Des méga-poutres en béton (très) armé pour reconstruire la ville dense
Portée par neuf méga-poutres en béton armé, une dalle déployée au-dessus des voies ferrées de la gare d’Austerlitz devient « sol » aedificandi.
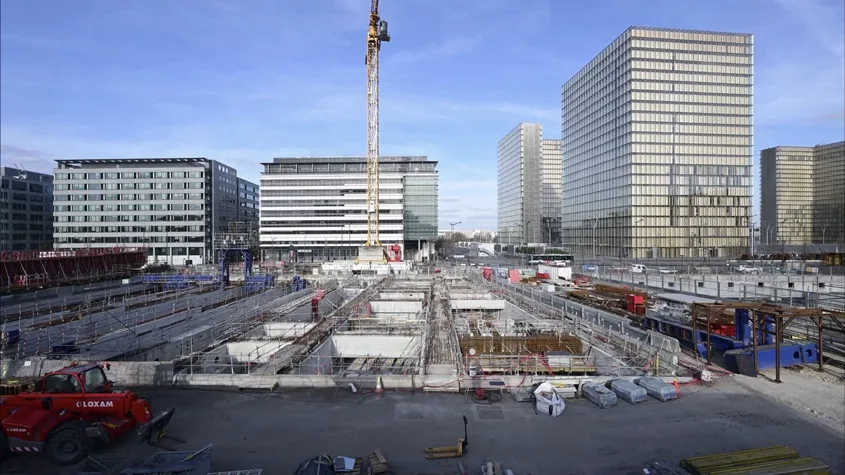
Répondre à la raréfaction du foncier...
La raréfaction de l’offre de foncier dans les hyper-centres-villes conduit les maîtres d’ouvrage à explorer des solutions innovantes pour maximiser l’utilisation des espaces disponibles. Le projet Aurore T5B, situé dans le 13e arrondissement de Paris, est un exemple emblématique de cette reconstruction de « la ville sur la ville ». Ce programme ambitieux, qui comprend un hôtel de luxe et un bâtiment culturel pour une surface de planchers totale de 12 000 m², est en effet situé… au-dessus des voies ferrées de la gare d’Austerlitz !
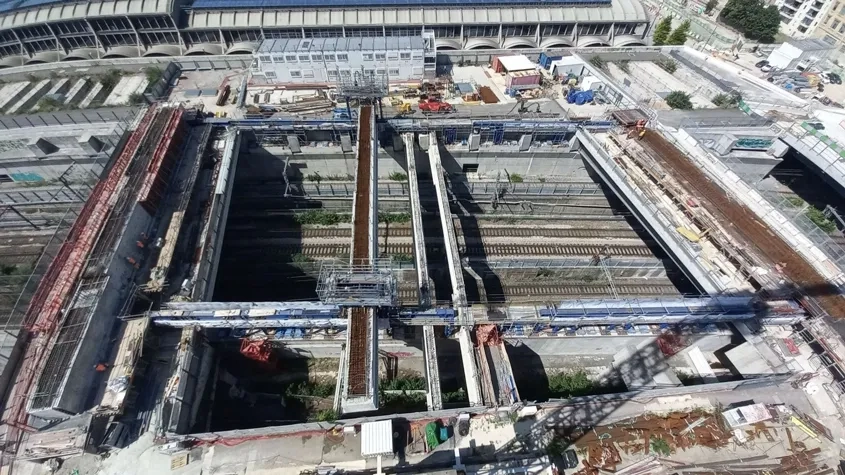
... par un pont habité soutenu par neuf méga-poutres en béton armé !
Pour répondre à cette contrainte rare, les bâtiments reposent sur une dalle de couverture construite au-dessus des voies ferrées. « Cette dalle est en réalité un véritable ouvrage d’art », pose Nabil Lahmidi, responsable travaux pour Egis, maître d’œuvre du projet (voir encadré 1). Sa structure est en effet composée de neuf méga-poutres en béton armé. « Ces poutres géantes de grande section – 2,5 m de largeur et 3,4 m de hauteur, dépassant 600 t – développent une portée allant jusqu’à 46 m, ce qui leur permet de franchir la faille constituée par le faisceau ferroviaire », poursuit Nabil Lahmidi.
Destinées à reprendre les charges des bâtiments en superstructure, les méga-poutres sont également conçues pour « porter » le sous-sol des bâtiments. « La Compagnie de Phalsbourg, notre maître d’ouvrage, souhaitait pouvoir disposer les locaux techniques de ses bâtiments sous le niveau de la dalle. L’espace interstitiel situé entre deux méga-poutres est donc utilisé pour y installer des locaux visitables de 2 m de hauteur sous plafond », décrit Régis Rancier, responsable études pour Egis. Ce sous-sol « suspendu », dont les âmes des méga-poutres constituent les murs, devait être conforme à la réglementation incendie. « C’est principalement pour cette raison de résistance au feu que la solution béton a été préférée à l’acier », justifie Régis Rancier.
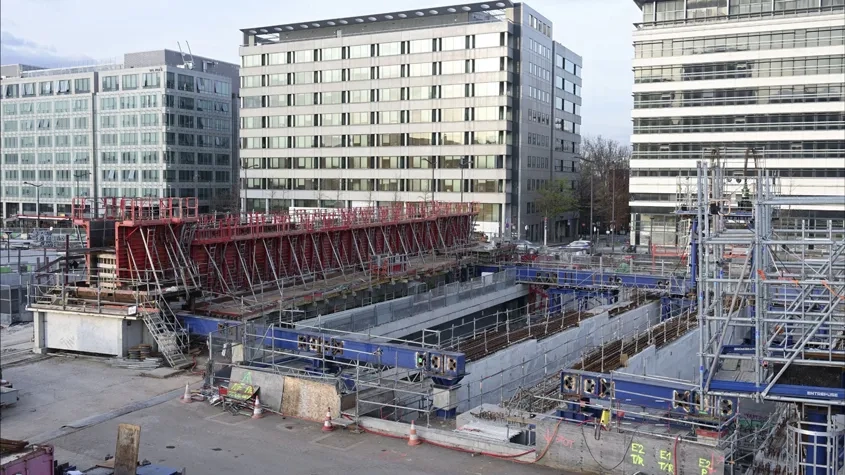
Des grandes portées sans précontrainte
Fait notable, ces méga-poutres sont réalisées en béton armé – une véritable prouesse pour des éléments massifs d’aussi longue portée (voir encadré 2) – et non pas en béton précontraint. « La SNCF rétrocédant la dalle à notre maître d’ouvrage, elle n’assurera pas la maintenance technique de l’ouvrage. Or les systèmes de précontrainte nécessitent la mise en place de suivis réguliers dans le temps. C’est pour cette raison que la SNCF souhaitait que les structures soient entièrement en béton armé. » En réalité, certaines des méga-poutres intègrent un système de précontrainte. « Mais il s’agit d’une précontrainte spécifique qui permet de ne pas solliciter les armatures du béton armé durant les phases de construction. Elle n’est en revanche pas prise en compte dans le dimensionnement pour les cas de charges les plus sévères en phase définitive », détaille Régis Rancier.
Une préfabrication « allégée »
Côté chantier, la fabrication et la mise en place des méga-poutres constituaient les principaux enjeux techniques du projet. « Toutes les méga-poutres étaient réalisées sur deux aires de préfabrication foraines installées sur deux futurs ouvrages de franchissement mitoyens situés de part et d’autre de notre chantier, indique Nabil Lahmidi. Cette proximité permettait d’acheminer les poutres, une fois leur construction achevée, directement sur le chantier, en évitant ainsi des manutentions intermédiaires complexes. »
Néanmoins, le poids unitaire de chaque élément était si important qu’il a été décidé de réaliser les structures des méga-poutres en deux temps. « Sur l’aire de la préfabrication, nous coulions avec du béton à haute résistance le “U” extérieur de la poutre comprenant la semelle inférieure et les deux ailes de l’âme, précise le responsable travaux. Seuls les abouts des poutres étaient pleins pour pouvoir installer les ancrages de précontrainte le cas échéant. » Cette relative légèreté permettait de déplacer les poutres plus facilement dans les phases ultérieures.
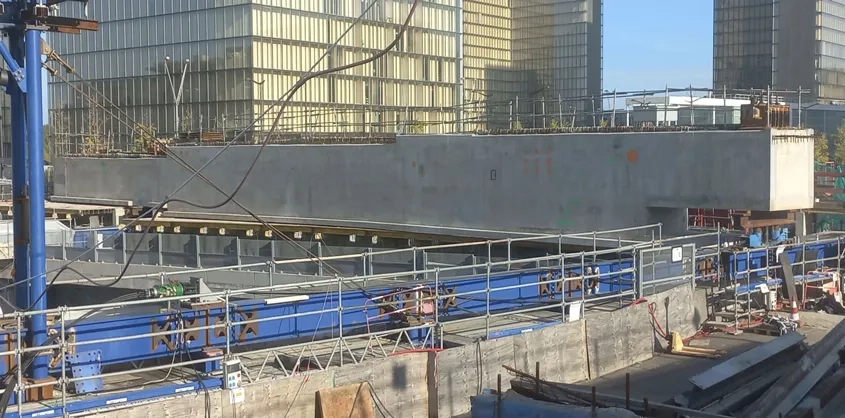
Un ripage et une descente sous contrôle
Une fois les poutres en « U » ainsi achevées, elles étaient directement ripées depuis l’aire de préfabrication grâce à des vérins. « Ces vérins dits “avaleurs” de câbles permettaient de tirer les méga-poutres sur le chemin de ripage jusqu’à ce qu’elles soient positionnées au-dessus de leurs appuis définitifs », explique Régis Rancier. Restait alors à les faire descendre jusqu’à leur position finale. Pour cela, des portiques de levage synchronisés étaient positionnés de part et d’autre de chaque méga-poutre. « Le premier mouvement que nous faisions subir aux poutres était un soulèvement de quelques millimètres, note Nabil Lahmidi. Cela nous permettait de retirer le tronçon du chemin de ripage sur lequel la poutre était appuyée jusque-là, supprimant ainsi tout obstacle à la descente. » Les méga-poutres étaient alors délicatement descendues jusqu’à leurs appareils d’appui situés 3 m plus bas. « Une fois les poutres en place, nous procédions alors au coulage de leur cœur, pour obtenir un volume plein et fermer le “U”. »
Deux heures de chantier au milieu de la nuit
Pour ne pas perturber l’exploitation des voies de la gare d’Austerlitz, toutes les opérations de déplacement des méga-poutres décrites ci-dessus étaient réalisées de nuit. « Notre chantier ne pouvait démarrer qu’une fois la circulation ferroviaire arrêtée et les caténaires coupées, si bien que nous ne disposions que d’une fenêtre de deux heures chaque nuit pour effectuer les différentes opérations, décrit Nabil Lahmidi. Au final, avec ce séquençage très contraint, entre huit et neuf nuits étaient nécessaires pour déplacer chaque méga-poutre depuis l’aire de préfabrication jusqu’à sa position définitive ! »
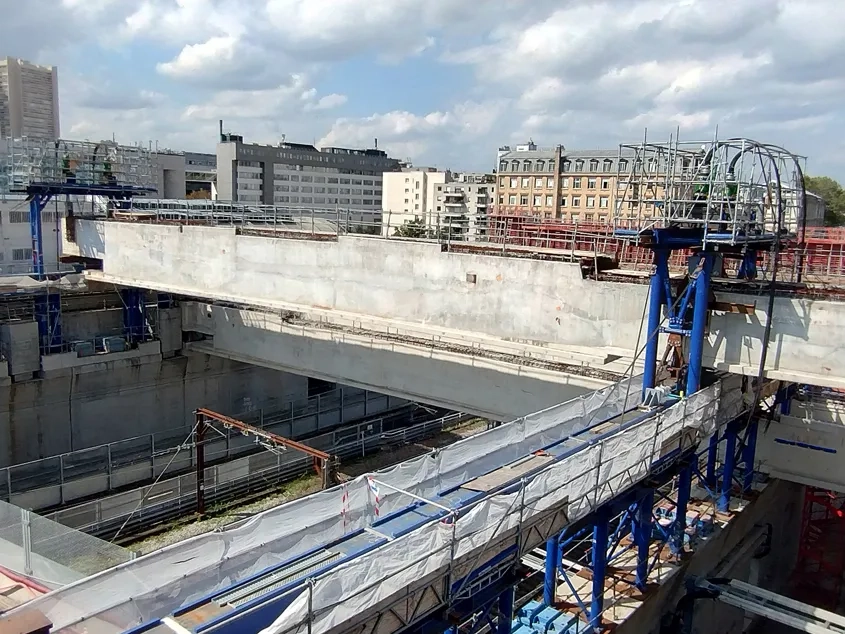
Mais la patience est payante et, une fois les neuf méga-poutres en place, le chantier de la dalle a pu s’achever par la réalisation des planchers haut et bas des locaux techniques « suspendus » entre deux poutres. Et malgré une histoire mouvementée, le génie civil a pu être achevé un mois avant le démarrage de Paris 2024… Objectif atteint !
Un maître d’œuvre à la rescousse !
En décembre 2020, un incident technique grave – n’impliquant toutefois aucun accident de personne – survient sur le chantier de la dalle de couverture du T5B, démarré un an auparavant. Le projet est alors mis en pause pendant deux ans. Durant cette période, le maître d’ouvrage fait appel au Cerema, dans un premier temps pour mener un audit structurel des éléments déjà réalisés, et dans un deuxième temps pour assumer la conception en place et achever le projet en remplacement du maître d’œuvre précédent. Les travaux ont ainsi pu reprendre en février 2023 pour s’achever avant la tenue des Jeux olympiques.
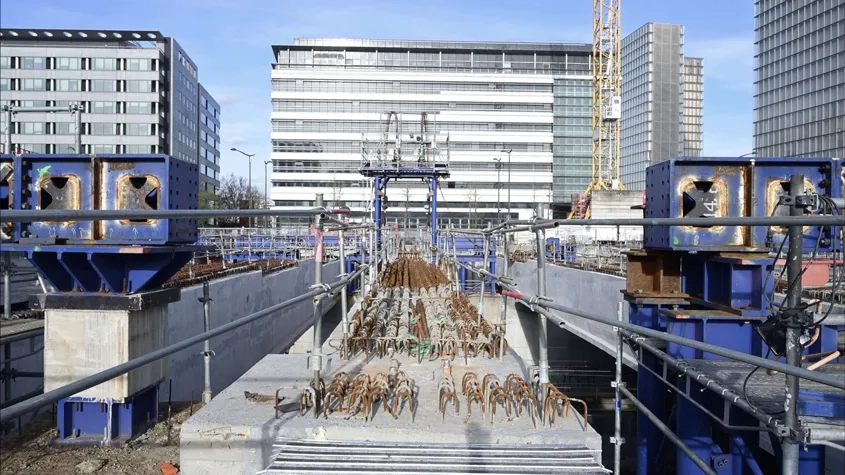
Des bétons à haute performance pour atteindre des portées exceptionnelles
En phase définitive, les méga-poutres sont dimensionnées en béton armé sans considérer la précontrainte. Autant dire que pour soutenir des portées allant jusqu’à 46 m, ces éléments structurels géants disposent de capacités exceptionnelles. Côté béton d’abord : la section en « U », réalisée sur l’aire de préfabrication, est ainsi constituée de béton à haute performance de type C60/75. Pour pouvoir tenir les cadences de production suite à la reprise du chantier, le groupement d’entreprises de génie civil souhaitait que les bétons disposent d’une très grande résistance au jeune âge. « Mais il fallait que cette montée en résistance n’entraîne pas une montée trop importante de la température au cœur des structures, afin de limiter les risques d’apparition de pathologies du béton, décrit Nabil Lahmidi. Pour nous en assurer, nous avons fait des essais de convenance, en instrumentant notamment la poutre avec des sondes de température. Le résultat s’est avéré très concluant : la formulation de béton, intégrant un mélange de ciments de type CEM I, pour la résistance au jeune âge, et de type CEM III, pour limiter la chaleur d’exothermie, nous permettait d’atteindre 60 MPa de résistance à la compression en seulement sept jours et ce, sans dépasser les seuils de température recommandés. »
La forte résistance des méga-poutres passe aussi par une quantité d’armatures très importante, en particulier au cœur des sections : la densité moyenne d’armatures y est de 300 kg/m3. « Pour pouvoir traverser ce maillage d’acier très dense, nous avons formulé un béton fluide – qui n’est toutefois pas un béton autoplaçant – dont la mise en place par gravité était accompagnée d’un vibrage conventionnel », conclut Nabil Lahmidi.
Localiser la réalisation
Reportage photo : © EGIS, © LEON GROSSE, © COMPAGNIE DE PHALSBOURG
COMMENTAIRES
4 COMMENTAIRES