Première en France : l’étanchéité d’un viaduc autoroutier rénovée avec du BFUP
Sur l’autoroute A36, la réfection de l’étanchéité du viaduc franchissant le canal de dérivation de la Saône a été réalisée en béton fibré à ultra hautes performances (BFUP). Ce matériau très technique, habituellement réservé à des applications structurelles, a été préféré aux matériaux et procédés d’étanchéité classiques. Une analyse multicritère tenant compte des spécificités de conception de l’ouvrage et de son environnement a ainsi conduit APRR, exploitant de l’A36, à expérimenter cette solution, inédite en France.
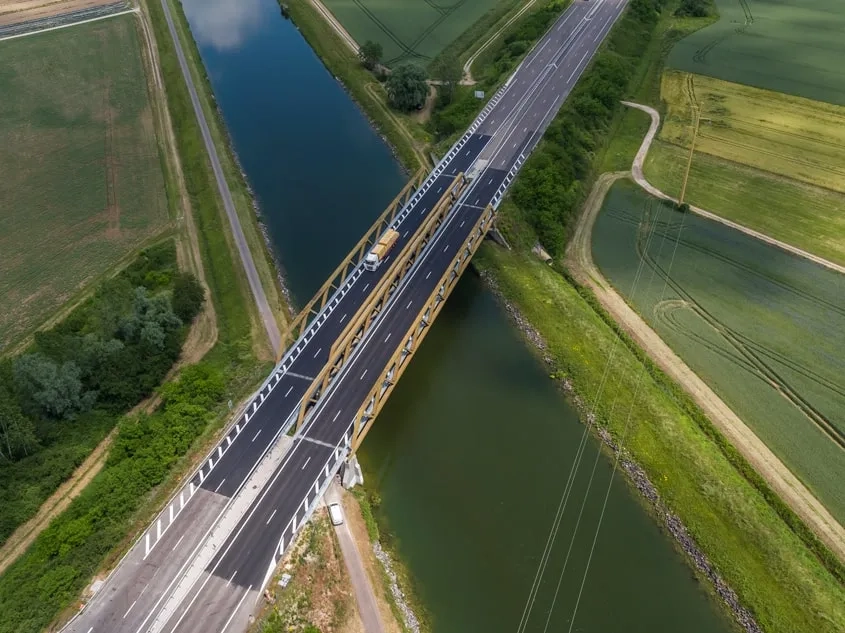
Dans le cadre de son contrat de concession avec l’État, APRR est engagé à lui rendre à son terme une infrastructure dans un bon état d’entretien. Dans cette perspective, le concessionnaire a intérêt à maximiser la durée de vie de son patrimoine. C’est dans cette logique qu’APRR (groupe Eiffage) prend soin de l’autoroute A36, dont l’exploitation et l’entretien lui ont été confiés jusqu’à fin 2035 dans le contrat actuel. Le chantier de réfection de l’étanchéité du viaduc de franchissement du canal de dérivation de la Saône en est une belle illustration.
Une étanchéité victime de l’effet « radiateur »
Cet ouvrage, situé en Côte-d’Or entre Beaune et Dole, est un double tablier mixte acier-béton monotravée de 100 m de long à poutres métalliques extradossées de type « Warren ». Construit en 1980, sa couche de roulement présentait des pathologies récurrentes, que les reprises successives d’enrobés, et notamment la dernière en date, en 2018, n’avaient pas réussi à résorber. « En 2020, nous avons constaté le décollement partiel et le fluage du complexe enrobé/étanchéité sur la voie lente, ce qui créait des risques d’accident importants », relate Romain Pittet, responsable patrimoine ouvrages d’art-tunnels chez APRR. Ce phénomène, causé par une forte exposition à la chaleur l’été et une grande amplitude thermique, était en réalité lié à la conjonction de deux problèmes de conception : « D’une part l’épaisseur des matériaux – dalle béton du tablier et complexe étanchéité/enrobé – était trop faible pour dissiper la chaleur en plein été. D’autre part, les poutres métalliques avaient tendance à conduire la chaleur accumulée en sous-face de la dalle. » Cet effet « radiateur » renforçait et accélérait les phénomènes de décollement et de fluage.
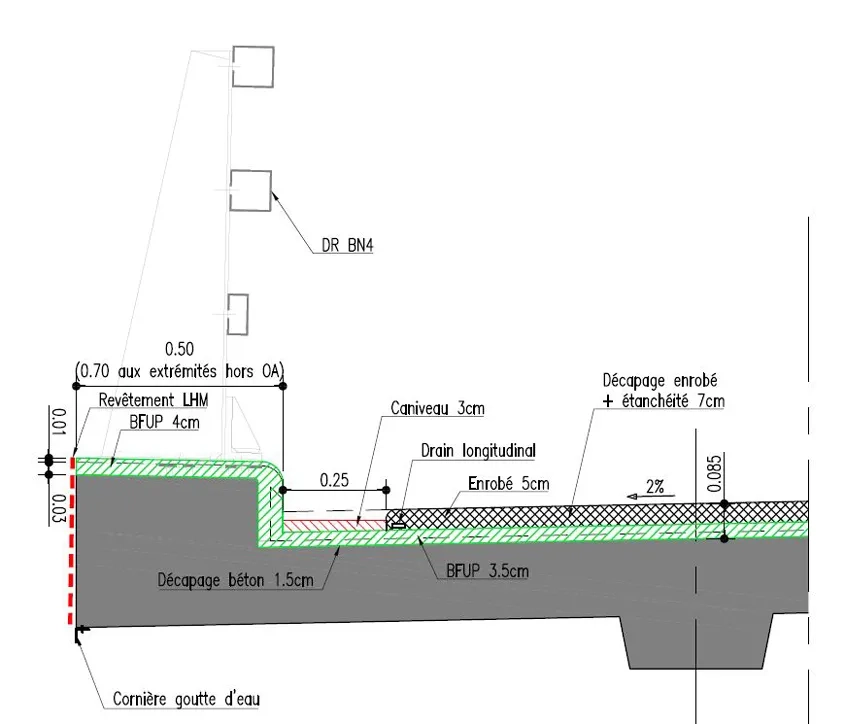
Des contraintes fortes de conception
« Forts de ce constat, nous avons alors décidé de reprendre l’intégralité de l’étanchéité de l’ouvrage », poursuit Romain Pittet. Plusieurs solutions ont alors été étudiées. « Nous avons mené une analyse multicritère rigoureuse sur la base des contraintes qui s’imposaient à nous et des objectifs que nous nous étions fixés. » Les contraintes principales étaient au nombre de trois : « Il fallait tout d’abord que nous n’augmentions pas le poids propre de l’ouvrage, sinon nous aurions été obligés de le renforcer. Cela signifiait notamment que nous devions conserver une faible épaisseur d’enrobés. Ensuite, nous devions trouver un procédé qui puisse résister durablement aux fortes chaleurs et à l’effet « radiateur » induit par la conception de l’ouvrage. Enfin, le chantier devait se dérouler dans un délai serré, pour minimiser la gêne à l’usager. » Les objectifs principaux de la rénovation étaient quant à eux les suivants : « Nous voulions que la réfection soit pérenne dans le temps, pour que nous n’ayons pas à y revenir régulièrement. Pour garantir une protection uniforme sur toute la largeur de l’ouvrage, il fallait aussi que l’étanchéité couvre de manière continue le hourdis du tablier et les longrines latérales. »
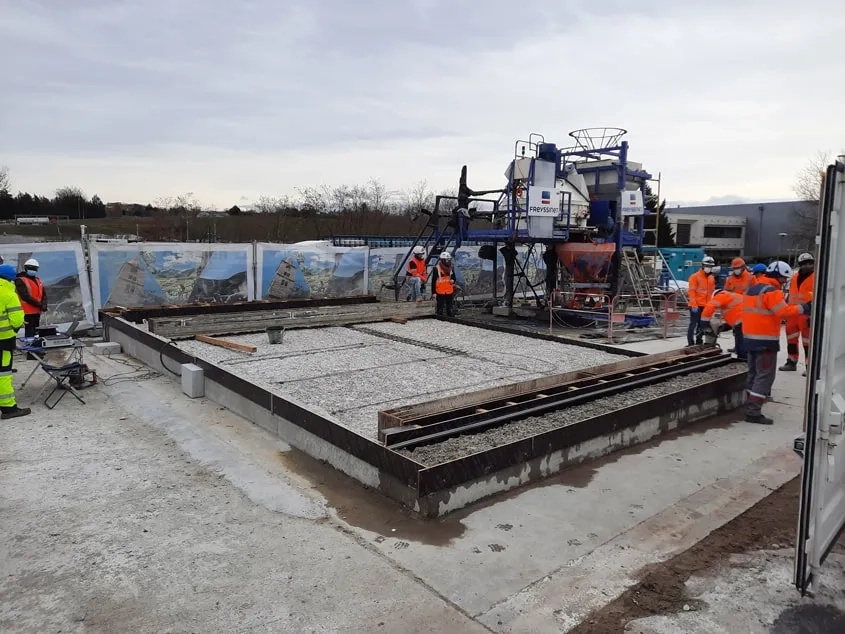
Le BFUP en étanchéité, une solution suisse
Dans le catalogue des solutions classiques d’étanchéité (1), aucune ne répondait à l’ensemble de ces critères. « Mais nous avions pris connaissance, à l’occasion du colloque "Le Pont" en 2017 à Toulouse (https://www.le-pont.com), d’une solution disposant d’un large retour d’expérience positif sur plus de 90 ouvrages suisses, jamais éprouvée en France, et qui cochait toutes les cases de notre cahier des charges : l’étanchéité en béton fibré à ultra hautes performances (BFUP). »
Les BFUP sont des matériaux très techniques habituellement employés pour des applications structurelles, aussi bien en ouvrage neuf qu’en renforcement d’ouvrages existants. « Ils disposent d’une très forte compacité et d’une très faible perméabilité. Néanmoins, les performances attendues sur notre ouvrage nécessitaient d’une part de sélectionner un BFUP très fibré avec de hautes performances en traction et d’autre part une mise en œuvre particulière pour garantir un rôle d’étanchéité globale », note Romain Pittet. Or, le corpus normatif français (2) ne permettait pas directement cette application BFUP. « Pour y parvenir, nous nous sommes inspirés du référentiel technique suisse – le cahier technique SIA 2052 : 2016 – dont nous avons repris certains paramètres en vérifiant qu’ils étaient compatibles avec les normes que nous utilisons en France », précise Romain Pittet.
Cet usage combiné des corpus permettait notamment de pouvoir répondre aux exigences techniques complémentaires qu’il fallait obtenir, à savoir un matériau écrouissant en traction, permettant en cas de fissuration le développement de multiples fissures très rapprochées (multifissuration), afin de garder la perméabilité la plus faible possible sur le long terme.
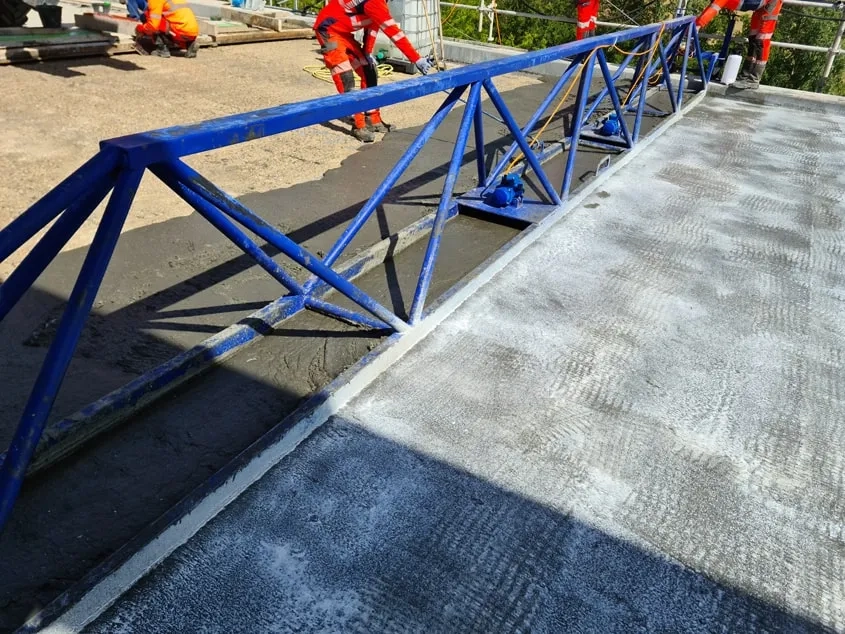
Une méthodologie finement définie
Une fois la formulation de matériau trouvée (voir encadré 1), encore fallait-il définir la bonne méthodologie de mise en œuvre. « Nous avons pu nous appuyer pour cela sur le protocole expérimental défini par le comité technique BFUP A36 (voir encadré) », explique Benjamin Simian, responsable d’activité pathologie et réparation des ouvrages chez Ingerop, maître d’œuvre du projet.
La bonne réalisation de l’étanchéité BFUP sur l’ouvrage existant passait ainsi par un phasage précis. Tout d’abord, il s’agissait de raboter l’enrobé et l’étanchéité existants. À cette étape de curage succédait celle du surfaçage du béton support par hydrodémolition. « L’objectif de cet atelier était de créer une macrorugosité optimale pour assurer l’adhérence à l’interface du BFUP et du béton. Il faut en effet noter que la connexion mécanique entre les deux matériaux n’était pas réalisée par l’intermédiaire de connecteurs, mais par une simple reprise de bétonnage », poursuit Benjamin Simian. Le support était ensuite humidifié à l’aide d’un brumisateur afin d’améliorer les conditions de prise et d’adhérence du BFUP, coulé en une couche de 3,5 cm d’épaisseur. Enfin, l’enrobé était mis en œuvre sur 5 cm d’épaisseur après hydrodécapage du BFUP et emploi d’un primaire pour améliorer l’adhérence du matériau bitumineux sur le BFUP.
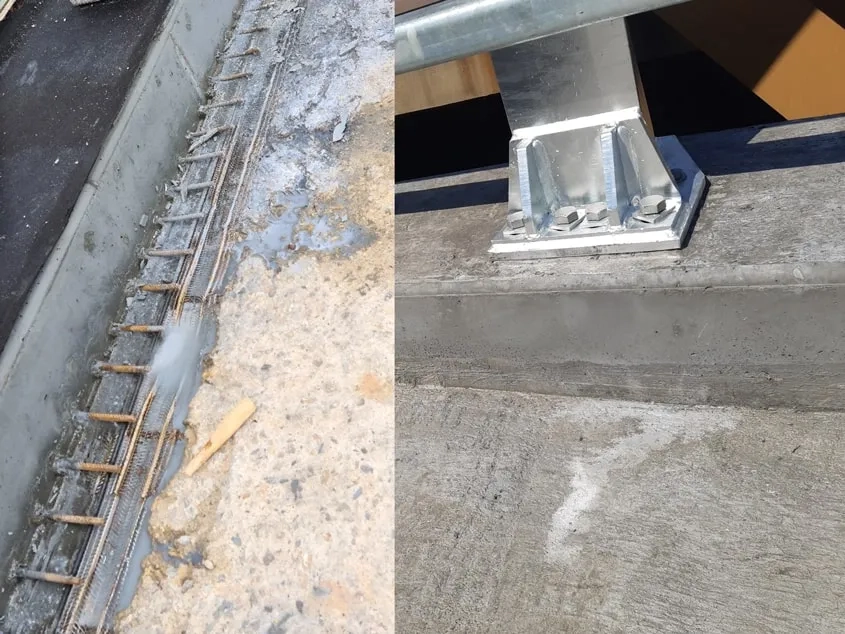
Une fabrication foraine et sur mesure
« Les contraintes de fabrication et de mise en œuvre du BFUP étaient fortes », note Pascal Ferraton, de Freyssinet, en charge de la réalisation des travaux. « Pour pouvoir tenir les délais serrés, nous avons installé une centrale de fabrication foraine sur le chantier. Chaque jour, nous devions adapter légèrement la formulation du BFUP aux conditions climatiques que nous rencontrions pour qu’il garde les caractéristiques demandées et conserve l’ouvrabilité recherchée. » La qualité du matériau était ainsi surveillée de très près – chacune des 250 gâchées était contrôlée à l’état frais, et des contrôles sur le béton durci étaient réalisés tous les 10 m3.
Finalement, grâce à l’implication de tous, les travaux de ce chantier inédit, menés au printemps 2021, ont pu être achevés dans le temps imparti – 11 semaines au total, en basculant la circulation à mi-parcours. Le suivi sur dix ans de l’ouvrage avec les experts du comité technique BFUP A36 permettra de contrôler son évolution. Mais le maître d’ouvrage a bon espoir : « Nous estimons que la durée de vie de cette étanchéité sera deux à trois fois supérieure à celle des procédés classiques », conclut Romain Pittet.
(1) Les trois solutions classiques analysées étaient : le système d’étanchéité liquide (SEL), la feuille préfabriquée monocouche (FPM) et la FPM complétée d’une résine bouche-pores.
(2) Les trois normes BFUP françaises sont les normes NF P 18-451, NF P 18-470 et NF P 18-710
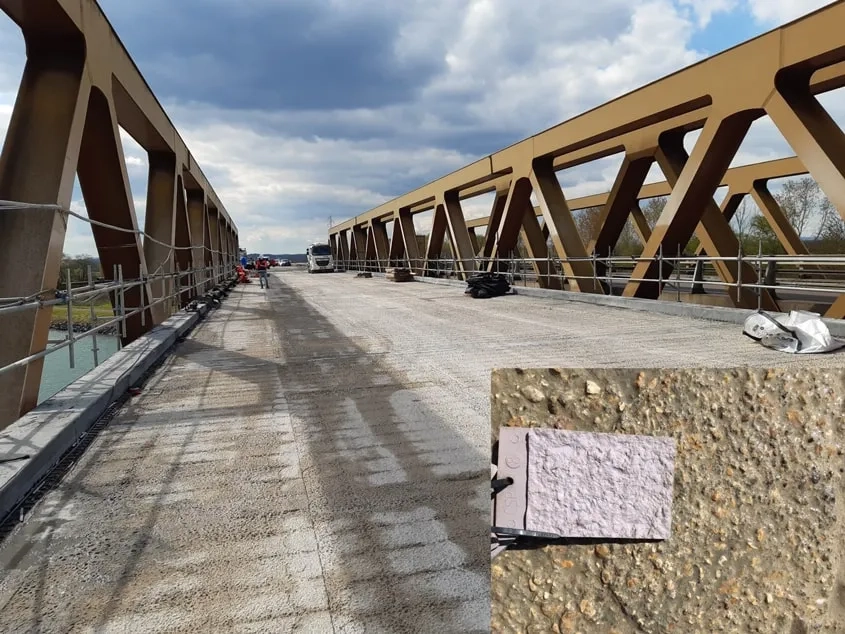
Un BFUP étanche formulé sur mesure
Pour arriver à formuler un béton fibré à ultra hautes performances le plus imperméable possible, coulé en place et répondant aux contraintes de mise en œuvre (coulage sur pente de 2 %, adhérence au support...), les équipes de la direction de l’Innovation appliquée de Vicat ont adapté finement les caractéristiques de leur BFUP maison – le Smart-Up. Finalement, le BFUP retenu a un comportement en traction de type T2 (peu écrouissant, selon la norme NF P18-470) avec une limite élastique supérieure à 7 MPa et une limite à rupture au-delà de 10 MPa. Il possède également une classe de porosité à l’eau améliorée (classe Dp+).
Un chantier expérimental suivi à la loupe
Pour aider au bon déroulement de cette expérimentation, le concessionnaire APRR a créé un comité technique ad hoc. Constitué d’experts reconnus du BFUP, ce comité a proposé la mise en place de deux dispositifs d’accompagnement et d’observation. Le premier a pris la forme d’une dalle de convenance de 5 x 10 m, véritable modèle réduit de la dalle du pont, destinée à valider les procédures d’exécution en termes de critères et de performances pour le chantier, ainsi qu’à vérifier l’adéquation de la formulation du BFUP. « La réalisation de cet élément témoin particulièrement complet dans le cadre de l’épreuve de convenance a rendu le chantier plus fluide en permettant d’améliorer en amont la préparation du chantier, ainsi que la fabrication et le process de mise en œuvre », explique Benjamin Simian. Le comité technique a également conseillé la réalisation d’une dalle « témoin de vieillissement ». De conception identique à la dalle du viaduc, elle est implantée à proximité, exposée aux mêmes conditions météorologiques et de salage que l’ouvrage. « Cette dalle de vieillissement va permettre d’appréhender l’évolution des performances dans le temps. Des éprouvettes seront prélevées périodiquement jusqu’à dix ans. » En complément, l’un des deux tabliers de l’ouvrage a été instrumenté pour pouvoir suivre en temps réel le comportement de l’étanchéité. Le suivi sera réalisé pendant dix ans.
Localiser la réalisation
Le chantier en chiffres
- 150 m3 de béton fibré à ultra hautes performances
- 44 tonnes de fibres métalliques
- 2 500 m2 de surface de tablier traités
- 2,5 mois de travaux
Fiche technique
- Exploitant et maître d’ouvrage : APRR direction du Patrimoine et des Opérations
- Maître d’œuvre : Ingerop agence Alpes Centre-Est
- Entreprise : Freyssinet agence Rhône-Alpes-Auvergne
- Fournisseur BFUP : Vicat, direction de l’Innovation appliquée
- Contrôle extérieur BFUP : Cerema – Université Gustave Eiffel
- Instrumentation : Quadric
COMMENTAIRES
LAISSER UN COMMENTAIRE