Un ponton flottant en béton armé pour accueillir les navires de combat
La base navale de Brest s’est récemment dotée d’un nouvel appontement pour accueillir les frégates multi-missions de la Marine nationale. L’ouvrage se distingue par son originalité : il s’agit d’un ponton flottant en béton armé aux dimensions XXL : 160 m de longueur, 17 m de largeur pour 9 m de hauteur. Entre planning serré, logistique contrôlée et hautes exigences de qualité, sa construction, dans une cale sèche de la base militaire, a imposé de relever de nombreux défis au groupement d’entreprises de génie civil. Récit.
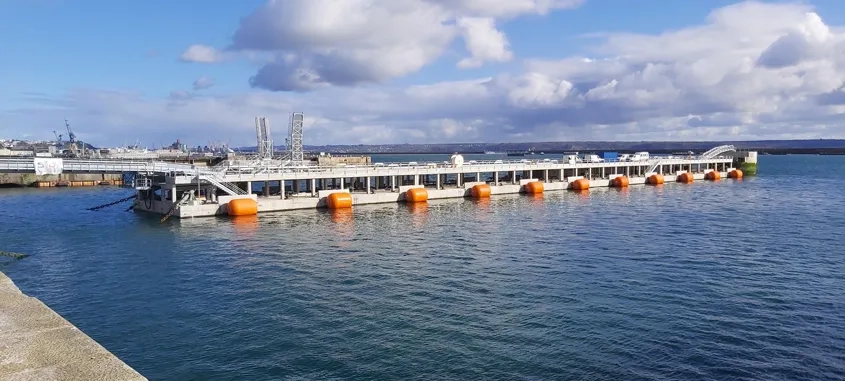
Navires militaires de combat, les frégates multi-missions (FREMM) se caractérisent par leur polyvalence : leurs capacités anti-sous-marines, anti-navires et anti-aériennes en font en effet de redoutables adversaires, capables d’atteindre des cibles en mer comme à terre. Si elles disposent d’une grande autonomie et d’une grande endurance, elles doivent néanmoins faire des escales régulières pour se ravitailler en carburant, en vivres et assurer le débarquement/embarquement des marins. Pour cela, les six FREMM françaises peuvent compter sur les appontements des bases navales de Toulon et de Brest. Suite à la mise en service d’un premier ponton d’accostage flottant en 2013, le port militaire de Brest s’est doté en avril 2021 d’une seconde ligne.
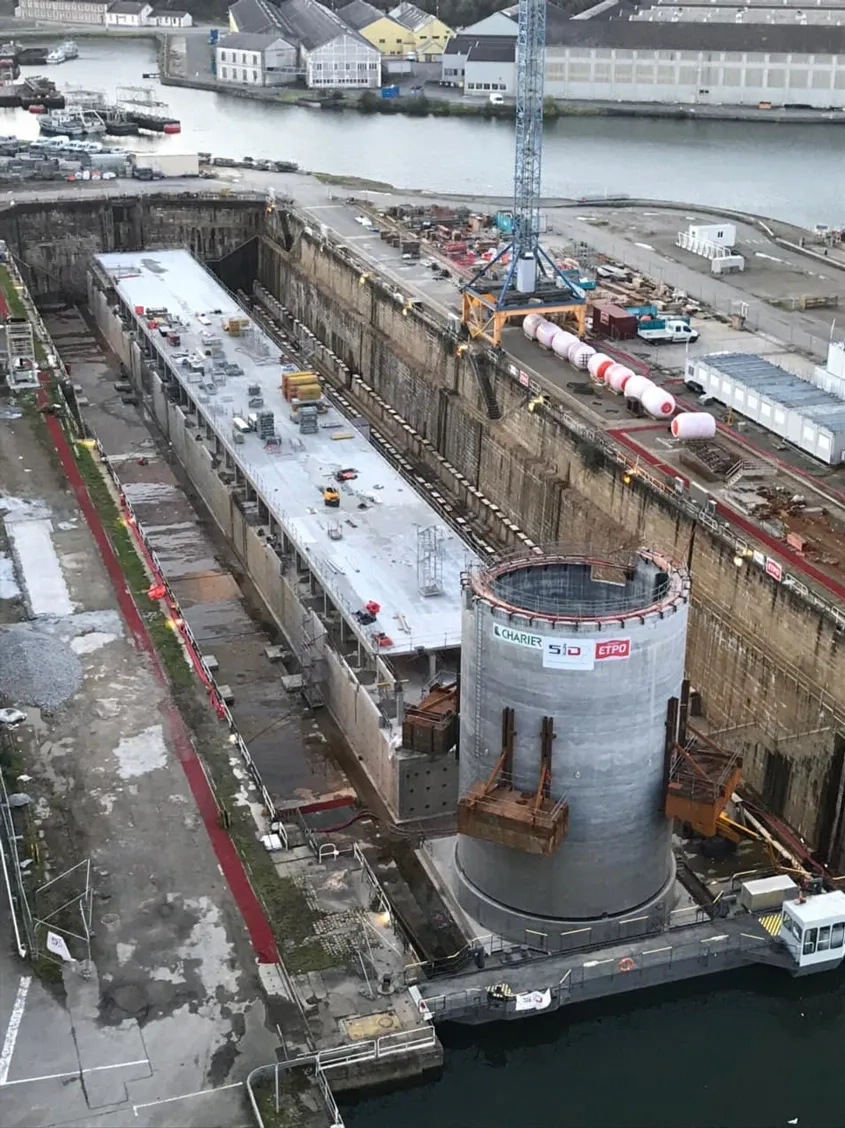
Un géant des mers en béton armé
Accessible par tout temps à ces imposants bâtiments de 142 m de long, le ponton en béton armé de 160 m de long, 17 m de large et 9 m de hauteur est lui aussi un géant des mers. Sa conception, similaire à celle du premier ponton, a été assurée en utilisant le BIM par une maîtrise d’œuvre pilotée par Artelia. L’ouvrage est constitué de deux ponts superposés et indépendants, offrant une ergonomie adaptée aux FREMM. Le pont supérieur est accessible en permanence aux véhicules et aux piétons via une passerelle qui le relie au quai. Le pont inférieur, accessible depuis le pont supérieur par un escalier, accueille les différents réseaux et les points d’amarrage.
Ces deux ponts – dont la structure en béton armé est constituée de dalles sur poutres et poteaux – reposent sur un caisson flottant monolithique, également en béton armé, dont 3,4 m sont immergés en permanence. Sa structure est constituée d’un radier et de voiles périphériques de forte épaisseur. Pour que le caisson puisse flotter malgré son poids important, un cloisonnement intérieur dessine douze alvéoles indépendantes présentant un volume total de 1 000 m3 et constituant autant de « poches » d’air à même de contribuer à la poussée d’Archimède.
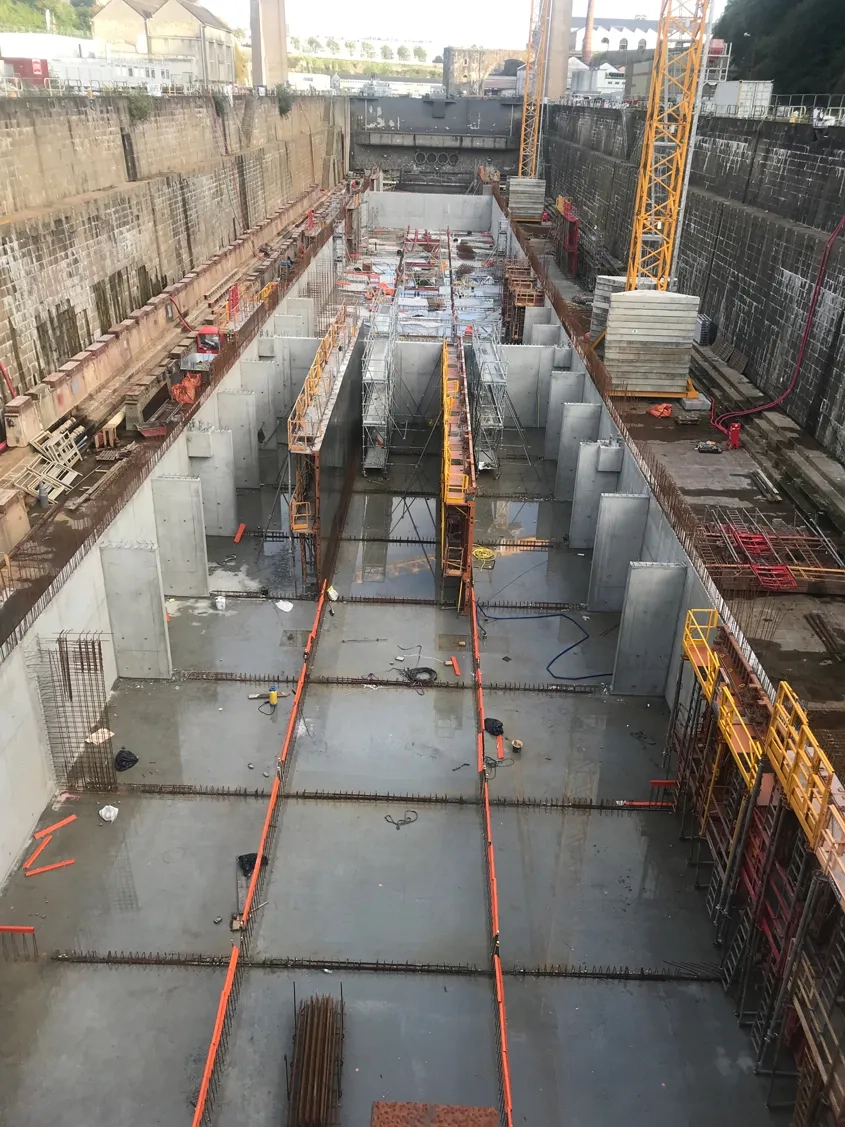
Des chaînes contre la mer déchaînée
Perpendiculaire au quai, le ponton est solidement amarré à chacune de ses extrémités à des points fixes, par l’intermédiaire de chaînes métalliques : côté quai, sur des massifs en béton armé fondés sur des micropieux ; côté mer, sur un musoir cylindrique en béton armé posé sur le fond marin. Sur le ponton, les quatre points d’ancrage de la chaîne sont constitués d’amortisseurs conçus pour reprendre les efforts d’accostage et les efforts d’amarrage. « Lorsque le ponton est chahuté par une mer agitée, les amortisseurs permettent de réduire les efforts d’amarrage. Néanmoins, cette réduction suppose qu’eux-mêmes puissent encaisser des charges importantes. C’est pourquoi les amortisseurs sont fixés sur des socles en béton très fortement armé – de l’ordre de 350 kg d’armature par mètre cube de béton, contre une moyenne de 200 kg/m3 pour le reste de l’ouvrage », précise Emmanuel Størksen, directeur général délégué d’ETPO, cotraitant du groupement de génie civil piloté par l’entreprise Charier.
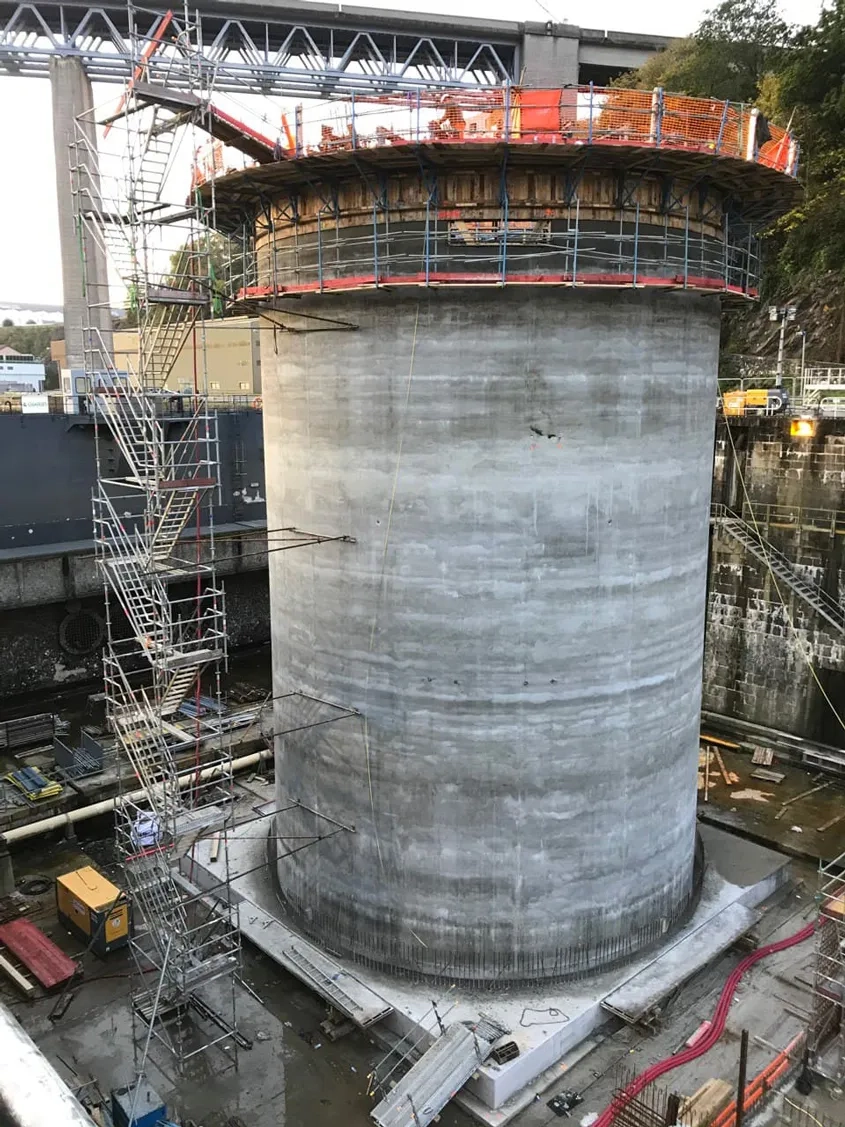
Planning serré et accès contrôlés
Côté chantier, les équipes du groupement ont pu profiter d’une cale sèche pour pouvoir ériger simultanément les structures du ponton et du musoir à l’abri des embruns. La mise à disposition de cette forme de radoub par le maître d’ouvrage était assujettie à une contrainte forte : celle des délais. « Nous ne pouvions pas déraper dans le planning de réalisation car la cale devait accueillir un chantier après le nôtre », poursuit Emmanuel Størksen. Une autre contrainte, liée à la localisation du chantier sur un site militaire, devait être prise en considération : « Avant de pouvoir accéder au site, toutes les entreprises, tous les fournisseurs devaient obtenir une autorisation, et certains collaborateurs faisaient l’objet d’enquêtes préalables. Pour ne pas risquer de bloquer le chantier pour un document manquant ou une inscription non faite, nous avons dû largement préparer et anticiper chacune des opérations en lien avec le maître d’ouvrage. »
La préparation du chantier a demandé également une grande implication de la part des bureaux d’études du groupement d’entreprises : bien que le ponton soit de conception quasi identique à celui qui avait été livré en 2013, les études d’exécution ont dû intégrer le redimensionnement de certains éléments du design – notamment la répartition des armatures dans le béton – pour tenir compte des évolutions réglementaires et des Eurocodes, le ponton ayant été justifié sur la base d’un règlement antérieur.
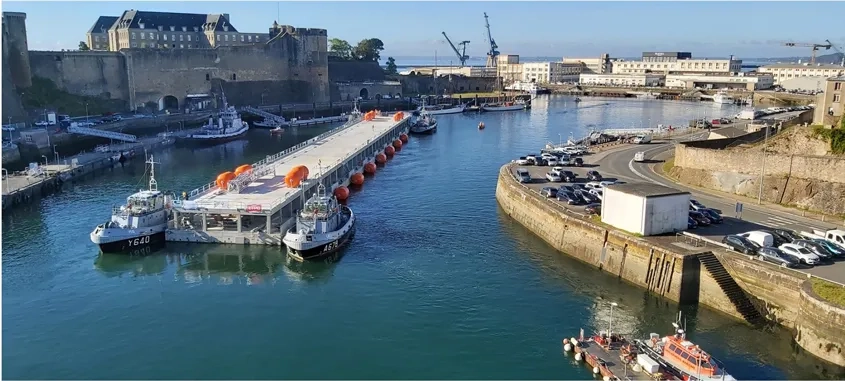
Un coulage continu sur six jours en coffrage glissant
La construction du ponton a débuté à l’automne 2019 par le coulage du radier, avant l’élévation des voiles longitudinaux et transversaux. « Les voiles longitudinaux périphériques sont plus épais (35 cm) que les voiles transversaux (30 cm), car ils sont soumis directement à la pression des coques des frégates », précise Emmanuel Størksen. Ses structures ont ensuite été solidarisées par une dalle de 25 cm d’épaisseur. Près de 150 poteaux ont alors été coulés avant d’être eux-mêmes recouverts par la dalle du pont supérieur.
La réalisation du musoir, cylindre de 14 m de diamètre et 23 m de haut, a été menée parallèlement à celle du ponton. Après le coulage du radier de 80 cm d’épaisseur, ses voiles courbes de 40 cm d’épaisseur en partie courante ont été coulés à l’aide d’un coffrage glissant sur six jours en continu, au rythme de 20 cm par heure. « Cette opération intensive, menée par 40 personnes mobilisées 24 h/24, a été minutieusement préparée en amont, notamment pour assurer le bon cadencement des camions-toupies, qui devaient livrer 4 m3/heure. »
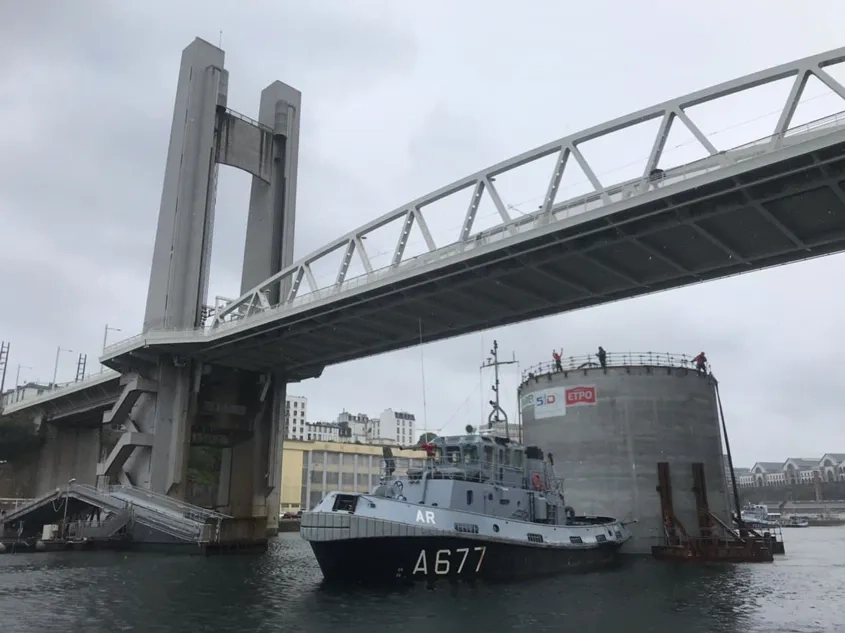
Une fois les ouvrages terminés dans la cale sèche, le ponton et le musoir ont été mis à l’eau avant d’être successivement remorqués vers leur implantation définitive.
Préalablement à l’échouage du musoir, les sédiments présents sur le fond marin ont été dragués. « Afin de limiter le volume dragué et son traitement, nos équipes et nos plongeurs ont confiné la zone jusqu’à la cote du terrain naturel au juste nécessaire pour asseoir le musoir », précise Emmanuel Størksen. La totalité des matériaux de dragage a ensuite été traitée à terre avant d’être réutilisée en remblai dans le musoir.
Une structure de 8 750 tonnes, et pas un kilo de plus !
Pour que les opérations d’avitaillement et de débarquement/embarquement puissent se dérouler sans encombre, le niveau de flottaison du ponton devait respecter scrupuleusement les prescriptions du cahier des charges, avec une partie émergée de 4,9 m de hauteur. Autrement dit, il fallait que la masse réelle de l’ouvrage soit identique à la masse calculée, et qu’elle soit répartie de manière uniforme. « Nous partions en permanence à la chasse aux kilos superflus ! », plaisante Emmanuel Størksen. L’épaisseur des voiles et des radiers était notamment scrutée de près. « Nous mettions en place des témoins d’épaisseur sur les parties d’ouvrage coulées et nous contrôlions systématiquement les volumes réellement mis en œuvre. »
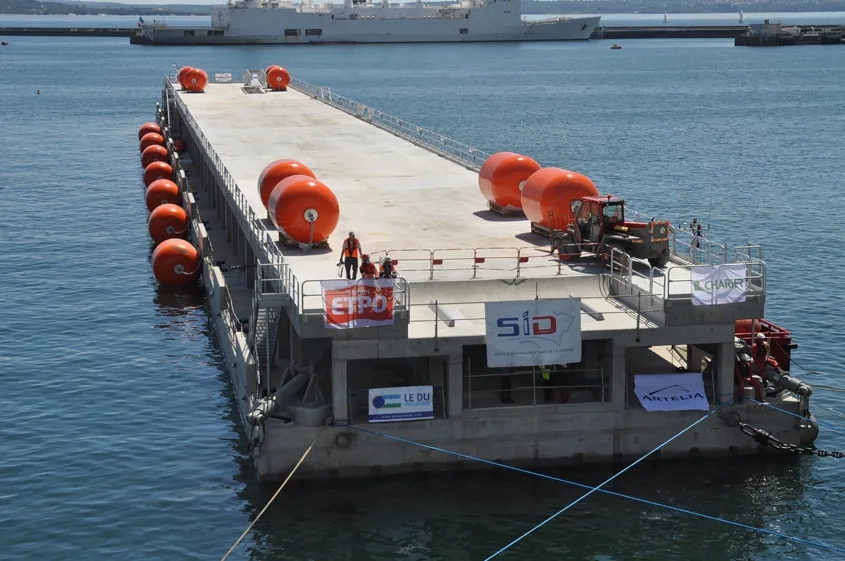
Formuler un béton étanche, fluide et résistant au jeune âge : un numéro d’équilibriste !
On l’imagine aisément : le béton constitutif d’un ouvrage comme le ponton flottant n’est pas un béton ordinaire ! Il devait d’abord être le plus étanche possible. « Pour cela, nous devions nous assurer que la formulation contienne suffisamment de fines, afin d’obtenir une "fermeture" optimale du matériau », explique Emmanuel Størksen. La bonne étanchéité de la structure passait aussi par une minimisation des zones de fragilité constituées par les reprises de bétonnage. « La rhéologie du béton devait être suffisamment fluide et homogène pour que les équipes aient le temps de le mettre en œuvre, et éviter les risques de reprise de bétonnage et de ségrégation », poursuit le directeur. Ensuite, le matériau devait répondre à une exigence a priori contradictoire : « le planning très serré du chantier nous obligeait à respecter des cycles de bétonnage très courts ». Le béton devait donc offrir une bonne résistance au jeune âge afin de pouvoir être décoffré rapidement.
« La centrale de Guipavas de notre fournisseur BCA a réussi à formuler un béton équilibré, conciliant résistance au jeune âge et bonne rhéologie », souligne Emmanuel Størksen, qui précise que le béton retenu dispose d’une classe de résistance C35/45, d’une classe d’exposition XS3 et d’une épaisseur d’enrobage des armatures de 5 cm.
Enfin, la masse réelle de l’ouvrage devait être strictement contrôlée afin de garantir le niveau de flottabilité calculé, la masse volumique du béton – 2,39 t/m3 – étant régulièrement vérifiée.
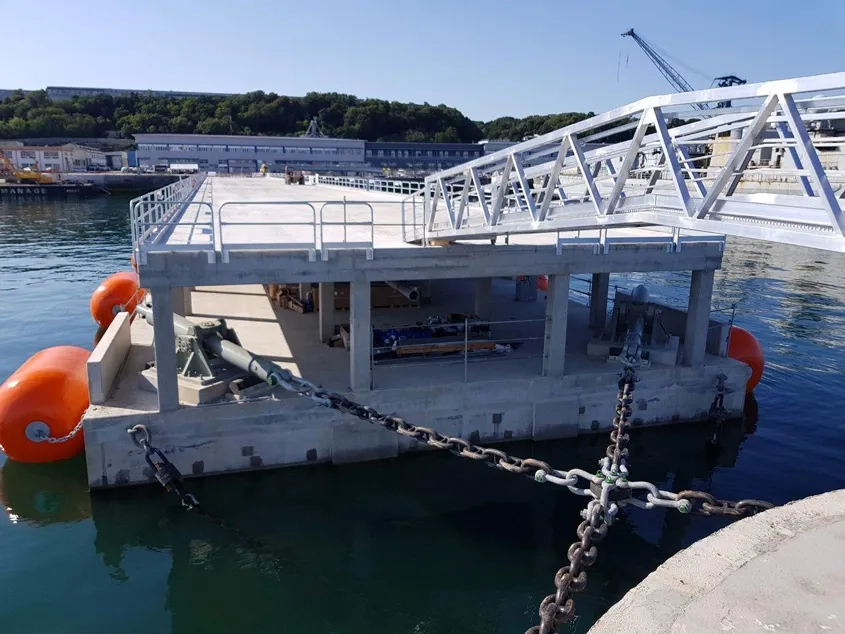
Localiser la réalisation
Fiche technique
Reportage photos : Groupe ETPO et Devisubox
- Maître d’ouvrage : ministère des Armées – Établissement du service d’infrastructure de la Défense (ESID) de Brest
- Maître d’œuvre : Artelia
- Entreprises de génie civil : groupement Charier SA/Charier GC/ETPO/Ducrocq/Geomine
- Fournisseur de béton : BCA (filiale de Tanguy Matériaux)
Chiffres clés
Ponton flottant
- 160 m de long x 17 m de large x 9 m de haut hors tout
- 3 600 m3 de béton utilisés pour la structure du ponton flottant, soit 8 750 tonnes
Musoir
- 14 m de diamètre x 23 m de hauteur
- 550 m3 de béton
Ancrages
- 4 chaînes principales capables de reprendre des efforts de 350 tonnes
COMMENTAIRES
LAISSER UN COMMENTAIRE