Fours de cimenteries : en route vers la sobriété énergétique
L’industrie cimentière investit régulièrement dans l’amélioration de ses fours de production. L’enjeu est double. Il s’agit d’une part d’en optimiser la productivité, et d’autre part d’en améliorer l’efficacité énergétique. De l’étanchéité à l’air à la mise en œuvre de technologies innovantes en passant par la maintenance régulière des installations ou les projets de R&D, les pistes d’optimisation énergétiques sont nombreuses.
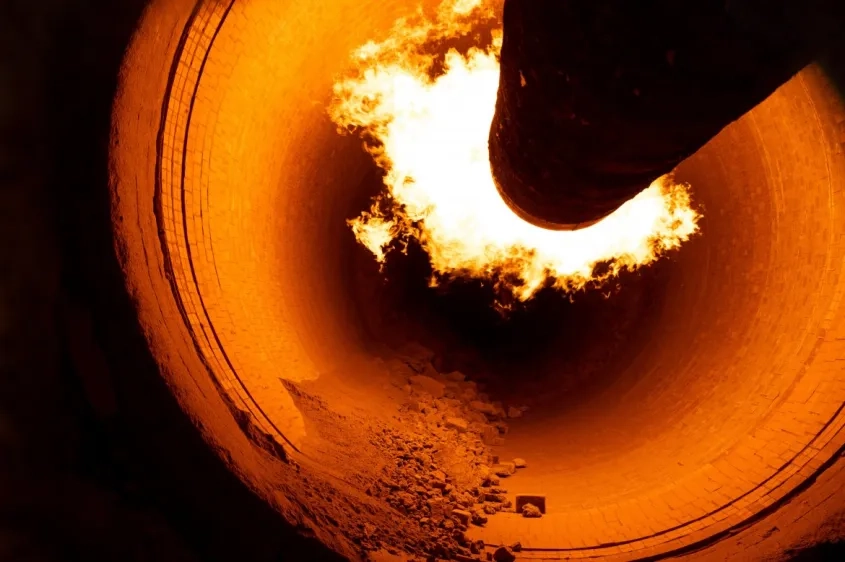
1ère optimisation énergétique des cimenteries : opter pour la meilleure technologie industrielle
La fabrication de ciment est opérée selon deux types de procédés principaux : par voie humide ou par voie sèche. La voie humide, qui conduit à ajouter de l’eau au mix de matériaux avant de devoir l’évaporer, s’avère excessivement énergivore. Elle a ainsi été peu à peu abandonnée au profit des procédés par voie sèche, qui consomment au minimum deux fois moins d’énergie. Ainsi, seule une dizaine de cimenteries par voie humide subsiste sur les quelques 3 000 cimenteries implantées actuellement dans le monde.
2ème optimisation énergétique des cimenteries : optimiser l’étanchéité à l’air de l’installation
Le four utilisé pour transformer la farine crue en clinker à haute température (1450°C) est constitué d’un long tube tournant en acier. A son entrée, le four est connecté à la tour de préchauffage et à sa sortie, au capot de chauffe, qui intègre la tuyère principale. A la jonction entre ces trois éléments peuvent apparaître des interstices permettant à l’air frais extérieur de rentrer dans le four, et à l’air chaud du four d’en sortir. Ces deux circulations d’air ont le même effet néfaste : elles réduisent largement l’efficacité énergétique du four. C’est pourquoi les opérateurs de la cimenterie veillent en permanence à la parfaite étanchéité de l’installation.
3ème optimisation énergétique des cimenteries : organiser la maintenance régulière du four
L’intérieur du tube du four est tapissé d’une multitude de briques réfractaires. Ces matériaux minéraux sont dotés d’une grande inertie thermique qui permet de conserver la chaleur à l’intérieur du four, minimisant ainsi les pertes par rayonnement. La surface de ces briques subit une usure dans le temps liée au frottement des particules de matière en circulation et à la chaleur. Lorsque leur épaisseur devient trop faible, les briques perdent leur pouvoir isolant, ce qui diminue l’efficacité énergétique du process. C’est ainsi que chaque année, le four est arrêté pour une opération de maintenance globale, au cours de laquelle les briques usées sont remplacées.
4ème optimisation énergétique des cimenteries : doper la performance de l’installation
En sortie de four, les « cailloux » de clinker sont extrêmement chauds (plus de 1 000°C). Ils tombent alors dans un refroidisseur, une installation dans laquelle est soufflé un air frais qui, en abaissant rapidement la température des matériaux à 80°C, se charge de leurs calories. Devenu chaud, cet air est récupéré et réinjecté dans le process, ce qui permet de diminuer les consommations du four. Investir dans un refroidisseur efficace est donc essentiel pour améliorer le bilan énergétique de l’installation.
Les cimenteries à voie sèche modernes intègrent également une source de production de chaleur secondaire située dans la tour de préchauffage : le précalcinateur. Doté de sa propre tuyère, alimenté par l’air chaud issu du refroidisseur et par des combustibles alternatifs (déchets, biomasse...), cet organe « précuit » le cru avant son entrée dans le four, permettant de diminuer de plus de 30 % la consommation énergétique et les émissions de CO2 du process.
5ème optimisation énergétique des cimenteries : investir dans la R&D
L’industrie cimentière travaille en permanence sur l’amélioration continue de ces process industriels, notamment à travers des projets de R&D de grande ampleur. Les pistes pour réduire la consommation énergétique sont nombreuses. Parmi les plus prometteuses, on peut en citer trois :
- L’élaboration d’un clinker nécessitant une température de chauffe moindre : 1250°C au lieu de 1450°C, avec une réduction drastique des consommations et des émissions carbone à la clé.
- Le remplacement des combustibles carbonés de la tuyère par différentes sources d’énergie : solaire, grâce à la technologie des fours à concentration solaire, ou électrique, grâce à l’installation d’une torche à plasma.
- La récupération du CO2 en sortie d’installation. Le CO2 contenu dans les fumées en sortie cheminée est concentré à hauteur de 10-15%. Ce volume de CO2 concentré pourrait être capturé (on parle de Capture CO2) et devenir une nouvelle ressource pour d’autres industries (croissance de biomasse, production de boissons gazeuses...).
- Le pilotage des installations par de l’automatisme avec des systèmes dits « experts » qui pilotent les fours (ou les broyeurs) directement (sous la surveillance d’opérateurs) en optimisant les paramètres de conduite en tout temps.
COMMENTAIRES
LAISSER UN COMMENTAIRE