
C’est une tendance de fond. Selon les projections 2018 de l’Agence internationale de l’énergie* (IAE), jusqu’à deux tiers de la production mondiale d’électricité pourrait provenir d’ici 2040 des énergies renouvelables, dont 20 à 25 % de l’énergie éolienne. Cette croissance programmée a déjà démarré. Elle s’accompagne d’une évolution typologique et technologique des éoliennes.
Pour capter toujours davantage d’énergie du vent, dont l’intensité augmente avec l’altitude, les éoliennes terrestres gagnent ainsi chaque année en puissance et en hauteur. Les plus imposantes culminent aujourd’hui à près de 160 m quand les nouveaux modèles de turbines annoncés affichent des puissances unitaires supérieures à 5 MW.Or en gagnant de la hauteur et de la puissance, les industriels repoussent les limites mécaniques des matériaux constitutifs des mâts des éoliennes.
Au-delà de 120 m de haut, les tours en acier sont particulièrement sensibles à la fatigue et, n’étant pas fabriquées sur site, demandent des moyens logistiques de transport lourds. Très logiquement, la capacité des grues indispensables à leur montage augmente elle aussi, tout comme leur coût et la taille de l’emprise au sol nécessaire à la circulation des engins de chantier et des grues en particulier. Par ailleurs, plus la hauteur de levage est importante, plus les contraintes sécuritaires sont sévères : les opérations de levage à la grue doivent être stoppées dès que les vents dépassent les 10 à 12 m/s, ce qui est fréquemment le cas sur les sites éoliens.
S’affranchir des contraintes de grande hauteur
C’est dans ce contexte, et dans l’objectif de faciliter la réalisation des éoliennes de grande hauteur, que l’entreprise Freyssinet (filiale de Vinci Construction) a développé une gamme de fûts d’éoliennes de grande hauteur en béton précontraint commercialisée sous la marque Freyssiwind dont le montage fait appel à un procédé compact utilisant un outil nommé Eolift.
« Ces deux innovations complémentaires font d’un côté appel à la préfabrication sur site d’éléments en béton formulés à partir de matériaux locaux, et de l’autre à un mode constructif permettant de travailler au niveau du sol », synthétise Jean-Daniel Lebon, directeur Énergies renouvelables du groupe Freyssinet. « Nous pouvons ainsi nous affranchir des contraintes logistiques et des conditions de vent liées à l’utilisation d’une grue, le procédé restant opérationnel et sécurisé jusqu’à une vitesse maximale de vent de 20 m/s, soit 95 % des vitesses de vent généralement observées. Il ne connaît par ailleurs potentiellement aucune limite de poids ni de hauteur. »
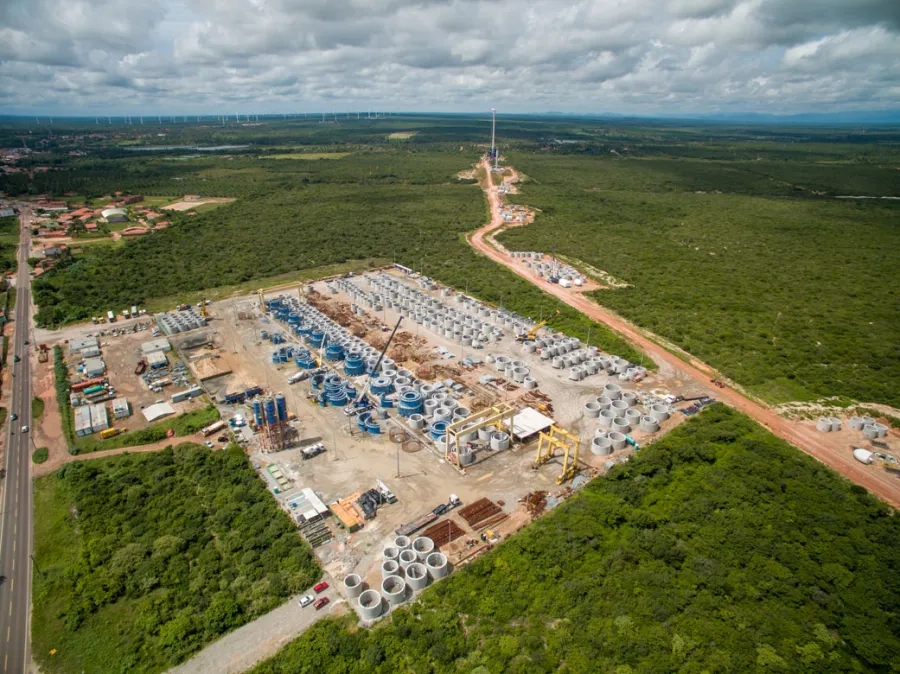
36 éoliennes pour un projet géant au Brésil
Ces éoliennes d’un nouveau genre ont pu bénéficier en 2016 d’un premier chantier d’envergure au nord-est du Brésil. 36 tours (119 m de hauteur pour une puissance unitaire de 2,7 MW) ont ainsi été installées avec le procédé Eolift pour le projet de ferme pilote de Trairi, dans l’État du Ceara.Chaque tour était constituée de la super-position de 32 segments d’anneaux en béton armé, préfabriqués dans un atelier forain situé au sein de la ferme d’éoliennes.
«Le principal enjeu de la préfabrication était de maintenir une qualité des anneaux constante», commente Jean-Daniel Lebon.
Une fois fabriqués selon la technique de la conjugaison, comme pour les voussoirs préfabriqués de ponts, les anneaux, d’un diamètre compris entre 4,5 m et 7,2 m (pour 3,9 m de hauteur et 25 à 40 cm d’épaisseur), étaient ensuite assemblés les uns aux autres par trois pour former des tronçons de 11,7 m de hauteur. Chaque tronçon était alors ripé sous l’outil Eolift, grâce auquel il était assemblé au tronçon supérieur initialement maintenu en position surélevée au centre de l’Eolift.
«Sur le projet brésilien, nous avons utilisé une grue mobile notamment pour décharger les voussoirs du camion et pour monter la turbine sur les 25 premiers mètres de la tour. Grâce aux retours d’expériences que nous avons accumulés sur ce projet, nous avons depuis modifié le procédé et le phasage pour que nous puissions totalement nous passer de grue lors de cette étape», commente Jean-Daniel Lebon. Désormais, seul le déchargement de la turbine sur la fondation nécessite une grue de faible capacité (voir encadré sur le phasage de montage, ci-dessus).
C’est l’outil Eolift qui se substitue à la grue. Pour cela, une petite potence pivotante a été intégrée à chaque demi-côté de l’Eolift. Elle permet notamment de décharger directement les voussoirs en béton des camions.
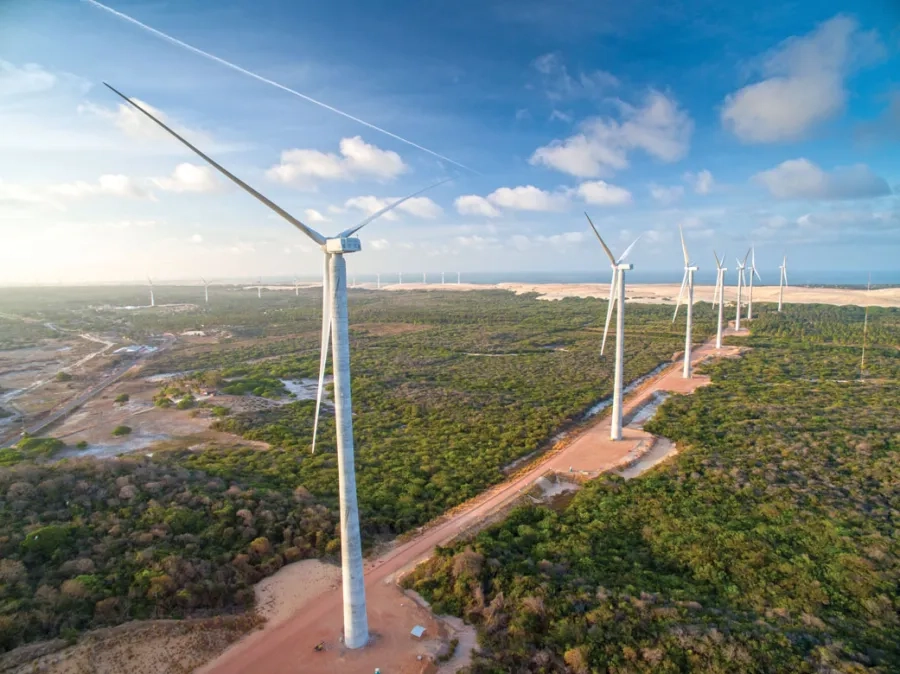
Une tour d’éolienne construite... de la tête aux pieds !
Le montage depuis le sol de la tour d’éolienne s’effectue de manière non intuitive, la tête étant hissée avant les pieds ! Tout commence en effet par la pose de la turbine de l’éolienne sur la fondation en béton armé préalablement construite.
L’outil de levage Eolift, constitué d’un châssis de hissage solidement ancré à la fondation de l’éolienne, est alors installé autour de celle-ci et vient la soulever à l’aide d’un système de levage hydraulique.
Il va alors monter les sections de la tour en ordre inversé par rapport au montage à la grue : les éléments inférieurs, préassemblés par segments de trois anneaux de part et d’autre de l’outil, sont glissés sous les éléments supérieurs déjà assemblés et levés, puis l’ensemble est hissé. L’opération est répétée jusqu’à la hauteur finale.
L’outil Eolift est alors démonté de manière quasi automatique. Les organes de connexion, les structures et les façades de l’Eolift sont repliés automatiquement avant que l’ensemble de l’outil soit transféré jusqu’à l’emplacement de montage suivant. Reste ensuite à installer les pales de l’éolienne.
Une structure renforcée par des câbles de précontrainte
Pendant les phases d’élévation de la tour, sa résistance provisoire est assurée par la connexion des éléments les uns aux autres par boulonnage au droit des joints. Mais une fois l’éolienne en service, «la structure est comme une grande quille soumise à des efforts importants, liés notamment au vent soufflant dans les pales. Le béton, même fortement armé, ne pourrait pas résister seul sur le long terme». C’est pourquoi la structure de la tour est renforcée par des câbles de précontrainte, installés une fois la tour entièrement assemblée et connectée à la fondation.
Il s’agit d’une précontrainte extérieure verticale constituée d’un ensemble de câbles de même longueur ancrés en pied dans la fondation de l’éolienne et en tête dans l’anneau supérieur, spécialement épaissi pour recevoir les ancrages.
Une fois tous les torons ancrés en partie haute, la mise en tension est réalisée toron par toron en partie basse, dans la fondation, à l’aide d’un vérin monotoron.
« Sur le projet brésilien, nous disposions de 16 câbles 13T15 par éolienne, mais nous avons depuis fait évoluer le design pour minimiser le nombre de câbles. » Les futurs projets comprendront ainsi 12 câbles 19T15 par éolienne.
Et l’innovation continue pour Freyssinet
Suite à la construction des 36 éoliennes de la ferme pilote de Trairi, achevée début 2017, de nombreux projets sont à l’étude partout dans le monde, « mais uniquement sur des parcs de grande ampleur, affichant de 100 à 300 MW de puissance cumulée minimum », précise Jean-Daniel Lebon.
En attendant, l’entreprise Freyssinet bouillonne toujours de nouvelles idées. Après la tour construite sans grue, elle vient de déposer un nouveau brevet pour une méthodologie de pose de pales sans grue.
Chiffres clés
Béton : 600 m3 pour une tour de 130 m de haut
Armatures : 110 à 120 kg par m3 de béton
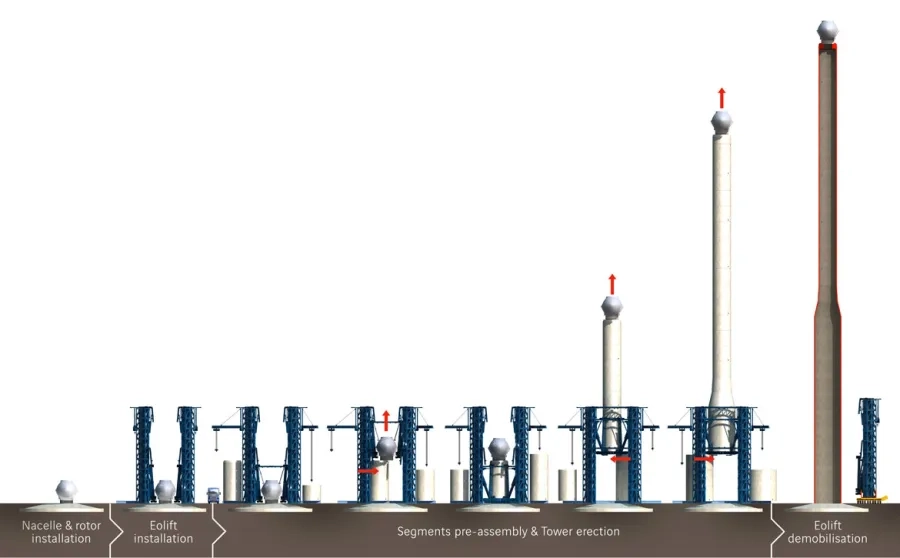
Une conception et un béton formulé pour éviter l’entrée en résonance de l’éolienne
Le béton des anneaux des tours est produit dans une usine de préfabrication foraine située au cœur de la ferme éolienne. Il est de classe de résistance C 60/75 et est armé avec une densité d’armatures comprise entre 110 à 120 kg/m3. Afin d’éviter des phénomènes de vibration, une fois la géométrie de la tour définie, le critère de dimensionnement du béton le plus important est son module d’élasticité.
« Nous devons absolument maintenir la fréquence propre de la tour en dehors des zones interdites définies par le fournisseur de turbines, pour ne pas entraîner une mise en résonance potentiellement très dommageable », justifie Jean-Daniel Lebon.
Pour garantir un module d’élasticité constant, les exigences de qualité, tant sur le processus de sélection des composants du béton (granulats, ciment...) que sur la chaîne de production, sont très élevées.
Pour le projet de Trairi, le mode de production des anneaux incluait une phase de vibration du béton, « mais nous utiliserons du béton autoplaçant (BAP) pour nos prochains projets », confie Jean-Daniel Lebon.
Principaux Intervenants
Texte : Olivier Baumann – Reportage photos : Laurent Chartier-Freyssinet
-
Courbevoie
-
Metz-Queuleu
-
COMMENTAIRES
LAISSER UN COMMENTAIRE