Une tour solaire géante au milieu du désert
Au beau milieu du désert de Néguev, en Israël, s’élève depuis début 2018 la plus haute tour solaire du monde. L’ouvrage monumental en béton culmine à 256 m de hauteur.
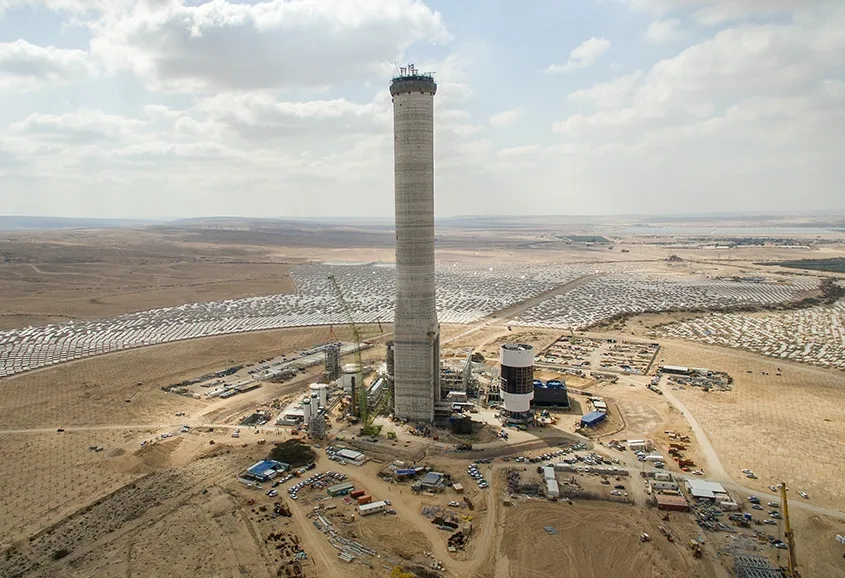
On la voit de loin. Une tour de 256 m de haut s’érige en plein désert de Néguev, en Israël. Il ne s’agit pas d’un mirage, mais de la plus haute tour solaire du monde. Elle constitue l’élément central d’une technologie rare, la centrale solaire à concentration, dont le principe est simple : des dizaines de milliers de miroirs mobiles (les héliostats) installés au sol font converger les rayons solaires qu’ils reflètent vers le sommet de la tour, constitué d’un four solaire de 50 m de haut.
L’eau qui circule à l’intérieur de ce dernier s’échauffe sous l’effet de ce rayonnement, pour atteindre des températures extrêmes, d’environ 600 °C. La vapeur est alors canalisée vers le pied de la tour, où elle est utilisée pour faire tourner une turbine qui produit de l’électricité, ensuite injectée dans le réseau. D’une puissance installée de 310 MW, cette centrale solaire thermique à concentration, inaugurée au premier trimestre 2018, produit environ 1,6 % des besoins énergétiques du pays et constitue le 5e plus grand projet d’énergie renouvelable au monde.
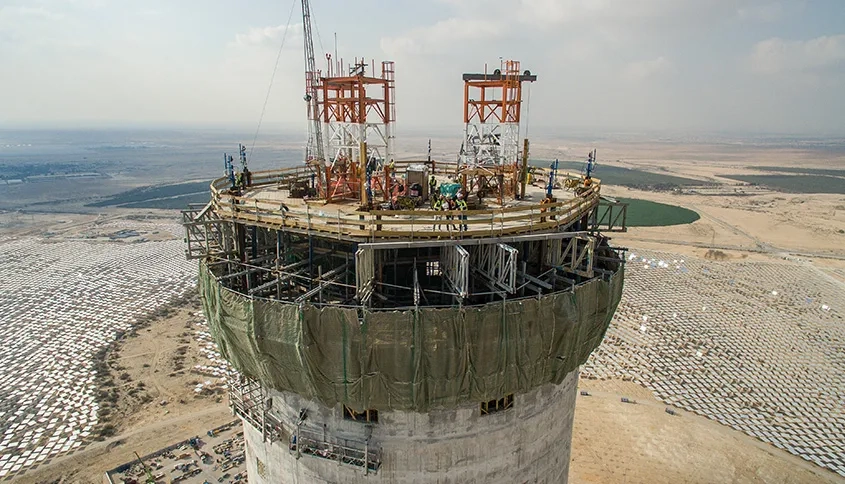
Le béton comme optimum technico-économique
Lancé en 2013 par le gouvernement israélien, l’appel d’offres pour sa construction a été remporté la même année par le consortium Megalim Solar Power Limited, piloté par General Electric. Outre les organes du process (four solaire, héliostats, générateur), la tour solaire constitue un ouvrage singulier, unique en son genre... et entièrement réalisé en béton ! « Le choix du béton relève d’un optimum technico-économique, puisque ce matériau était à la fois le moins coûteux et le plus apte à tenir les déformations que serait amenée à supporter cette structure élancée », justifie Jean-Bernard Datry, consultant et ex-directeur de l’ingénieriste français Setec TPI, en charge de la conception et des plans d’exécution de la tour solaire. La tour, dont le fût en béton s’élève à 209 m, s’apparente en effet à une gigantesque cage d’ascenseur, puisqu’elle est non seulement conçue pour soutenir le four solaire en son sommet, mais également pour permettre sa mise en place lors de la phase de construction. « L’une des caractéristiques de l’ouvrage tient d’ailleurs dans le fait que la conception du levage du four a été intégrée à la conception de la tour elle-même », détaille Jean-Bernard Datry, qui précise que l’ouvrage a été conçu selon les Eurocodes, pour une durée d’utilisation de 25 ans.
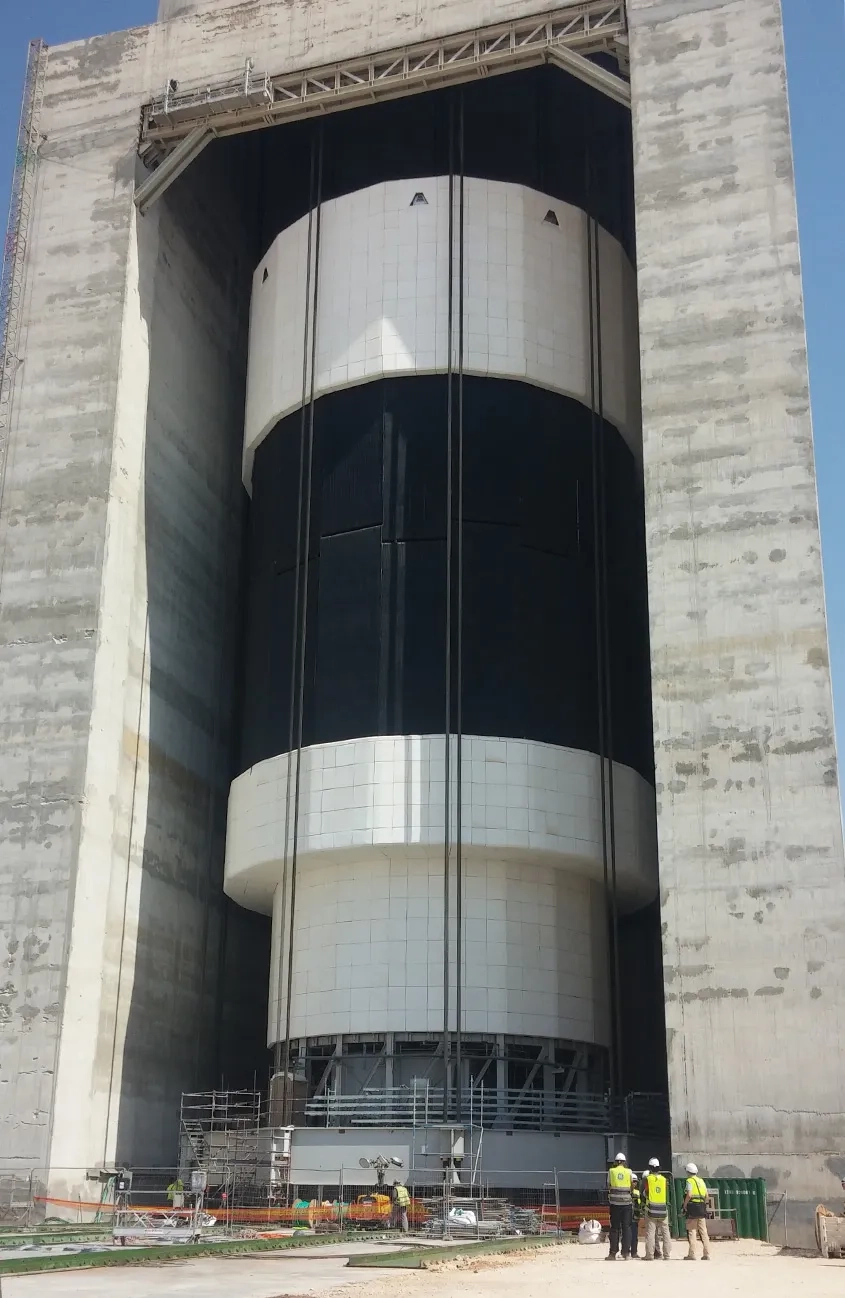
Passer d’un carré à un cercle
Le mode opératoire est ainsi conçu pour que le four solaire soit ripé à l’intérieur de la tour avant d’être hissé à son sommet par des vérins avaleurs de câbles (voir encadré). La géométrie de la tour devait évidemment tenir compte de cette contrainte de construction : c’est ainsi que afin de laisser le tirant d’air nécessaire au passage du four, la tour ménage en partie basse une ouverture en portique rectangulaire de très grande dimension (52 m de hauteur et 24 m de large).
L’enveloppe de la tour est à géométrie variable : de section carrée sur les 57 premiers mètres, elle présente une section circulaire sur les 120 m les plus hauts et une section variable de transition sur 32 m de hauteur. « Cette géométrie mixte résulte d’un compromis entre la prise au vent – minimale avec une section circulaire – et la résistance aux déformations latérales – maximale avec une section carrée », précise Jean-Bernard Datry. L’épaisseur des voiles de la tour est elle aussi variable, passant par exemple dans la zone de transition de 50 cm en pied à 35 cm en tête pour atteindre 120 cm autour du portique.
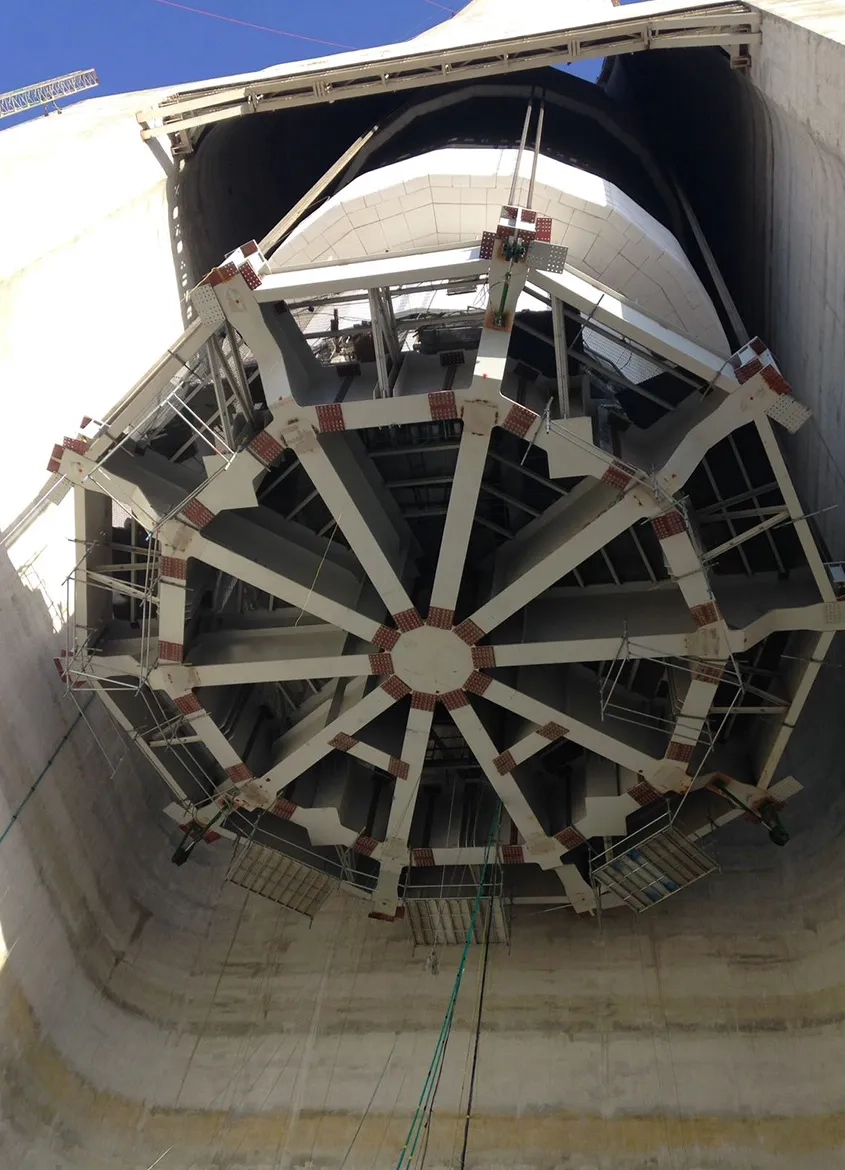
La tour s’élève de 20 cm par heure
Pour construire cet ouvrage si particulier, les équipes méthodes ont fait appel à un coffrage glissant. À l’instar des pylônes du dernier pont sur le Bosphore ou de la structure du tribunal de grande instance de Paris, la tour solaire d’Ashalim a pu être érigée avec cette technique. Elle présentait plusieurs avantages : « Contrairement au coffrage auto-grimpant qui, par la succession de phases techniques indispensables à son montage-démontage, nécessite trois ou quatre jours entre deux levées, le coffrage glissant monte en continu, 24 h/24, au rythme d’une vingtaine de centimètres par heure. Cela permettait de tenir le planning très serré de l’opération. Par ailleurs, le système de coffrage glissant conique permettait de s’adapter aux changements de géométrie de la tour – qui passe d’un carré à un cercle – sans interrompre les opérations. »
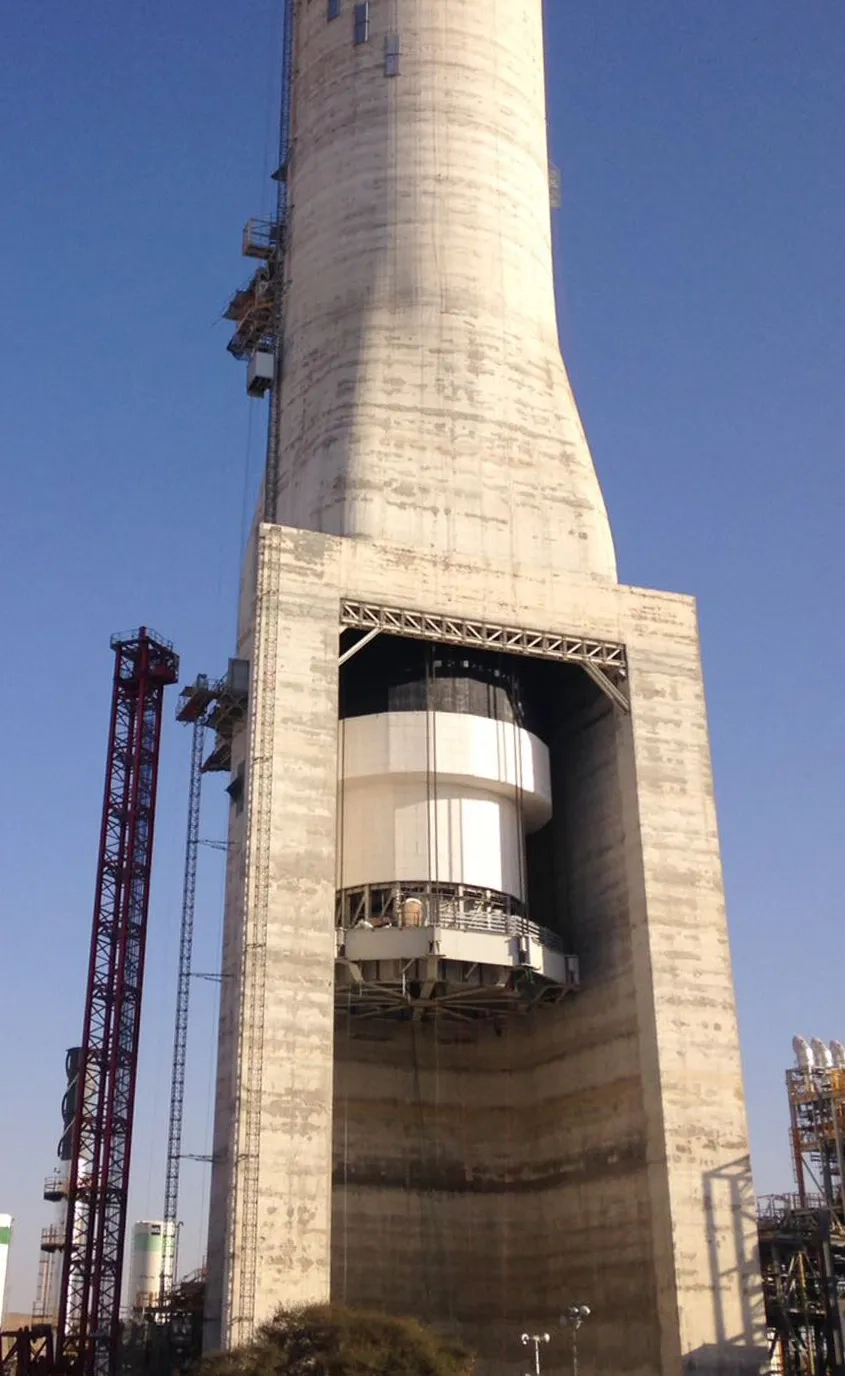
La précontrainte pour faire face à la concentration des efforts
Constituée d’un béton armé à la formulation très spécifique (voir encadré), la tour solaire comporte également plusieurs éléments en béton précontraint. « La tour aurait été “fermée”, les efforts descendants auraient été répartis selon une symétrie de révolution et le béton armé aurait suffi à les reprendre », signale Jean-Bernard Datry. Mais l’ouverture très haute et large pratiquée dans la structure crée un « vide » qui entraîne une concentration des contraintes, notamment au niveau de la traverse supérieure du portique. Pour les reprendre, le linteau est ainsi précontraint par post-tension. « Les câbles de précontrainte sont répartis horizontalement de manière à orienter les charges descendantes vers les poteaux du portique, puis dans les fondations superficielles de la tour, qui sont, elles aussi, précontraintes », illustre Jean-Bernard Datry.
Au total, trois ans et demi auront été nécessaires pour réaliser ce projet d’énergie renouvelable extraordinaire.
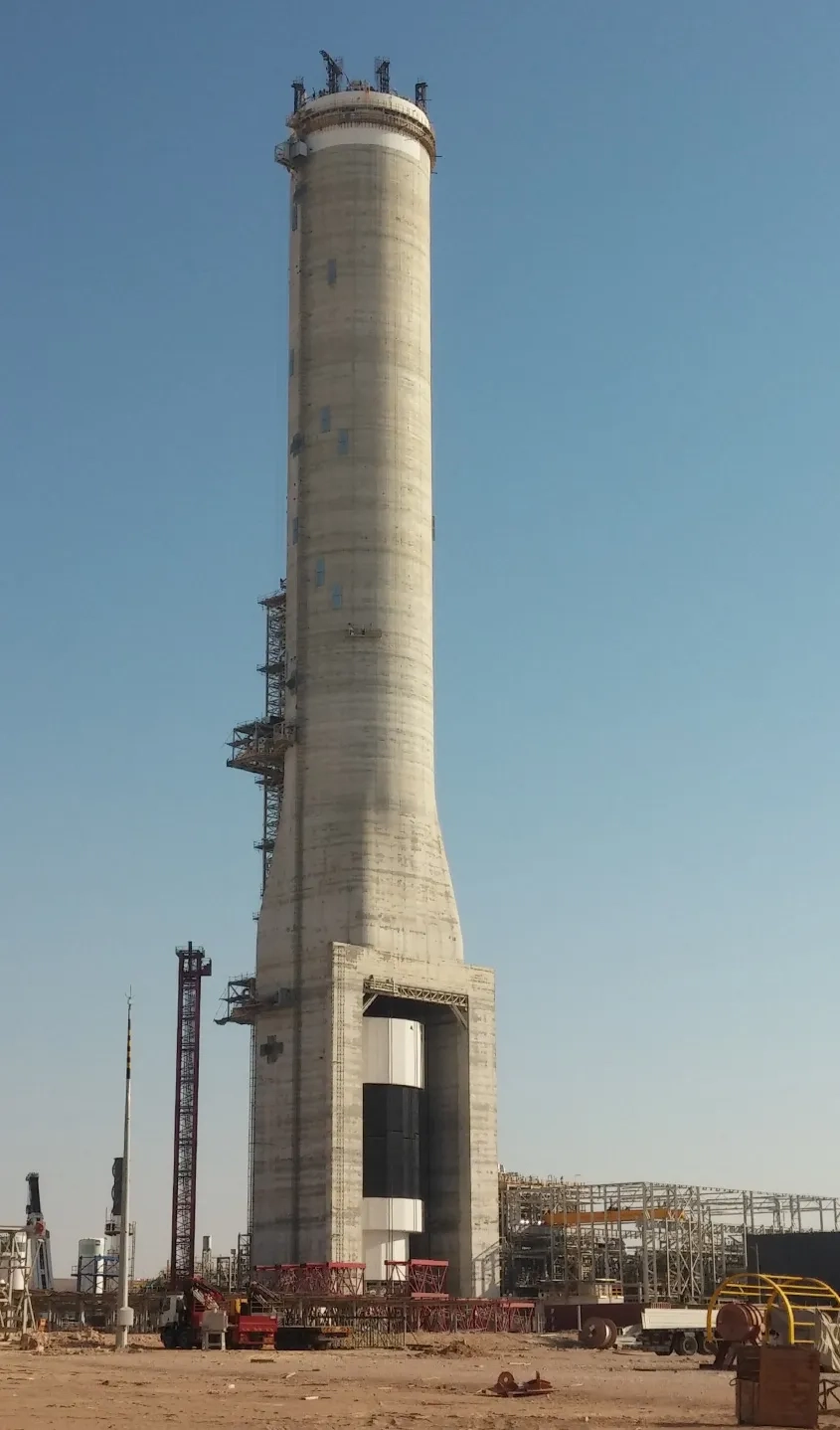
Une chaudière de 2 200 t hissée à plus de 200 m de hauteur
Les opérations de manutention nécessaires à l’installation du four solaire au sommet de la tour constituent l’un des morceaux de bravoure du chantier. Il s’agissait d’abord d’acheminer le four jusqu’à l’intérieur de la tour. Pour cela, l’entreprise spécialisée Hebetec a fait translater la chaudière de 2 200 t par une technique de ripage sur coussins d’air. Une fois positionné au centre géométrique de la tour, le four solaire a pu être hissé par 20 vérins avaleurs de câbles installés au sommet de l’ouvrage et répartis sur sa circonférence. L’ascension s’est ensuite déroulée pendant cinq jours durant lesquels les équipes de jour et de nuit se relayaient en continu. À l’issue de cette progression millimétrique, le four est resté suspendu pendant une semaine 10 cm au-dessus de sa position définitive, le temps que son support métallique puisse être finalisé.
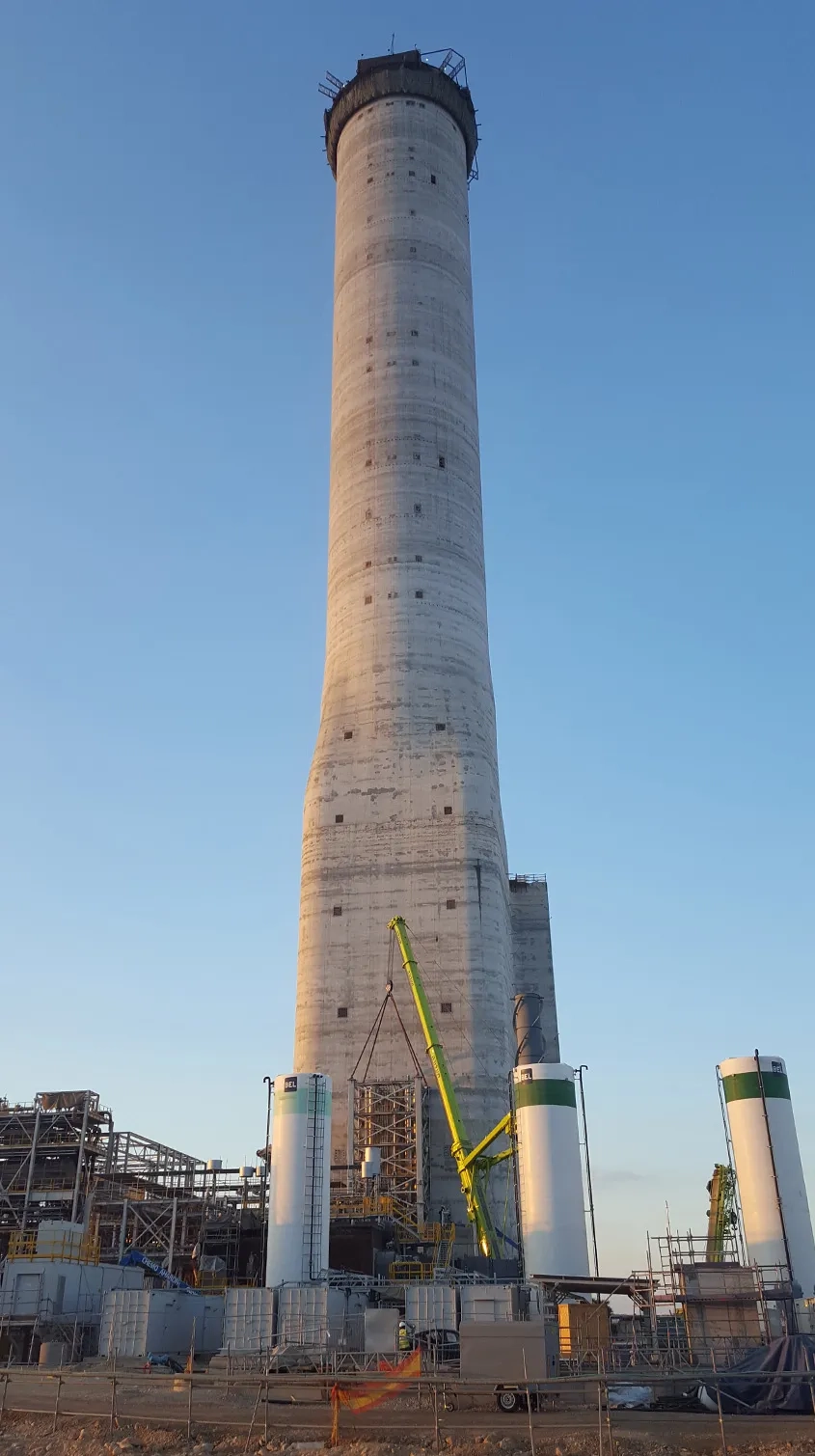
Des bétons pour résoudre la quadrature du cercle
Tel un monolithe géant dressé dans le désert, la tour solaire est entièrement constituée de béton. Son mode constructif par coffrage glissant nécessitait la formulation de bétons extrêmement spécifiques, conciliant des caractéristiques a priori contradictoires. « D’une part, les bétons ne devaient pas avoir une cinétique de prise trop rapide, pour éviter qu’ils soient arrachés lors du déplacement du coffrage, qui monte en continu, explique Jean-Bernard Datry. D’autre part, ils devaient être suffisamment fermes pour pouvoir tenir lors du hissage du coffrage via des vérins placés sur des barres scellées. Enfin, ils devaient être suffisamment fluides pour pouvoir être pompés sur de grandes hauteurs... » On l’imagine aisément : le réglage de la formulation des bétons était extrêmement précis. Les quelque 11 600 m3 de bétons coulés en place nécessaires à l’édification de la tour ont été fabriqués par une centrale à béton installée au pied de la tour.
Chiffres clés
- Diamètre du puits : 63 m
- Volume construit : 204 000 m3
- Volume de béton : environ 50 000 m3
Fiche technique
Reportage photos : Alstom GE.
- Maître d’ouvrage : Megalim Solar Power Ltd
- Responsable du projet clef en main, conception de l’usine et de la chaudière : General Electrics
- Concepteur du preliminary design et constructeur de la tour : Ferbeck Industrial Chimneys
- Conception, calculs et plans d’exécution de la tour béton : Setec TPI
- Levageur de la chaudière : Hebetec
- Fournisseur outil coffrant : Gleitbau
- Coût total : 660 M€, dont 25 M€ pour le Génie Civil.
COMMENTAIRES
LAISSER UN COMMENTAIRE