Le renouveau de la construction hors site
Les multiples contraintes environnementales et réglementaires qui s’imposent désormais aux ouvrages relancent l’intérêt pour la construction hors-site. Entre tradition et innovation, ce mode constructif fondé sur la notion de préfabrication ouvre la voie à de nouvelles approches.
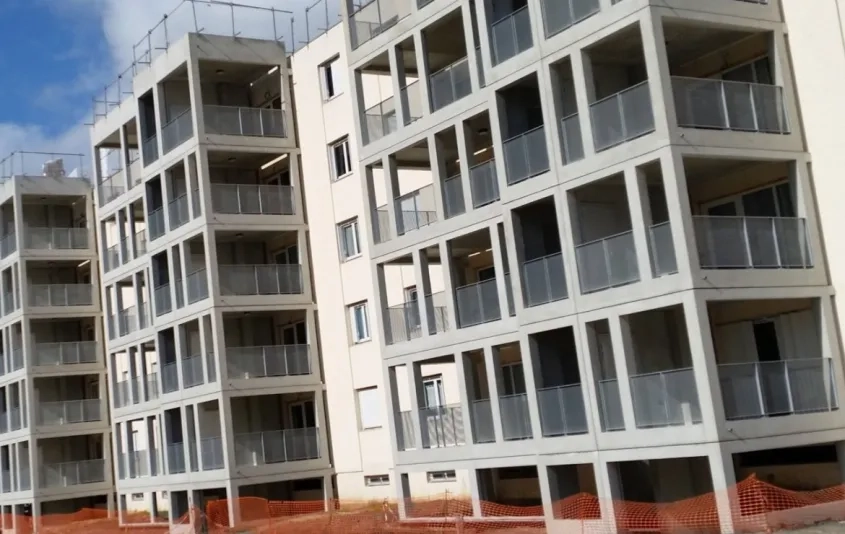
Réduire les délais de mise en œuvre, s’affranchir des aléas climatiques, diminuer la pénibilité des chantiers, limiter les nuisances pour les riverains, tout en maintenant, voire renforçant, un haut niveau de qualité des ouvrages : cette équation, pour complexe qu’elle soit, trouve une solution dans l’industrialisation des composants de l’ouvrage.
Depuis longtemps, la préfabrication est associée aux matériaux acier, béton et maintenant bois. Toutefois, la part des produits préfabriqués reste mineure en France, contrairement à certains pays d’Europe du Nord, d’Amérique du Nord ou d’Asie, zones géographiques dans lesquels la construction hors -site connaît une croissance à deux chiffres.
L’élan donné par les grands chantiers des métropoles urbaines, associé à la difficulté de recrutement de main d’œuvre qualifiée sur site, accélère l’approche de construction hors-site. Les articles 65 et 67 de la loi ELAN définissent la notion de préfabrication, qui « consiste à concevoir et réaliser un ouvrage à partir d’éléments préfabriqués assemblés, installés et mis en œuvre sur le chantier ». Le texte précise également que les éléments préfabriqués peuvent être produits sur un site qui peut être soit une usine ou un atelier, soit une installation temporaire jouxtant le chantier (préfabrication foraine).
Préfabrication et béton : une tradition renouvelée
La technique de préfabrication pour le béton est utilisée depuis la seconde moitié du XIXe siècle. Elle a su évoluer au cours du temps pour intégrer les évolutions technologiques de fabrication en usine : CAO, robotisation, modélisation 3D…. Ce mode de fabrication est naturellement associé à la notion de contrôle continu de la qualité. Depuis des décennies, les chantiers sont ainsi livrés en planchers, poteaux, poutres, escaliers, blocs, balcons… tout composant d’un ouvrage durable. Tous ces éléments sont indépendants les uns des autres, et autorisent tous les types de réalisation.
Les avantages de la solution « préfa » sont nombreux : réduction importante de la durée du chantier de gros œuvre, rapidité de montage, hautes qualités thermiques, sismiques, comportement incendie, propreté du chantier et plus globalement la réduction des nuisances. Et si les produits sont industrialisés, la liberté de conception n’en est pas moins diminuée, le sur-mesure faisant également partie intégrante de l’offre industrielle.
Une nouvelle catégorie d’éléments préfabriqués fait aujourd’hui son apparition : l’élément modulaire, ou élément 3D. Il s’agit ici d’une cellule complète, associant les éléments traditionnels horizontaux et verticaux, mais en apportant en plus une notion de profondeur. « Nous devenons des équipementiers, en intégrant à la structure béton l’équipement électrique, la plomberie, les revêtements de sols ou murs, voire le mobilier ! » explique Patrick Soubiran, Directeur commercial chez CIR-Préfa.
« Nous intégrons de nouvelles compétences, tant en usine que sur site, puisque nos équipes assurent le montage des éléments afin de garantir la meilleure précision dans l’ajustement des modules » complète-t-il.
En assurant le « tout corps d’état », l’industriel apporte ainsi à son client la sérénité, en maîtrisant au maximum les aléas de réalisation en usine, et en limitant les interventions sur chantier.
La construction hors-site : des atouts environnementaux et des avantages économiques
Fabriquer en usine permet d’optimiser le dimensionnement des éléments, et donc de générer moins de déchets, moins d’emballages.
Ce mode de fabrication permet également d’intégrer plus rapidement les évolutions liées à la transition environnementale : réduction de l’empreinte carbone, recours aux ressources locales ou recyclées, réduction des distances transportées…
La tenue de délais de réalisation de plus en plus serrés favorise également le recours aux solutions préfabriquées : un temps de mise en œuvre de l’ouvrage réduit de plusieurs mois impacte fortement l’équilibre économique d’une opération.
Cette dernière raison explique notamment le regain d’intérêt pour la construction hors-site des donneurs d’ordre tant publics que privés. Certains ont franchi le pas, pour des opérations de construction neuve mais aussi de réhabilitation, notamment dans des situations d’urgence (relogement, besoin accru pour les catégories spécifiques que sont les seniors ou les étudiants…).
« Le recours aux modules 3D peut apporter un vrai plus sur des chantiers de rénovation sur lesquels les habitants ne sont pas déplacés » explique Patrick Soubiran.
« Pour le compte d’un bailleur social bordelais, nous réalisons actuellement un chantier sur lequel tous les éléments de circulation verticale (escaliers, ascenseurs) sont rapportés à l’extérieur de l’ouvrage, dans des modules 3D ».
Et lorsqu’un chantier d’envergure s’achève 6 mois plus tôt que prévu, tel le chantier des deux tours Clement Canopy à Singapour, le gain économique est indéniable. En effet, pour ces deux tours de 40 étages (120 mètres de haut), Bouygues Bâtiment International a fait le choix de travailler en modules formés par l’assemblage d’éléments 2D fabriqués sur des sites dédiés, à quelques kilomètres du chantier.
L’assemblage hors-site d’éléments préfabriqués s’inscrit a priori dans une démarche d’économie circulaire : il présuppose un démantèlement de l’ouvrage en vue d’un réemploi ou d’une réutilisation.
Vers un nouveau mode d’organisation ?
Le renforcement de la construction hors-site implique une coopération renforcée entre concepteur et industriel fabricant, qui devront mutualiser leurs compétences et savoir-faire sous peine de compromettre le projet commun. Cette vision est d’ailleurs intégrée dans la loi ELAN du 23 novembre 2018 en apportant des dérogations à la loi MOP visant à promouvoir l’utilisation de la conception-réalisation. L’architecte, tout comme le bureau d’études, gardent toute leur place dans un procédé qui passe de la sous-traitance à la co-traitance dynamique. Si l’architecte apporte toujours sa vision de l’œuvre, la coopération renforcée avec l’industriel permet d’interagir efficacement pour apporter une réponse adaptée entre expression du besoin et faisabilité technique.
Quelques réalisations exemplaires, y compris dans les Travaux Publics
La Maison Abordable® Concrete Offsite®
La Maison Abordable® est un concept d’habitat innovant, reposant sur la construction hors-site. Les premières maisons, expérimentées dans la Sarthe et les Deux-Sèvres, se présentent sous la forme de 6 modules en béton d’environ 18 m² chacun, fabriqués en usine et assemblés sur site à raison de 3 pour le rez-de-chaussée et 3 pour l’étage de la maison, sans poteau ni mur de refend. Grâce à cette technologie hors-site, le hors d’eau est réduit à 3 jours au lieu de 3 semaines. Les modules en béton de la maison Ponant 3.0 peuvent se démonter facilement en vue d’un réemploi. En fin de vie, les aciers et le béton sont 100 % recyclables, le béton pouvant servir de granulats utilisés pour de nouveaux ouvrages.

Afin d’apporter des réponses efficaces aux collectivités qui doivent, dans des délais courts, proposer des solutions d’hébergement à destination de publics tels que les étudiants ou les populations...
Ponts et passerelles
Il y maintenant dix ans que l’architecte Rudy Ricciotti a fait le choix de la construction hors-site pour réaliser la Passerelle des Anges qui mène au Pont du Diable en plein cœur de l’Hérault. Avec une portée de 67,5 m pour 1,8 m de hauteur, soit un élancement de 1/38ème, la passerelle a demandé de nombreuses prouesses technologiques. Au premier rang, la portée : la passerelle nécessitait un franchissement de 69 m en une seule fois, sans appui intermédiaire, et pour réduire l’impact visuel, ni arcs, ni haubans. Défi relevé avec une solution en béton fibré préfabriquée, tant pour les deux poutres isostatiques parallèles formant le garde-corps que pour les 46 voussoirs. Il aura fallu trois semaines de montage et 6 ouvriers pour assembler les 144 tonnes de l’ouvrage.
Plus récemment, aux Pays-Bas, la ville de Kampen s’est dotée d’un pont en béton entièrement démontable. Constitué de 40 modules de 2,5m sur 1,5m, cet ouvrage a été conçu dans l’optique de pouvoir être démonté pour permettre un accès temporaire à un chantier de maintenance, sans bloquer la circulation dans cette région caractérisée par un trafic routier dense et des axes routiers restreints, traversés par de nombreux canaux. Chaque pièce est démontable, réutilisable. Mis en service en début d’année 2019, le pont est en phase d’analyse, pour envisager un déploiement plus large sur d’autres sites néerlandais.
COMMENTAIRES
LAISSER UN COMMENTAIRE